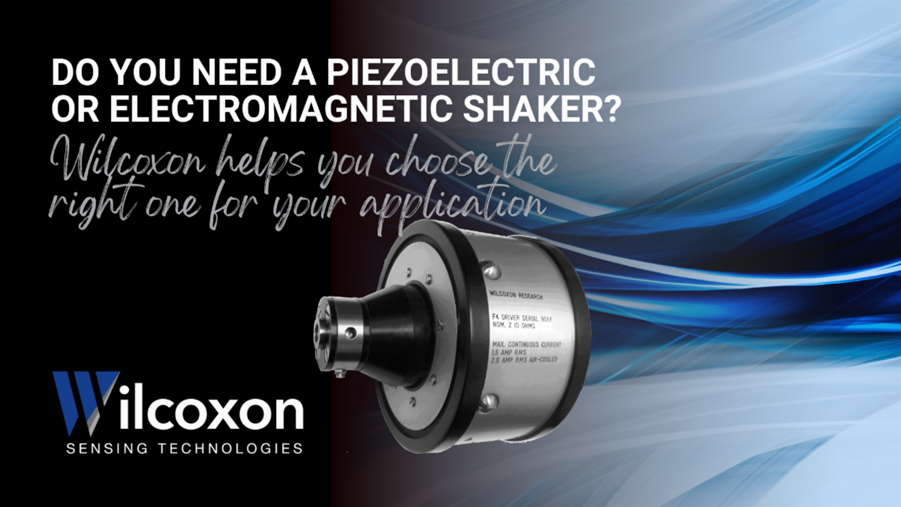
Which type of shaker works best for your test & measurement application – piezoelectric or electromagnetic? Try asking Peter Eitnier, senior application engineer for vibration monitoring specialist Wilcoxon Sensing Technologies.
We like his straightforward presentation of the fundamentals, coming from a specialist with a company that makes both types – and even designs both technologies into a combination product. Here are a few excerpts. Much more info is available on the company’s website, including specific application recommendations. Another area of magnetic expertise in the company is applied to its development of precision accelerometers.
Wilcoxon piezoelectric and electromagnetic shakers provide reliable structural excitation of a test article within a controlled, localized environment. By simulating such dynamic forces and natural frequencies, shakers can be used along with accelerometers and other vibration monitoring devices to reveal cracks, defects, weaknesses, or other abnormalities, allowing engineers and test technicians to better predict structural behavior over time.
Common uses are for structural testing, material studies, product testing, quality assurance, research and development, and modal testing. In his overview, Eitnier explains the two primary shaker types: electromagnetic/inertial and piezoelectric. Both can provide reliable structural excitation of test article within controlled, localized environment. They simulate dynamic forces and natural frequencies and are typically used along with accelerometers and other vibration monitoring devices to reveal cracks, defects, weaknesses, other abnormalities.
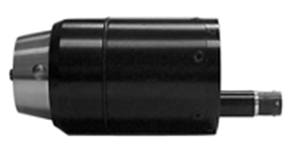
Basically, piezoelectric shakers which are based on sonic and ultrasonic structural excitation shine in high-frequency applications ranging from 500 to 80,000 Hz.
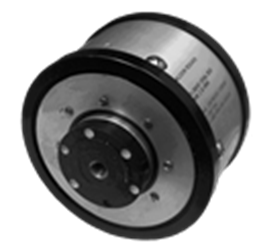
Electromatic shakers operate on the principal of magnetism and are applied mostly in low-frequency applications ranging from 5 to 10000 Hz. Magnetic field is formed as current runs through a wire. As wire is wound in a coil, effect is multiplied and can be manipulated. When magnets are fixed on either side of coiled wire, alternating electric currents flow into coil, inducing vibration and oscillation with the motion directed toward the object under test.
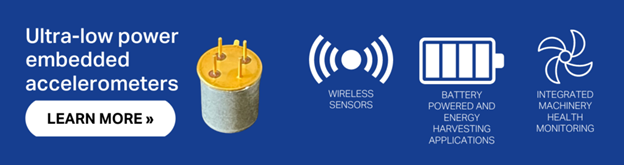
Last year, it introduced an ultra-low power accelerometer designed to be embedded into wireless vibration sensors and other battery-powered vibration measurement applications. The compact sensor, LVEP050-TO5, can also be embedded into motors, pumps, fans, and other production assets, to incorporate vibration monitoring built-in self-test capabilities into common wearable machine components.
For wireless sensing, battery-powered, and energy harvesting applications, the battery consumption is less than 5% of a standard industrial accelerometer and can take 4-10 times as many readings as other low-power piezoelectric accelerometers.
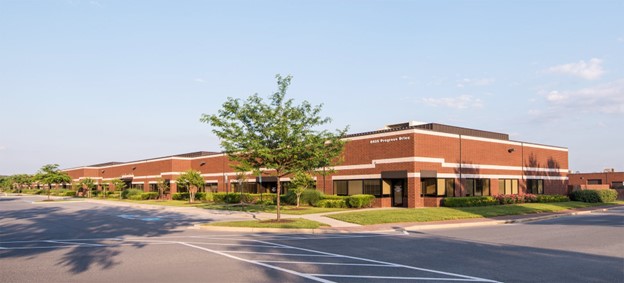
In Frederick, Maryland, Wilcoxon’s facility houses a wide variety of modern manufacturing, assembly and test equipment ranging from precision machinery for high-quality vibration sensor components to custom-built machinery specifically designed for accelerometer fabrication. See www.wilcoxon.com.