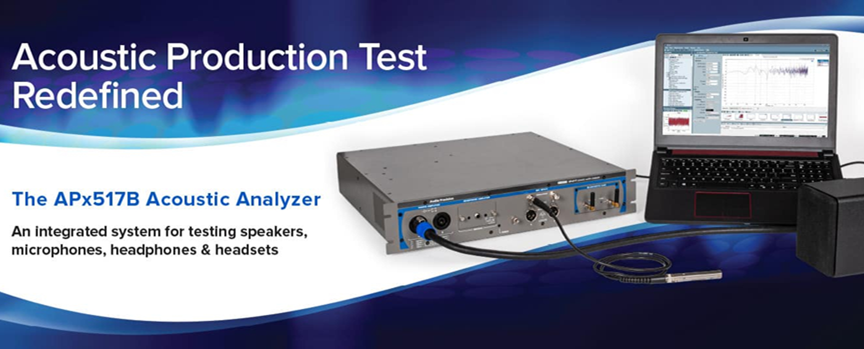
If magnet material chips loose during the manufacture of speakers it can cause what audio designers call a “buzz defect”. This can be an onerous problem to detect but new software from instrument maker Audio Precision raises the bar for doing so.
The improvement comes in the latest update to the company’s APx500 audio measurement software, version 6.1, for production test of loudspeakers, headphone drivers, and microphones. Most importantly for designers and manufacturers of speaker drivers, and products incorporating them, the software now covers all the standard techniques for detecting “rub and buzz” defects.
“Simply put, APx audio measurement software now offers the broadest set of rub & buzz defect detection methodologies available,” said Daniel Knighten, general manager of Audio Precision. The term is commonly used to describe any one of several possible manufacturing defects that cause undesirable noises to be emitted during speaker operation. Rub-related noises occur when the speaker cone is off-center or canted and mechanically rubs when it moves to create sound. Buzz defects occur when loose particulate matter such as chipped magnet material or bits of glue are trapped in the gap between the speaker’s voice coil and the cone.
As an audible defect in a speaker driver, or device incorporating a speaker, rub & buzz presents several challenges to device manufacturers, the company explains. First off, it is a subjective issue, with little broad-based agreement on how much is too much – the noises created by a specific defect can be perceived very differently by different listeners. Compounding the issue is the level of distortion in a typical speaker is far greater, and more diverse, than in a typical electronic device and can mask these defects. This latter point means the standard audio measurements of frequency response and distortion will only detect the most severe cases of rub & buzz.
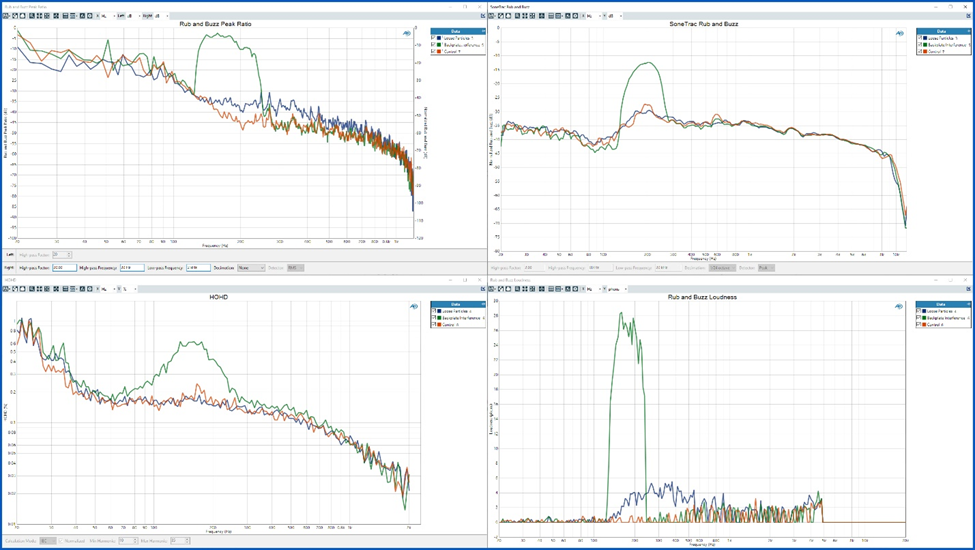
So, with rub & buzz defects, you have imperfections in a speaker that can negatively impact a listener’s perception of the speaker’s quality, but those defects are not necessarily detectable by traditional audio measurements. To address this issue, several different rub & buzz detection methodologies have been developed within the industry: various approaches using high-pass tracking filters, distortion-oriented methods that focus only on high-order harmonics, and techniques applying human hearing-based algorithms to the distortion signal. While all these methods are applicable to rub & buzz detection, no single method has achieved uniform adoption in the industry.
- Rub & Buzz – Previously available in APx software, this method uses high-pass tracking filters to remove the fundamental signal and detect defects as excursions in the residual waveform’s crest factor or peak ratio.
- SoneTrac (new with v6.1) – A Bose-developed improvement to Rub & Buzz, this method filters the residual signal and ratios it to the RMS of the total signal to reduce the noisiness of the measurement result.
- High-Order Harmonic Distortion (HOHD; new with v6.1) – A classic method for rub & buzz detection, HOHD uses the THD (Total Harmonic Distortion) ratio but only of harmonics above the 10th, 10-35, 20-200, etc., which is a simple way to account for frequency masking effects.
- Rub & Buzz Loudness (new with v6.1) – Applies a psycho-acoustic loudness model to the residual signal to calculate the perceived level of the rub and buzz based on well-established models of the human perception of sound.
- Audio Precision is a brand of electronic audio and electro-acoustic test instrumentation made by Axiometrix Solutions, based in Beaverton, Oregon. Other major brands of the company are GRAS Sound & Vibration and imc Test & Measurement. For more info, see www.ap.com.