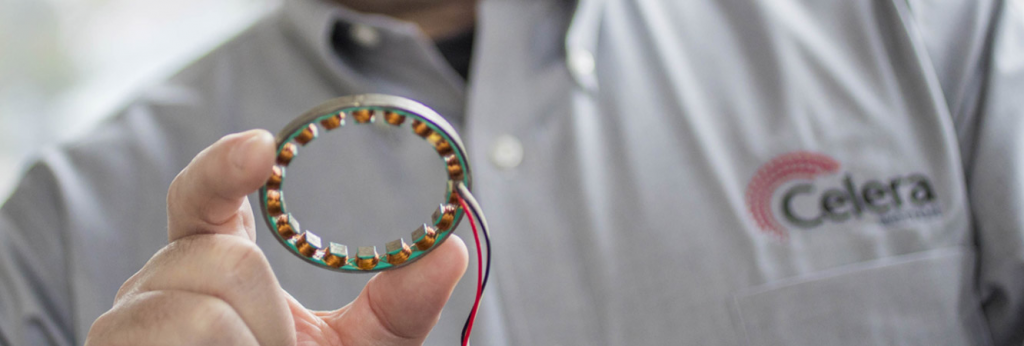
Slotted motors are good for high torque density and high acceleration, while slotless motors are optimum for smooth operation and good Kt (torque constant) linearity when operating in a servo control system. The reasons behind this are explained in an excellent white paper, “Slotless Vs Slotted Motors”, from Celera Motion that illustrates how their designs yield different attributes.
Permanent magnet brushless motors come in all shapes and sizes providing both rotary and linear motion. They are known for high torque density and high efficiency. They are also routinely referred to as Brushless DC motors, Brushless AC motors, Synchronous Permanent Magnet motors, or Servo Motors. The fundamental output of these machines is torque (rotary) or force (linear).
Smooth and predictable torque/force while moving is the main challenge for many applications in imaging, scanning, metrology, photonics, and tracking. Traditional permanent magnet brushless motors exhibit cogging torque, a torque disturbance from the interaction between the permanent magnet and the slots between stator teeth. Cogging is cyclical torque with angle that creates torque ripple, (and corresponding velocity ripple), adding a non-linear element to the control of the motor.
Various methods to minimize cogging have been used for years. They include skewing laminations, skewing magnets, special mechanical modifications, and electrical compensation in the motor controller. In most applications that require smooth motion with light loads the success of these methods is marginal.
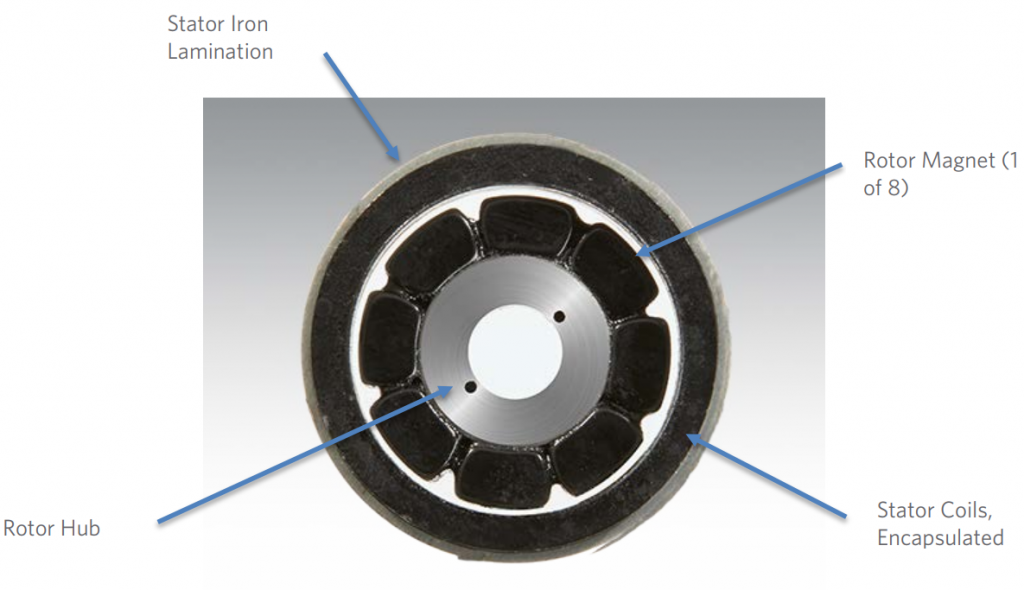
Slotless motors are designed to optimize smoothness and create predictable torque output with minimal non-linear effects. Commonly referred to as slotless motors when rotary and air core motors when linear, slotless motor designs place only copper phase coils in the air gap of the motor. These coils, when placed properly, interact with the permanent magnetic flux to create force or torque. Cogging torque is eliminated because the discontinuous iron teeth are removed from the motor air gap. Slotless technology is especially effective with direct drive precision systems because all torque is a function of phase current and there are no unwanted or uncontrolled torque disturbances from the motor. For more details, diagrams and illustration, see the White Paper.
Celera Motion, based in Bedford, MA, is a motion control business of Novanta. Celera makes encoders, motors, servo drives and mechatronic solutions.
For more info, see www.celeramotion.com.