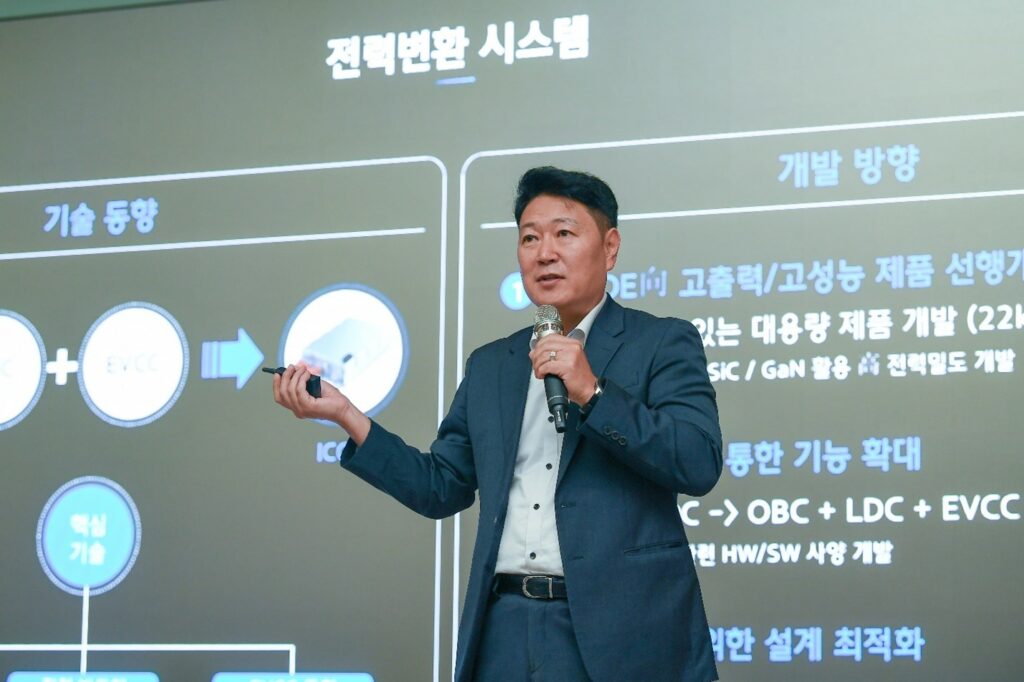
Tier-1 components manufacturer Hyundai Mobis is striding forward aggressively to build a leadership position in automotive electrification. New efforts unveiled in October include plans to build another major new electrification plant in Europe, plus a roadmap for advanced technology development with design of innovative drive systems, electromagnetic systems and nickel-free materials for inductors among the key elements.
On October 15, it agreed to establish its first European power electric (PE) system production base in Novaky, Slovakia. The plant will have an annual production capacity of 300,000 units, with completion targeted for the second half of next year. It follows previous electrification sites in the Czech Republic and Spain. The move comes in response to rising protectionism and the adjustment of automakers’ EV transition pace in Europe, with Hyundai Mobis taking a proactive approach through local investment and market localization to capitalize on global electrification opportunities.
A PE system is a key component of an electric vehicle (EV) that drives the vehicle and replaces the engine and transmission of a conventional internal combustion engine. Components include motor, speed reducer, inverter, and battery. The motor generates torque as soon as it starts to rotate. The PE system integrates the motor, decelerator, and inverter into a single unit.
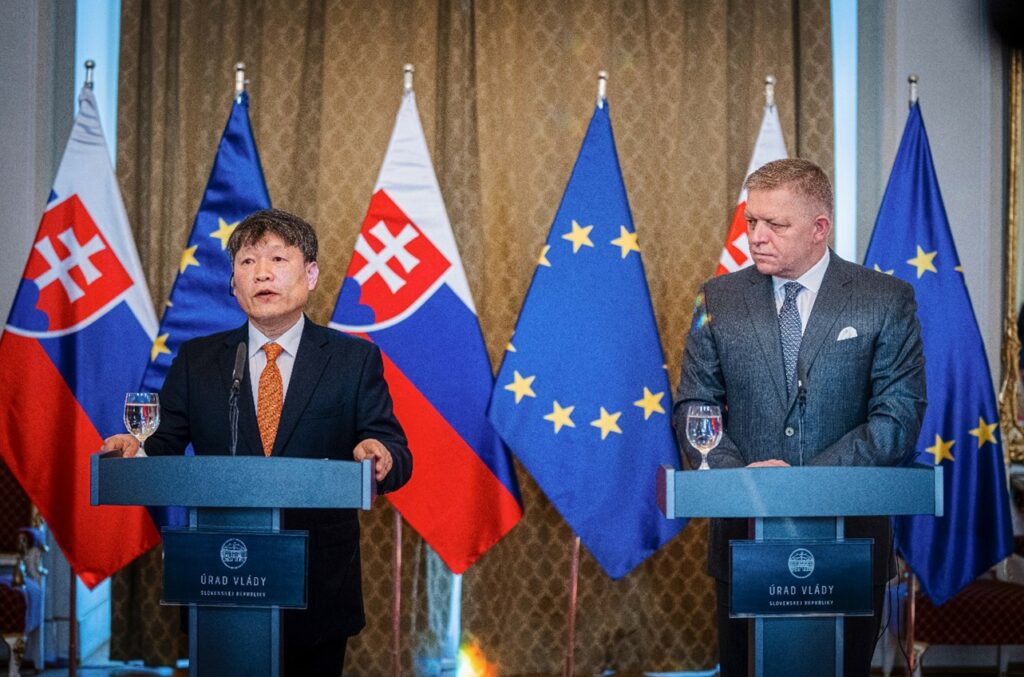
The new production base will involve an approximately KRW 350 billion investment. The plant will occupy a site of approximately 105,700 square meters (equivalent to 14 soccer fields), with KRW 250 billion dedicated to its construction, which is slated for completion by the second half of next year. Once operational, the plant will have the capacity to produce 300,000 PE systems annually for the European market. An additional KRW of 95 billion will be invested in constructing new facilities for producing braking systems and airbags within the existing Zilina plant.
Slovakia is home to several global automakers, including Kia which is also building an EV-dedicated plant in the country. Hyundai Mobis plans to leverage its new electrification hub in Slovakia as a strategic foothold for expanding its presence in the European EV market. In addition to Europe, Hyundai Mobis is expanding its electrification bases worldwide. In response to the growing North American EV market, the company plans to begin operating new battery system and PE system production facilities in the region during the second half of this year. Currently, the South Korea-based company operates electrification production hubs in nine locations globally (six domestic and three overseas) and is establishing six new electrification production hubs in South Korea, North America, and Indonesia.
Nickel-free metal for inductors part of innovative materials development
It is accelerating the development of new materials that use fewer rare metals like nickel while enhancing performance. Recently, its scientists and engineers developed a new material that reduces the use of expensive nickel metal in inductors, a key component in power conversion for electric vehicles. While inductors are typically made from metal powders mixed with nickel, they successfully reduced the nickel content from the previous 50% to the 30% range. Amid a sixfold increase in nickel prices over the past decade, this new material minimizes raw material price volatility while ensuring electromagnetic properties. Going further, Hyundai Mobis has embarked on evaluating a new material that is completely ‘nickel-free’, the first of its kind globally.
The company is also focused on developing new materials to enhance competitiveness across all electrification and electronic components fields, including high-speed charging battery cooling technology, electromagnetic shielding materials, and surface coating technologies for autonomous driving sensors. There are more than 100 research and development professionals in materials science at work at the company, part of a global R&D workforce exceeding 7,000 people.
At a presentation on October 4 at its Uiwang Research Center, the company unveiled 65 mobility technologies slated for commercialization within the next two to three years, highlighted by efforts in autonomous driving, connectivity and electrification. It was held at the Electrification Research Building, a specialized research facility dedicated to next-generation electrification technologies completed at the end of last year which plays a pivotal role by consolidating the development of key electrification components including R&D, testing and evaluation, and quality analysis, all under one roof.
The three core development strategies for electrification components focus on drive systems, battery systems and power conversion systems. The drive system is represented by a 3-in-1 integrated drive system combining motors, reduction gears, and inverters. Key focuses include miniaturizing the system, high-efficiency electromagnetic design, oil cooling, and power module technology. The power conversion system strategy focuses on developing the next-generation Integrated Charging Control Unit (ICCU), which incorporates the Electric Vehicle Communication Controller (EVCC). This advancement is expected to realize Vehicle-to-Everything (V2X) connectivity for electric vehicles, linking cars with charging infrastructure and smart home functionalities. Concurrently, Hyundai Mobis is accelerating the development of necessary power semiconductors. For more info, see www.mobis.com.