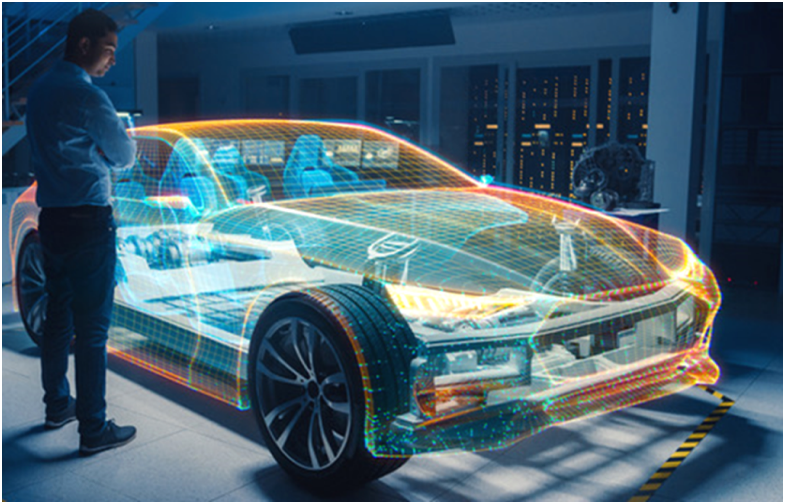
Few companies can match the product development pace of Wells Vehicle Electronics, a manufacturer of electronic products for the automotive industry. Many are magnetic and electromagnetic components such as an innovative rotary position sensor that it recently developed. The products are manufactured in a versatile, modern plant flexible enough to accommodate small production runs to highly automated runs for large-volume orders.
In April, it introduced 1,802 new parts including a variety of sensors, switches, solenoids, coils and voltage regulators for light and heavy-duty vehicles. Last year it introduced 1,200 new parts, 449 of them in December.
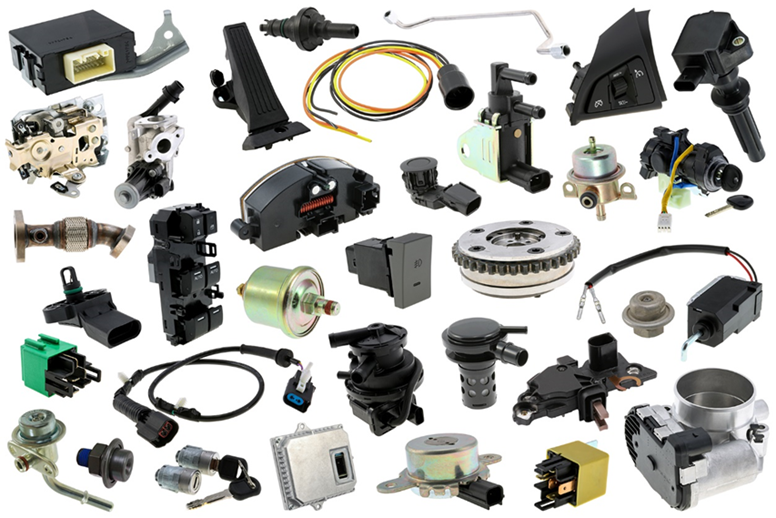
The most recent batch of new products, depicted above, included 696 switches, 428 fuel system products, 397 sensors, 245 emissions products, 21 coils, 12 solenoids, and 3 voltage regulators. “The addition of these new part numbers for April furthers our commitment to providing a full line of professional-grade vehicle electronics and engine management products for our customers,” said Patrick Sommerfeld, vice president of sales and marketing.
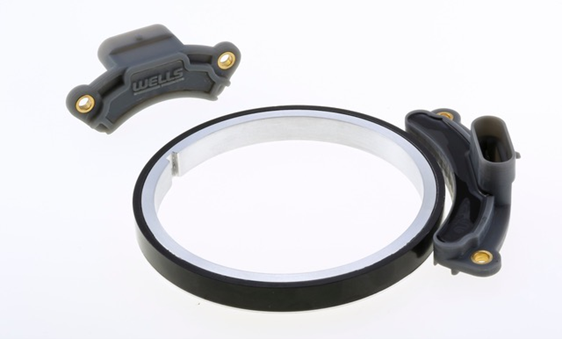
An example of the creative product development and flexible manufacturing strategy is a new line of rotary position sensors for EV powertrains that was introduced in September by its Wells Engineered Products business unit. As an alternative to conventional transformer resolvers and variable reluctance resolvers, they use hall-effect sensors two-axis sinusoidal magnetization to deliver higher accuracy in a smaller, lighter package.
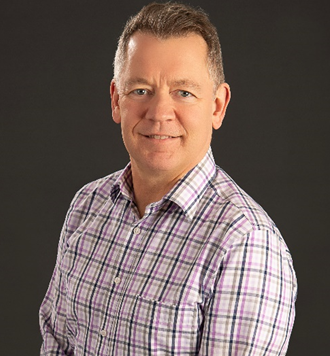
“Because controllability, performance and smooth torque are all critical for EV performance, accurate measurement of rotor position is essential,” said Greg Burneske, director of Wells Engineered Products. “Our rotary position sensors are more compact than a traditional VR resolver and integrate readily into new or existing motor designs, including hub motors, giving EV traction motor designers opportunities for improved designs with higher performance at a lower cost.”
They feature a semi-circular package for space-constrained applications, making them adaptable to various mounting techniques and locations. According to its comparison data, rotor mass is <100 g compared to 155 g for a VR Resolver. Protected by multiple patents, the sensor performs the same core function as the resolver but does it better while costing less and taking up less space. The comparison refers to an application with a 96mm OD shaft on a 12-pole pair PM AC synchronous motor. The original VR Resolver uses a 12-lobe rotor for electrical pole pair matching.
Our team of engineers understand that every application is different, the company says. Maximizing performance means tailoring the sensor. The new sensor was designed with customization in mind. Mounting method, layout and even sensor outputs are all adaptable to suit motor design, even hub motors.
Prototypes can be produced to tight timescales using 3D printing and other rapid technologies to get the sensors in testing or customer hands quickly. Well-equipped test facilities and ISO 17025 certified validation labs are used to ensure performance and durability for the application. The sensors can be manufactured on highly automated equipment for volume orders, but the company’s processes are also configurable for small and medium production runs.
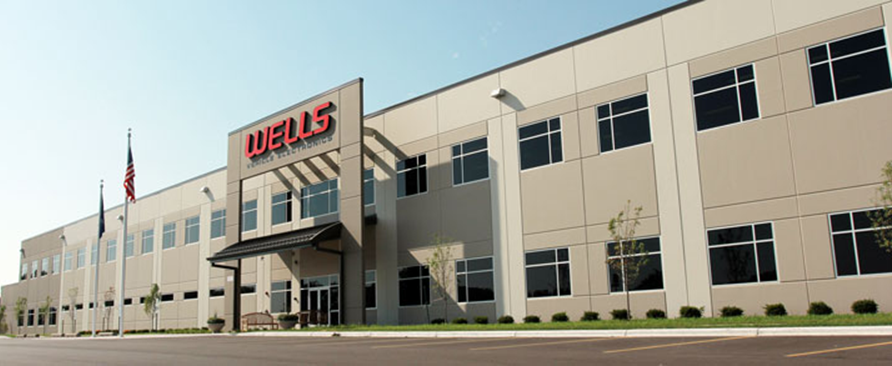
As a business unit of Wells Vehicle Electronics, Wells Engineered Products provides custom precision engine management and power control products for manufacturers of premium vehicles, power generation and industrial equipment throughout North America. It partners with automotive manufacturers and their Tier 1 suppliers, as well as smaller sectors. Located in Fond du Lac, Wisconsin, the company is a division of NGK Spark Plug. For more information, see www.wellsve.com and www.wellsengineeredproducts.com.