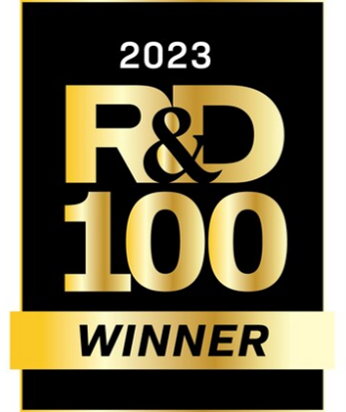
Bunting-DuBois in partnership with the CMI at Ames National Laboratory has successfully compression bonded a new magnet material. The “Cerium Gap Magnet” is made by utilizing the plentiful rare earth element Cerium (Ce). The project resulted in the team winning a 2023 R&D100 award which is often referred to as “The Oscars of Innovation” and the “Nobel Prize of Engineering”.
Traditional ferrite or “ceramic” magnets are made by combining iron oxide with either strontium or barium carbonate using extreme heat. An inefficient high energy consuming process that produces a somewhat weak magnet. On the other end of the scale for magnetic strength, neodymium magnets are made by melting neodymium, iron, and boron to a liquid, strip casting it into flakes, then crushing it to a powder. The powder is then pressed and sintered into a specific shape with heat. Ceramic magnets tend to be too weak to be of use in the clean energy sector and thus have a very low demand in those markets. Neodymium magnets on the other hand, are what has allowed the clean energy sector to evolve. This type of magnet has a limited raw material supply and carries a high price point that can fluctuate dramatically.
The “Gap” in Cerium Gap Magnets is a void that exists between the weaker ferrite or “ceramic” magnet and the significantly stronger “neodymium” magnets, said Don Lindstrom, General Manager of Bunting-DuBois. By creating a magnet that is stronger than ceramic and that does not rely on the neodymium iron boron elements, industry can have access to a less expensive alternative for products that need more than a ceramic magnet but don’t need the power of a neodymium magnet. As a result, demand for neodymium can be reduced.
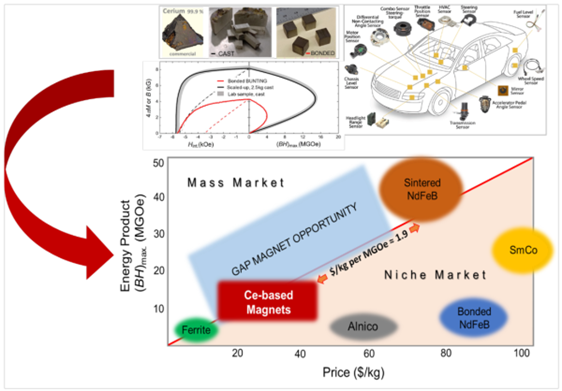
Cerium Gap Magnets use elements that combine at an intragranular level through a domain pinning mechanism which eliminates the need for sintering. It remains to be seen if the Cerium Gap Magnet will have the characteristics to replace neodymium, that’s up to the product manufacturers. It is possible one could use these in various sensors used in automobiles, which could make a real impact at reducing the demand on neodymium.
“Bunting-DuBois has been collaborating with CMI and Ames National Laboratory on both new innovative processes as well as critical material development for almost 10 years, said Lindstrom. Our partnership has led to several interesting developments in the field of magnetics.”
For additional information on the development of Cerium Gap Magnets please see the you tube video at: https://youtu.be/zsb61XSzylI?si=75RgmGUNhiO2y9Q2 For further information on Bunting-DuBois, visit: www.bunting-dubois.com.