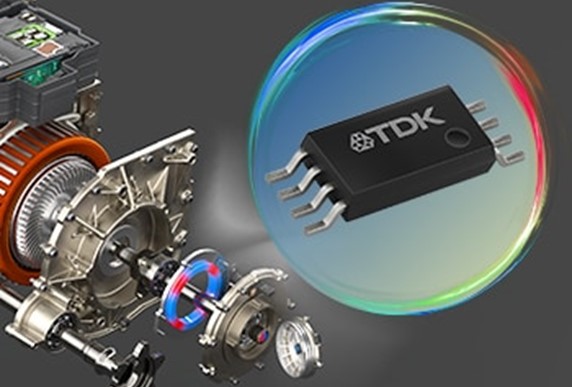
As environmental awareness grows and the realization of a sustainable society becomes increasingly important, the mobility market is witnessing an active movement towards adoption of electric vehicles, aiming to transition from gasoline-powered to electric-powered motor vehicles. To design higher performance EVs, including electric motorcycles, next-generation electric motor technology that balances factors such as high efficiency, high reliability, compactness, light weight, and cost performance at a high level is required.
Tunnel Magneto Resistance angle sensors are earning an important role in the transition, explains TDK, a leading developer of TMR sensors for automotive and other applications. A recent presentation by the company compares the different angle sensor technologies for detecting rotational angles in traction electric motors and explains why TMR angle sensors can enhance EV design. Some highlights are presented here.
Fundamentally, since an e-motor serves as a power unit it plays a crucial role in the proliferation of electric mobility and is required to balance efficiency and performance. Highly efficient e-motors reduce energy consumption and extend battery life. This enables long-distance travel on a single charge, improving user convenience. Low noise and vibration characteristics also provide a comfortable ride and minimize operating noise and vibration.
As rotary angle detectors, angle sensors assist e-motors in the accuracy and efficiency of vehicle control systems. Resolvers and inductive angle sensors are currently mainstream, but they have several challenges.
Firstly, the high cost is one of the significant problems of resolvers. The complexity of the design and the difficulty in manufacturing these sensors, along with high material costs, lead to an overall increase in expenses. Furthermore, the fee of encoder licenses used in conjunction with the sensors and the expenses included in the R/D converter are also an additional burden. Resolver and inductive sensors are not scaling in system cost well as they always need a full set of components.
The next issue is the size. Resolvers require a high-inertia metal target during rotation and take up space due to the use of coil systems. Inductive sensors consist of three or more coils on PCB and a metal plate attached to the shaft to cover them, limiting further miniaturization. The large number of components also poses a disadvantage from the perspective of failure rate.
Magnetic sensors are also used as alternative solutions, but they face challenges in magnetic noise resistance. They react to the strength and direction of magnetic fields, so external magnetic noise can interfere and make accurate detection difficult without shielding.
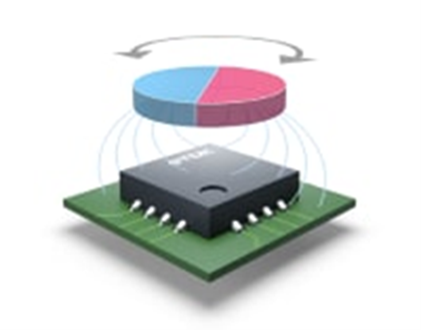
These challenges hinder the evolution of angle sensor technology and require a new approach, maintains TDK, leading to their case for greater adoption of TMR angle sensors. They are a type of magnetic sensor that detects the direction of a magnet’s magnetic field, allowing for high-precision detection of rotation angles and enabling efficient control.
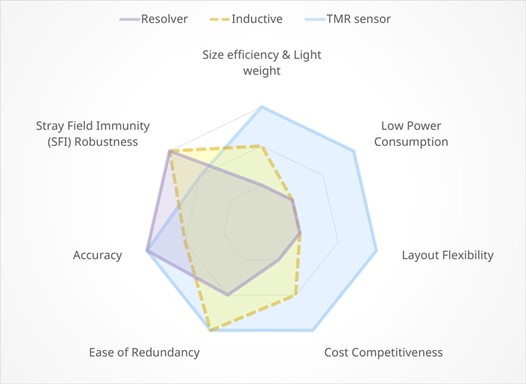
Size and weight can be an important benefit of a TMR angle sensor. It maintains an advantage of compactness and lightness even with a magnet besides the IC. Resolvers require excitation coils and output coils on the stator side and electromagnetic steel plates on the rotor side, which increase size and weight.
TDK’s compact packages contribute to the miniaturization, weight reduction and cost reduction of the entire system. They achieve the compactness such as TSSOP-8 (6.4 x 3.0mm) and QFN16 (3.0 x 3.0mm). The target magnets are also very small and lightweight, making them easy to integrate even in space-constrained environments, thereby increasing design flexibility and enabling efficient product development.
They also can offer a unique method of external magnetic field noise cancellation. TDK proposes a method to suppress external magnetic field noise signals using multiple sensors and consults with customers on magnetic shielding methods. The complete presentation plus more details, charts, action videos and graphs are available on the company’s website. See www.tdk.com.