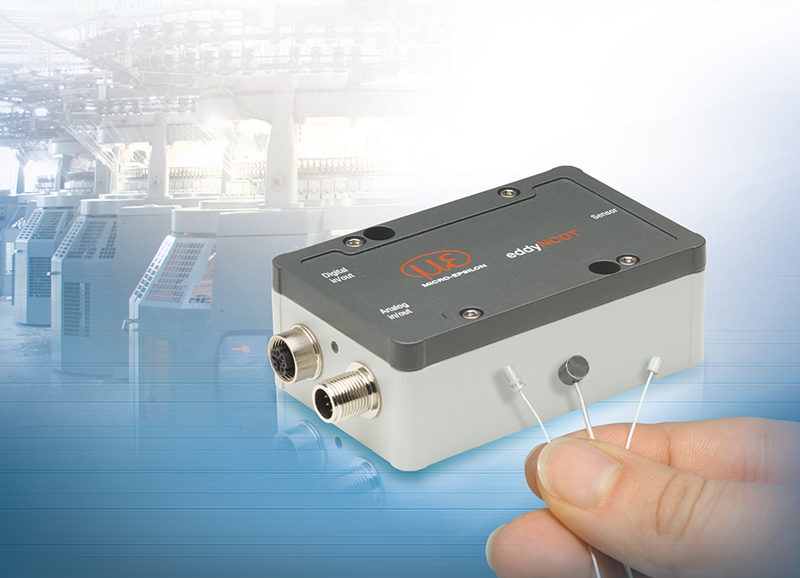
A new inductive eddy current displacement measuring system from Micro-Epsilon offers high performance and precision for applications in industrial processes. It provides resolutions in the submicron range and operates with a frequency response up to 20 kHz.
The eddyNCDT 3070 eddy is designed for small non-contact measuring ranges below 1 mm, precisely measuring displacement, distance, position, shaft movement and gaps. It is particularly suited for applications in harsh environments where highest precision is required such as those found in plant and machine building, automotive industry, automation technology and test benches. The system consists of a sensor, a cable and controller. At the factory, the sensors are matched to ferromagnetic or non-ferromagnetic objects.
Like other non-contact, inductive displacement sensors from Micro-Epsilon, it operates according to the eddy current measuring principle. Unlike conventional, inductive displacement sensors, they measure on ferromagnetic and non-ferromagnetic materials. Due to their immunity to oil, dirt, pressure and temperature, these inductive eddy current sensors are primarily used for integration in machines and facilities.
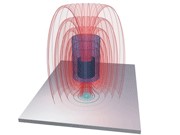
A coil is integrated in a sensor housing and energized by a high-frequency alternating current. The coil’s electromagnetic field induces eddy currents in the conductive measurement object, causing the resulting alternating current resistance of the coil to change. This change of impedance causes an electrical signal which is proportional to the distance of the object to the sensor coil. The high-frequency field lines emanating from the sensor coil easily penetrate non-metallic materials, which allows for measurements even at high levels of contamination, pressure and oil or plastic coverings.
For more info, visit: www.micro-epsilon.com.