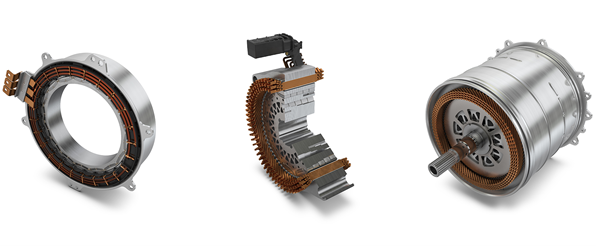
Securing large orders recently for motors and integrated powertrain systems for electric vehicles, automotive supplier Schaeffler is reaping the rewards of its decision to create a specific business division for electric mobility three years ago, at the beginning of 2018. The start of mass production for multiple products across all electrification levels is testimony to its successful engagement in the electric mobility area, the company says.
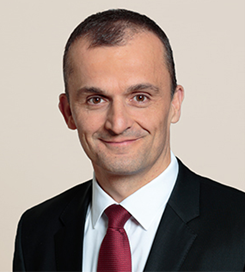
“We have successfully transformed ourselves into a drive system supplier for sustainable electric mobility solutions and established ourselves as a reliable partner for our customers,” says Matthias Zink, CEO Automotive Technologies at Schaeffler AG. “We have been engaged with electric mobility for more than 20 years and we understand the drive train requirements.”
Over the last few years, Schaeffler has progressively strengthened its electric mobility expertise through a series of targeted acquisitions. The purchase of Elmotec Statomat, a leading maker of machinery for manufacturing stators, at the end of 2018 added new expertise in winding technology and other aspects of electric motor manufacturing technology. Another highly successful acquisition back in 2016 was the takeover of Compact Dynamics, a specialist in the development of innovative electric drive concepts.
Mass production solutions across all levels of electrification
Now the company supplies technologies for all electrified drive trains. Mass production of the electric axle transmission, a key component of electric axle systems, has been running successfully since 2017, providing optimum transmission ratios and power transfer from the electric motor to the wheels. This is a highly versatile component with a wide range of applications. In the Audi e-tron, for example, Schaeffler electric axle transmissions, with different structural designs, are used on both axles for all-wheel drive capability. The Porsche Taycan is fitted with a high-efficiency Schaeffler coaxial electric axle transmission to provide the required transmission ratio on the front axle.
In 2020, the coaxial electric axle transmission earned Schaeffler the prestigious PACE Award, regarded as the hallmark for successful automotive projects. Schaeffler has also secured multiple orders for its complete “3in1 electric axles”, which combine the electric motor, drive unit and power electronics in a single system. They are high-performance electric axles with advanced power density.
Electric motors: Start of mass production
This year will see the start of the mass production of hybrid modules, hybrid drive units and all-electric axle transmissions. The basis of Schaeffler’s electric motor production is a modular, highly integrated technology platform. Schaeffler’s strong expertise in the areas of production and technology across all components of electric drive systems is the key to the successful industrialization of products that are both technologically advanced and highly profitable.
Along with a series of mass production orders for electric motors in the passenger car sector, Schaeffler recently entered the heavy-duty applications segment for commercial vehicles. The company recently announced a mass production order for electric motors featuring the “wave winding” technology, which provides high power density as well as advantages during assembly.
Record order for dedicated hybrid drives
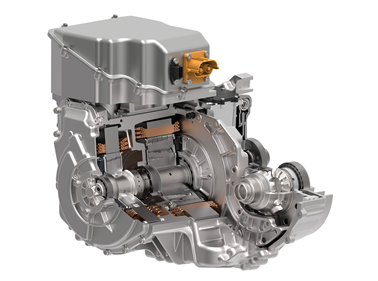
As reported last year, Schaeffler has received a record order for dedicated hybrid drives. From 2024, Schaeffler will deliver an entire drive unit comprising two electric motors and transmission with integrated power electronics. A system power rating of 120 kW offers sports-car like performance with low fuel consumption.
“We are making excellent progress,” says Dr. Jochen Schroeder, president of the E-Mobility business division. “Our modular product portfolio enables us to offer customized volume-production solutions to meet any customer requirement.”
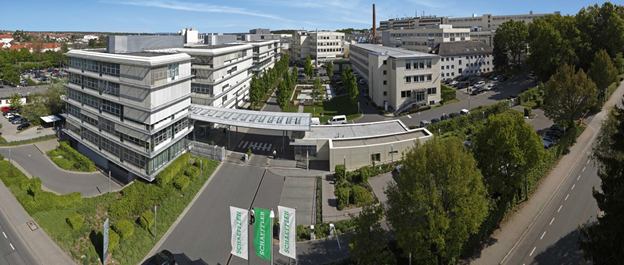
Based in Herzogenaurach near Nuremberg, Schaeffler manufactures components and systems for drive train and chassis applications for the automotive industry, as well as rolling and plain bearing solutions for industrial applications. With around 83,700 employees, the group is one of the world’s largest family companies, working from 170 locations in over 50 countries.