
In the race for improved electric motors for e-mobility and wind power, axial flux motors are receiving a lot of attention for their innovative capabilities in delivering high-density power in a smaller, lighter package. This article looks at the developments and offerings of several companies involved in bringing new innovations to axial flux motors- Maxnax of Belgium, Ashwoods Electric Motors of England, Emrax of Slovenia, and AVID Technology in the UK. Another key player, YASA in the UK, is covered in a related article.
One company that is receiving serious attention its innovative design work is Belgian startup Maxnax bvba. As with axial flux motors generally, its motors are designed to provide new levels of power density resulting in much lower overall weight and size. While squarely targeting the EV automobile market, Maxnax is also designing its motors to be applicable for electric industrial machinery such as wind turbines, mining and agricultural vehicles, and motorbikes. The company is located in Kortrijk near Ghent.
Axial Flux “direct-drive machines”, as Maxnax refers to them, are based upon a fundamentally different approach to direct drive than is represented by traditional radial flux systems. Put two sets of magnets parallel to each other, perpendicular to the axis of rotation. This axial-flux topology provides machines that are less wide and heavy as well as being more compact, yielding greater efficiency.
According to Maxmax, its motor is 50% to 75% lighter than radial flux direct drive machines for similar power. The company began with a focus on wind energy applications, designing a motor that becomes a generator. Now it focuses on smaller high-speed motors, developing designs for EV applications including cars, trucks, buses and motorcycles.
Founded by Peter Leijnen who serves as CTO, the company now has about 9-10 employees. So far, it has concentrated on making prototypes for various OEMs and taking reservations for its first series production model which it is has been targeting to begin manufacturing in the second quarter of this year. This will be the AXF275 which targets e-mobility applications.
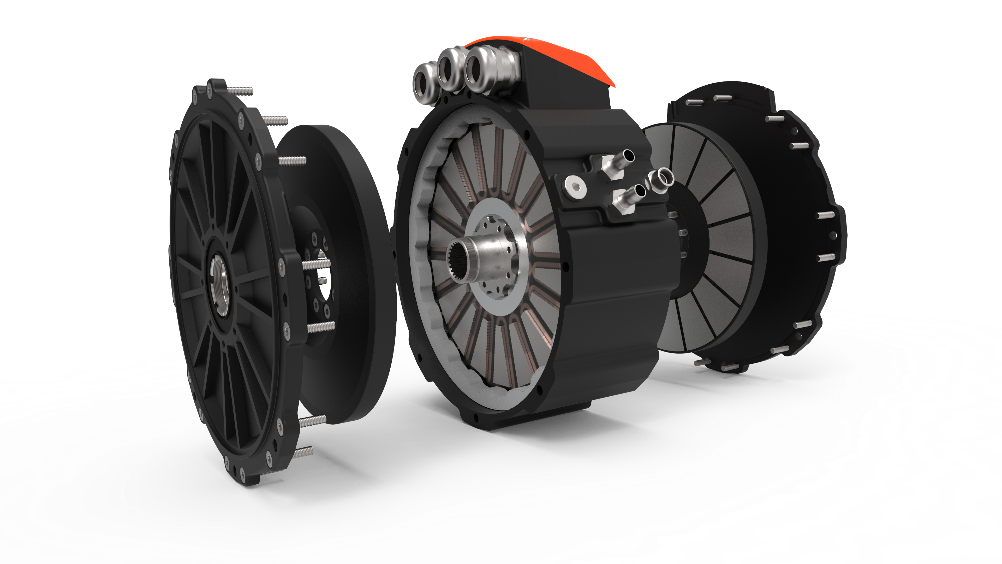
Its yokeless axial flux motors deliver scalability and extreme power densities for e-mobility, according to Daan Moreels, also a co-founder, who serves as business development officer. They use Neodymium N45SH magnets in amounts which vary for each motor type, said Moreels. “Compared with traditional radial flux permanent magnet motors, we typically need up to 40% fewer permanent magnets for similar torque, he noted. The magnets are sourced from standard supply resources.
The key to the power density is the yokeless axial flux design with two rotors at each side of the machine. According to Magnax, this shortens the flux path while the magnets are farther away from the axis, resulting in greater efficiency and leverage around the central axis. There is zero overhang of loops on the windings making them fully active. The design is scaleable from small motors for electric vehicles to large wind-turbine generators. Characteristically, they perform well at a broad range of rotational speeds, making them suitable for high-speed-low-torque and low-speed-high-torque applications. For more information, see www.Magnax.com.
Avid Technology in the UK
In the UK, a permanent magnet axial flux motor from Avid Technology is shaking up things in the EV market. The company reports a surge in new orders for its EVO motor since it acquired the rights from its developer GKN Hybrid Power to manufacture it for the automotive market and further develop it for new applications. Now it has brought in-house design, development and production for the EVO.
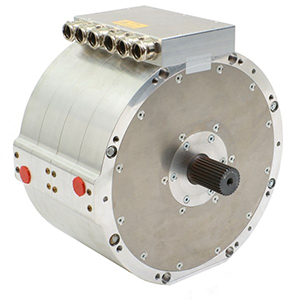
EVO axial flux electric motors have one of the highest usable power and torque densities of any electric vehicle drive motor available on the market today and are suitable for a range of high-performance drivetrain applications, says the company. The EVO can be used in conjunction with custom built or standard inverters, the company notes, while it can deliver a variety of integrated solutions for OEM applications for traction, generator and accessory drive.
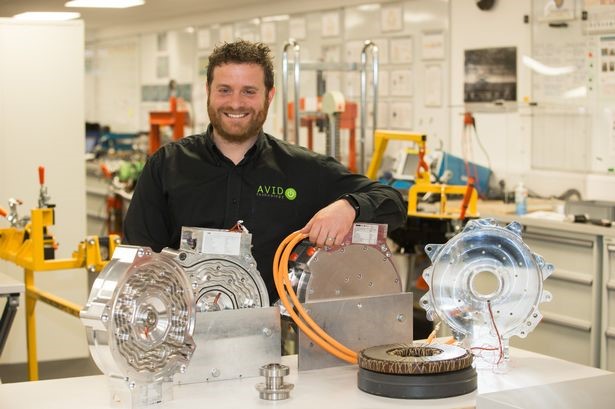
Avid reported it has seen a sharp increase in demand for the EVO with exports to Germany, Poland, Spain, US and Asia already in the pipeline. In May, the company reported that it had already signed contracts for more than $65 million in orders for the year for the motors alone.
“It’s been a fantastic start to the year for the business and extremely rewarding to complete our first EVO shipment,” said Ryan Maughan, managing director. “The last 12 months have been tremendously exciting in terms of sales growth through a variety of new opportunities. We are proud to be working with some of the largest commercial vehicle manufacturers in the world to design and deliver their electric and hybrid vehicles of the future.”
“After securing the license with GKN we invested over 4 million Euros to expand our production and testing facilities. This investment has increased our manufacturing capabilities to enable us to meet the rising demand we’re seeing in our primary commercial and passenger vehicle markets.”
The company has now completely transferred production to its plant in Cramlington, Northumberland, and is developing the existing EVO technology to create new variants of the motor for a variety of alternative applications. “Most recently we’re experiencing an increase in demand for our technology in the robotics and aerospace industries globally. This has been possible due to our market-leading high-power density motors and electronics solutions which can bring tremendous improvements in functionality and efficiency in robotic systems and aerospace applications.”
For more information, see www.avidtp.com.
Emrax of Slovenia
One of the longest-running manufacturers of permanent magnet axial flux motors is Emrax d.o.o based in Kamnik, Slovenia, formerly known as Enstroj. Its first axial flux prototype motor, named Emrax, which stands for Electric Motor Roman Axial flux, was made in 2008 to power a pioneering electric airplane. Since then the company has grown, changed its name to match that of the product line, and developed the Emrax line to five sizes.
The company added its smallest and largest units in 2016– the smallest being Emrax 188, which has diameter 188 mm and axial length 77 mm and the biggest, EMRAX 348, which has diameter 348 mm and axial length 107 mm. As other Emrax motors they both have a significantly high-power density, which is up to 9 kW/kg.
The small model is well suited for the electric drive system installed in motorbikes. Still, it is high powered (70 kW peak, 30 kW continuous) and, despite its smaller diameter light weight, it has 100 Nm peak and up to 50 Nm constant torque.
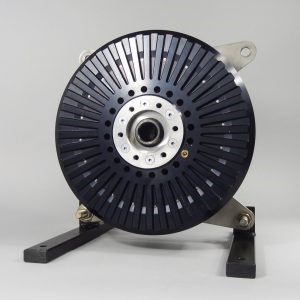
Ashwoods Electric Motors Ltd
Another established manufacturer of permanent magnet axial flux motors is Ashwoods Electric Motors Ltd based in Harcombe Cross, England. The company produces both radial flux and axial flux machines, providing its efficient permanent magnet electric motors across a range of sectors including materials handling, off highway, automotive and marine.
The company’s axial flux motor range includes the Elmo-S (air cooled) and Elmo-D (liquid cooled) motors that suit a wide array of applications and power requirements.
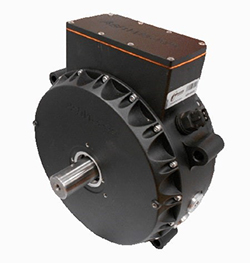
Typical for an axial flux motor, the magnetic field is applied along the rotor axis, parallel to the shaft. The motors incorporate a unique stator and rotor design with surface mounted permanent magnets to deliver high power at efficiencies far superior to high-performing induction motors, says the company. This lightweight and compact design contributes to the motors’ extremely high torque density. This, coupled with its excellent direct transmission drive characteristics, makes it ideal for high power and torque applications.
Its first axial flux motor was produced in 2011. The company as it is known today was founded in 2012 and became ISO 9001 certified in 2013. Just a year later, its first IPM motor was developed and then commercialized in 2016.
Last spring it moved into its present location which, due to its size and significant equipment investments, brings to the company a dramatic new capability for high-volume manufacturing. Perhaps most significant was its investment in a brand-new and custom-built stator production machine that is highly automated. According to the company, it can wind up to six teeth simultaneously at 300rpm – much improved on the current process. The positioning of the wire can be controlled to 0.01mm and the automated ABB robot is accurate to 0.02mm.
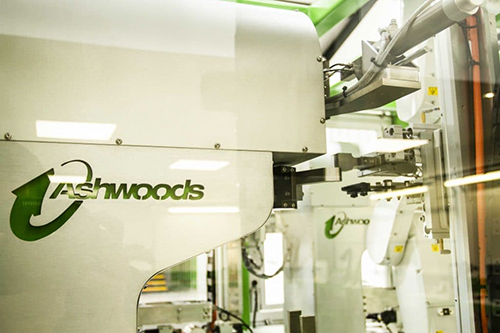
The company’s internal permanent magnet (IPM) motors are radial flux machines, as the magnetic field is applied radially inward and outward from the rotor. These incorporate the magnets directly into the rotors. They are designed to be relatively low cost, scalable motors for use within high volume applications. Use of AC technology enables the motor to be a third of the size and weight of typical induction and brushed DC motors, while still offering the benefits that accompany permanent magnet technology. With a range of standard and custom motors available, the IPM motors can be integrated into many materials handling, automotive, off-highway and industrial applications.
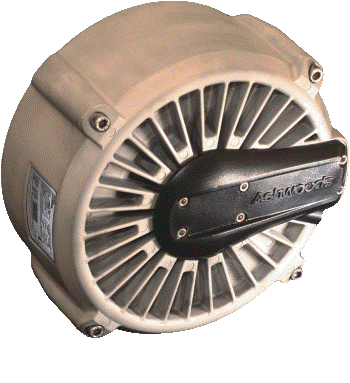
The IPM motors incorporate magnets embedded within the rotor enabling them to produce reluctance torque, this contributes to the motors being capable of producing considerable amounts of torque with very minimal magnet material. The unique design allows for field weakening to improve high speed performanc-producing near peak power at speeds from 2000 to 6000 rpm. For more information, see www.AshwoodsElectricMotors.com