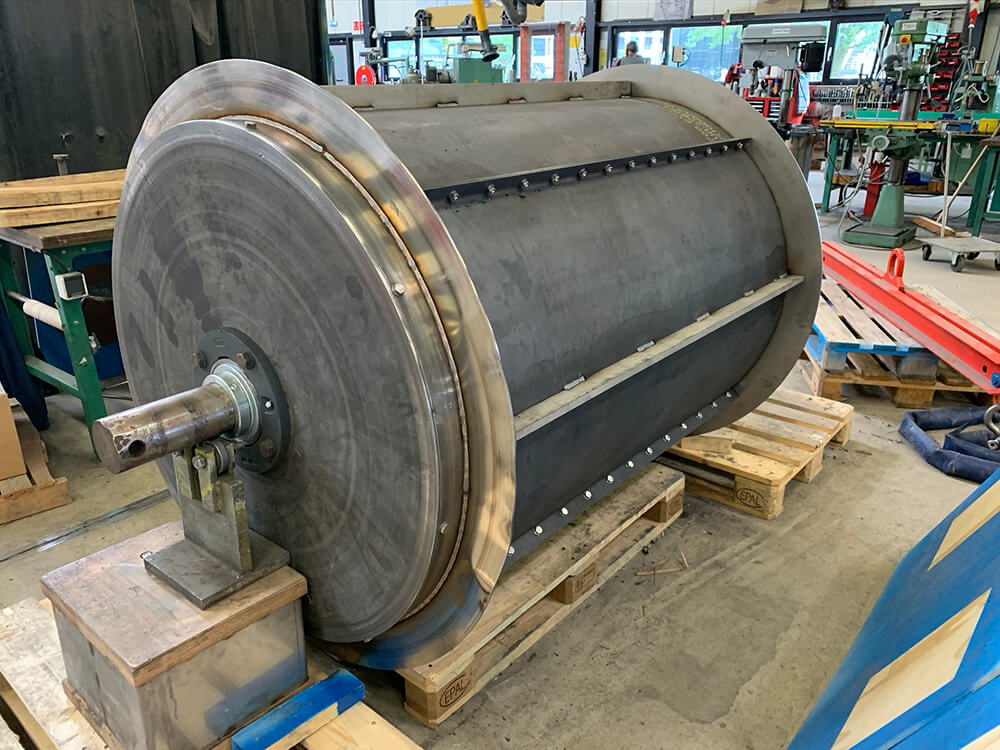
Difficult to remove
The production site in Wielsbeke currently uses 50 percent recycled wood in its chipboards and wants to increase this to 75 percent. To do that, the plant not only needs more recycled wood. It also needs to optimize the cleaning of the wood it brings in. This is often contaminated with stones, plastic, glass and also ferrous metals. In particular, it is difficult to remove the wood blocks containing these ferrous metals (materials in which iron is the main component).
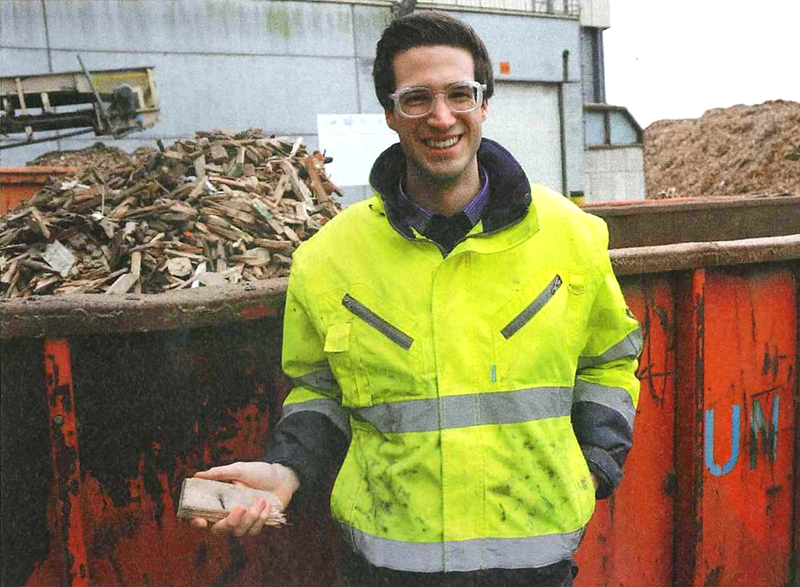
Optimize the process
“From a thorough analysis of the entire recycling process from the supply of the wood, the removal of the wood blocks containing ferrous metal with the existing drum magnets proved to be the biggest problem,” acknowledges Martijn Lambregts, maintenance engineer at Unilin’s Panels division.
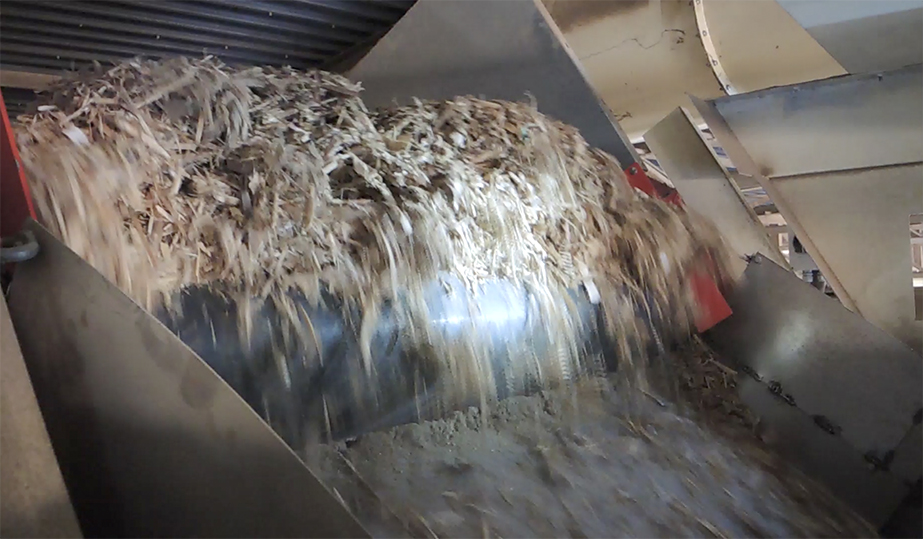
At the end of the recycling line, a block magnet hangs above the conveyor belt that leads to the chipping plant. The block magnet serves to check the material being fed in. This is where the problem became clearly visible.
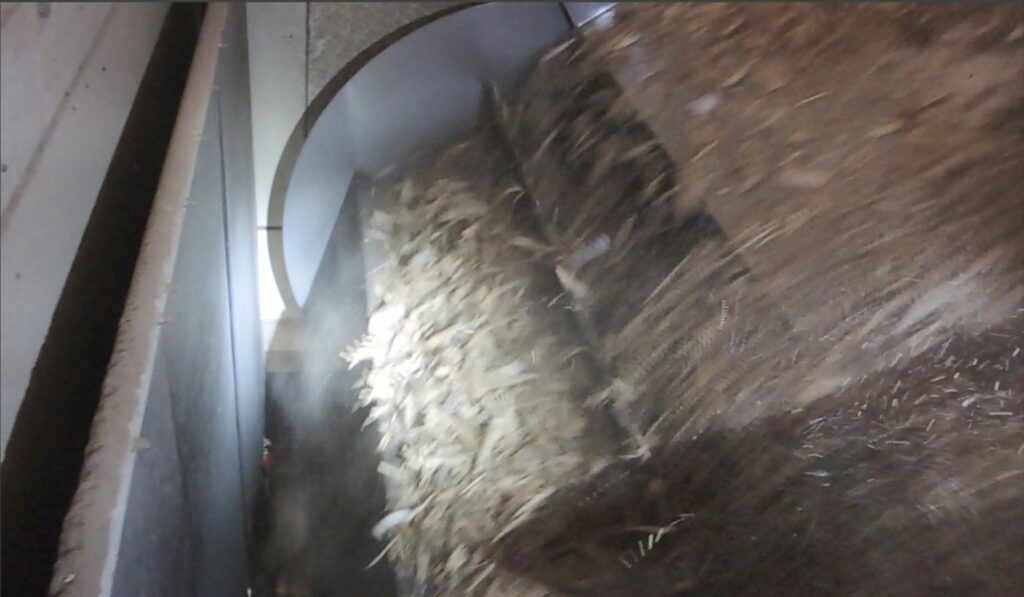
Lambregts: “Too many wooden blocks with nails in them, for example, were hanging on the block magnet. This meant that in practice wood blocks also went through to the chipping mill, resulting in higher wear and tear on the blades and a greater risk of sparks, and therefore fire. In addition, we want to avoid ferrous particles getting into the chipboard itself.”
To optimize the process and make it safer, Unilin sought cooperation with Bakker Magnetics. Together, they designed a super-strong neodymium drum magnet for removing wood with embedded ferrous metals. Neodymium magnets are the strongest permanent magnets available.
Magnetic and a non-magnetic half
“For the strongest possible magnetic field with a wide capture field, across the entire width of the feed chute, the magnet consists of neodymium of the highest gradation,” says Ibo Serbest, sales engineer at Bakker Magnetics.
This motor-driven drum magnet consists of a static magnetic core positioned at an angle of 180 degrees. This means that inside the drum there is a magnetic and a non-magnetic half. The drum rotates at a frequency of about 35 rpm.
On the magnetic half of the drum, the material flow is deposited. Magnetic materials such as ferrous metals in wood, such as nails, and deformed stainless steel will “stick” to the drum due to the magnetic field. Once the magnetic material leaves the magnetic field, it is collected separately.
Cleaning process
In the cleaning process of the recycling wood, drum magnets have been installed at two locations, including those of Bakker Magnetics. The first drum magnet removes in the preliminary stage with high efficiency all ferrous metals not contained in wood from the material flow on the conveyor belt. This flow also contains glass, plastic and stones.
The material is transported over screening machines with increasingly finer meshes. It again passes through drum magnets, which transport fractions of a certain size to so-called heavy goods separators. Then eddy current machines separate the non-ferrous metals (aluminum and copper).
The project presented Bakker Magnetics and Unilin with a number of challenges. The design, the configuration of the magnetic drum and the selection of the magnets caused the most headaches, indicate Serbest and Lambregts. The latter also mentions the installation, carried out by Unilin’s technical department.
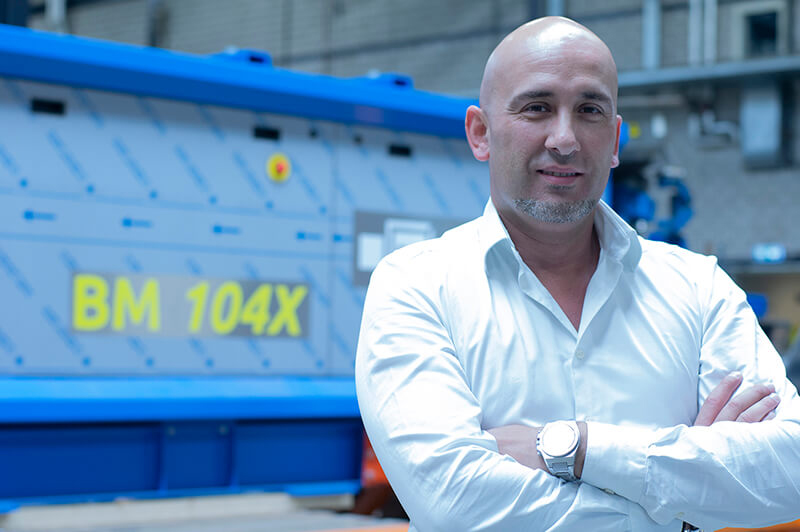
“This had to be done with the utmost care and supervision, since the magnetic field is extremely powerful,” Lambregts says. “For example, no magnetic tools were allowed to be used. The danger here is that the mechanic could injure his fingers or hand. Also, mechanics were not allowed to carry other metal objects, such as a watch.”
The results are impressive. The new magnetic drums remove four times more metal from the material stream, tests have shown. “The block magnet confirms this. There are significantly fewer logs hanging from these.”
For more information see https://bakkermagnetics.com/.