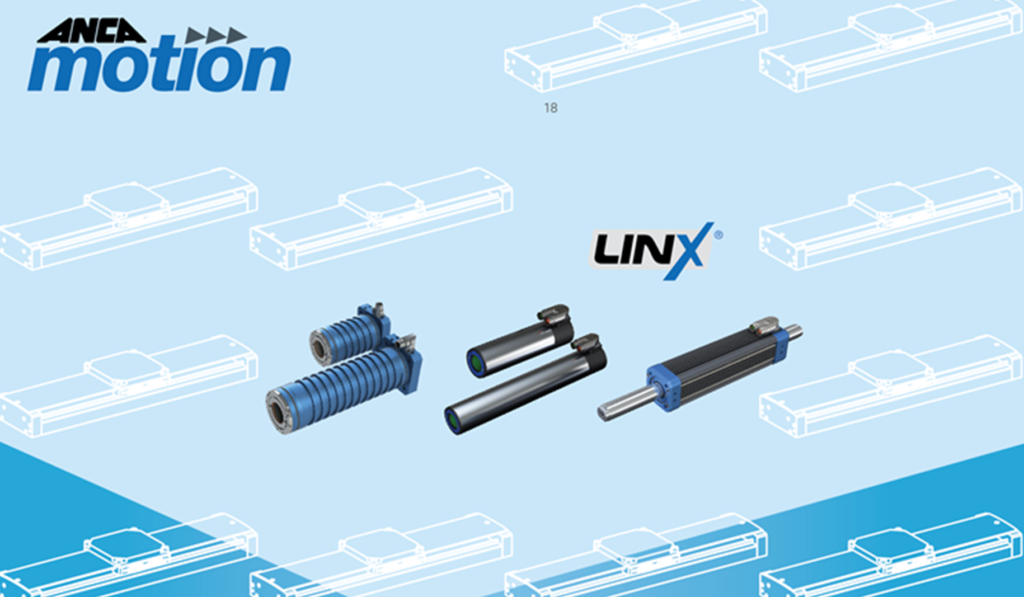
With the tubular structure of its LinX motors, ANCA Motion maximizes the magnetic flux generated by the permanent magnets contained in their stainless steel shaft. Employing the full shaft surface for magnetic force, the motors provide several key benefits over flat linear motors for a variety of automation applications.
The Australian company’s LinX range of tubular linear motors has its origins in tool grinding machines, but their features make them a match for a range of automation applications including packaging, food and beverage manufacturing, printing, pharmaceutical, rollforming, textile production, and test and measurement. ANCA Motion’s sister company, ANCA CNC Machines, introduced tubular linear motors in 2014 for its FX Linear and MX Linear machines.
As a replacement to retrofit pneumatic cylinders, the LinX M-series motors are designed to be fully compatible with standard pneumatics accessories, such as mounting plates, linear guides and coupling pieces. Going from flatbed to tubular actuation significantly improves thermal stability.
“Because the motor is floating in the machine structure, that enables us to put a water-cooling jacket around the motor and completely take the heat out of the motor,” according to Heng Luo, product manager. “That’s a vast advantage from a thermal perspective compared to a flatbed.”
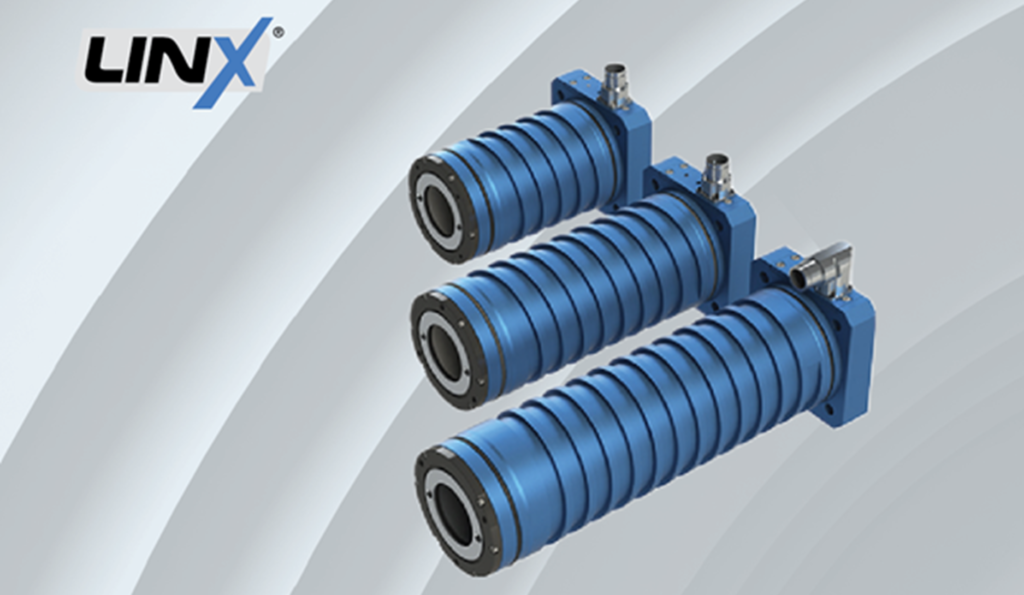
The motor consists of a shaft containing magnets and a forcer containing wound copper coils. The symmetric design results in zero attractive forces between the forcer and shaft, greatly reducing the loading requirement on support bearings.
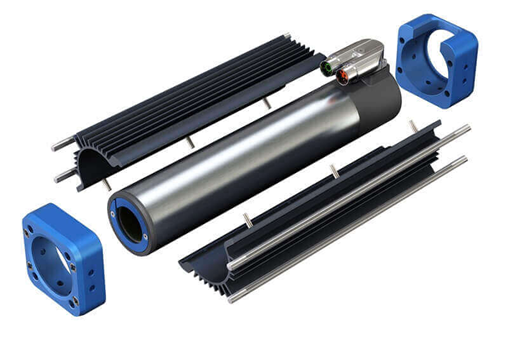
“The traditional linear motor is flat in construction, which creates many issues when implementing these motors on machines,” said Phillip Wysocki, electrical systems engineer. “Machines with flatbed linear motors typically require a separate chiller for thermal stability, and the attractive force between coil and magnet bed creates tremendous downforces on the bearings, making everything wear faster and decreasing efficiency. In addition, flatbed style linear motors used in grinding machines typically have a back-iron in their magnetic circuit, further increasing the downforces and creating cogging.”
With the engineering head office in Australia and a global presence in more than 40 countries worldwide, ANCA Motion employs 100 staff of which 60 are based in Australia. For more info, see www.anca.com.