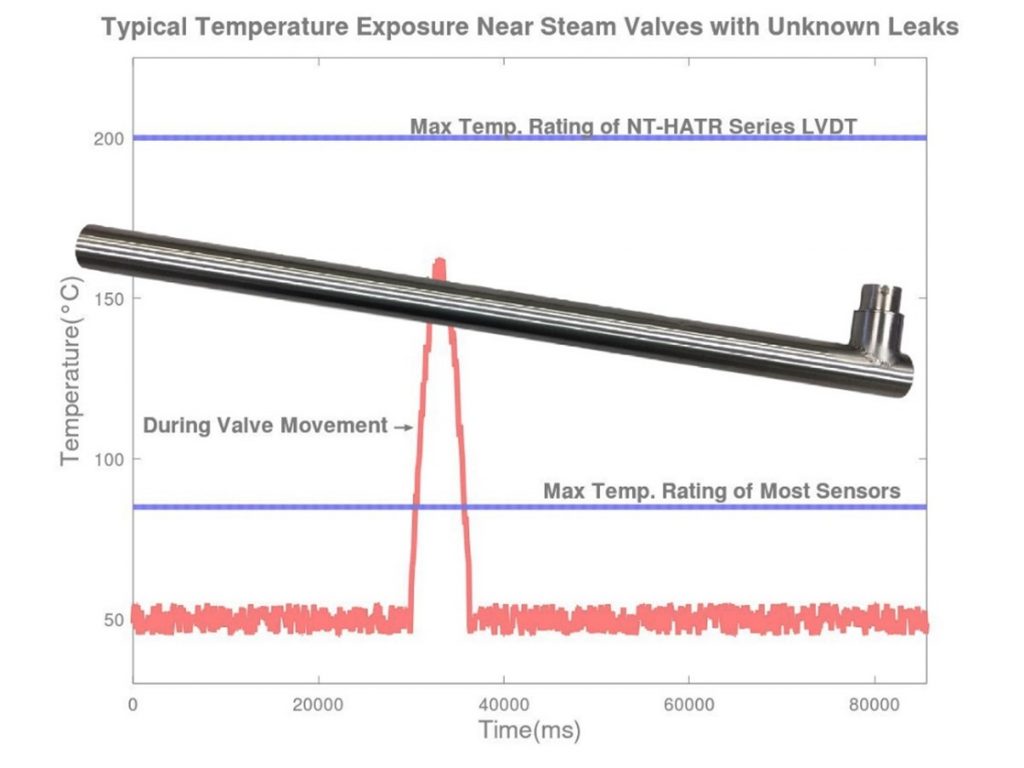
High-temperature position sensors from NewTek Sensor Solutions feature inductive linear technology that provides a reliable and long-term solution to sensors that fail when operating in rugged environments with unanticipated temperature spikes. Steam valves in power generation plants, for example, can have undetected leaks when moving, causing periodic rises in temperatures beyond original operating specifications and sensors not designed for temperature spikes can fail even when exposed to briefly elevated temperatures.
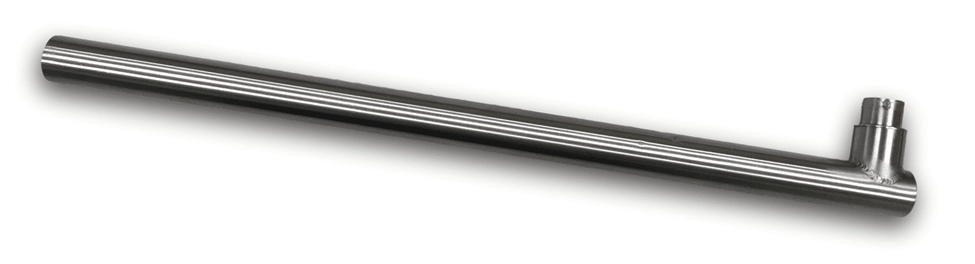
The company’s range of HATR-750 High Temperature LVDTs combat the problem, giving operators a reliable output of valve position. Hermetically sealed and constructed of stainless steel, the AC-operated LVDTs can operate in fluctuating temperatures from -65°F to 400°F. Windings are potted inside the housing with epoxy for added protection against harsh environments. They can be applied to a range of industrial applications such as machine components, workpiece or valve position sensing in factory automation, assembly and power generation plants with corrosive environments.
A linear variable differential transformer (LVDT) is a common type of position sensor that converts the linear position or motion of a measured object to a proportional electrical output that can be read by operators and control systems. Inductive transformers with frictionless operation, they have a near-infinite expected service life.
There are two basic components: a fixed housing containing the single primary winding with two secondary windings and a movable core constructed of ferromagnetic material and mechanically linked to the measured object. There is no physical contact between the housing and the core. The single primary coil is centered in the housing and energized with an AC signal. Magnetically coupled by the core, a voltage is induced in each of two symmetrical secondary windings connected in a series-opposing circuit. The effective voltage and LVDT output is the difference between each secondary. When the core moves away from the center of the LVDT, known as the null point, the signal from the primary will be coupled to one secondary more than the other.
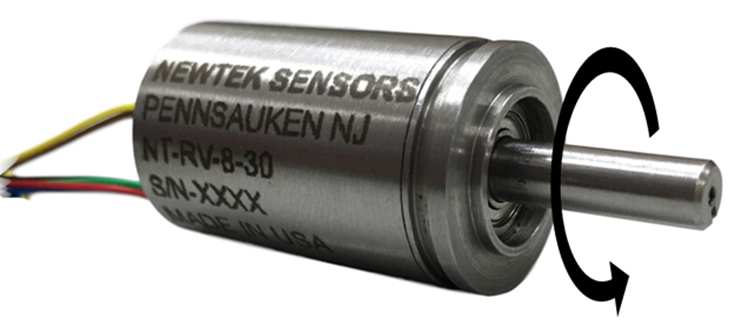
Based in Pennsauken, New Jersey, Newtek makes a diverse portfolio of sensors for performing at extremes of pressure and temperature and in harsh environments. Among these are its RV series of rotary position sensors, shown above. They measure and provide feedback on the rotary displacement of rotating elements in industrial benchtop and test and measurement applications. Used to measure the angle of an incomplete turn, they are used in mail sorters and diverter gates of packaging and postal sorting equipment as well as for actuator feedback, throttle position and quarter-turn valve position sensing. For more info, see www.newteksensors.com.