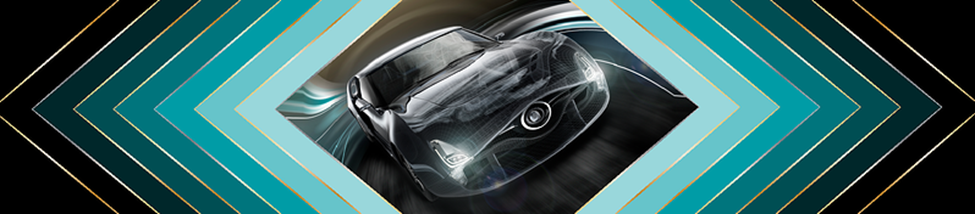
The demand for electric vehicles for both personal and commercial transportation continues to grow and with this growth comes increased pressure on designers of on-board chargers and DC/DC inverters to ensure the battery packs are efficiently utilized. This reality, in turn, puts renewed focus on the power magnetic components that are used to provide isolation and voltage conversion throughout the vehicle.
The need to ensure that high-power magnetics are optimized in terms of density, weight, efficiency and cost along with the increased usage of resonate mode switching topologies dictates the use of advanced 3D design techniques. “Optimized high power magnetic design is only possible through the effective use of finite element (FEA) modeling,” according to John Gallagher, product marketing for the power business unit of Pulse Electronics. “Pulse employs our expertise to ensure we can provide the most efficient designs for our automotive customers.”
Today, engineers are requesting magnetic parts in applications that use phase-shifted full bridge and LLC converters. In a new white paper, “Design of High Power Planar Magnetics for a 1.8KW Phase Shifted Full bridge Converter using Advanced FEA Electromagnetic’s Tools,” Pulse engineers David Mungia and Gerard Healy analyze the designs of two magnetics, a phase-shifted full bridge transformer and accompanying output inductor, to prove out the benefits of FEA for optimizing designs. Designed by using Ansys Maxwell electromagnetic field simulation software, the magnetics are used in a 1.8kW DC/DC inverter for HEV/EV automotive applications.
They use the 2D eddy current solver within the program for quickly comparing winding topologies in the power transformer, and AC losses in distributed gap configurations for the output inductor. “There is an important requirement in high-power converter applications for highly efficient yet small power magnetics. It is commonly believed that complicated and dense 3D finite element analysis models are required to accurately analyze and design high-power magnetics. In contrast, here we propose a novel design methodology using 2D FEA approximations, that produces results quickly and accurately,” explain the authors.
At high frequency, there will be skin and proximity losses in the transformer. Therefore, it is crucial to select an optimal interleaving strategy. While the true loss of the transformer is not calculated accurately at this stage, using the 2D solver does speed up the process of evaluating different design iterations without having to wait long periods of time for each set of results, they note. Even though the solver did not produce the true loss, it did help to identify the best configuration. Their technique demonstrates a way how designers can take full advantage of the capabilities of advanced electromagnetic FEA software to quickly model complicated planar magnetics and improve their performance.
For more info, see www.power.pulseelectronics.com.