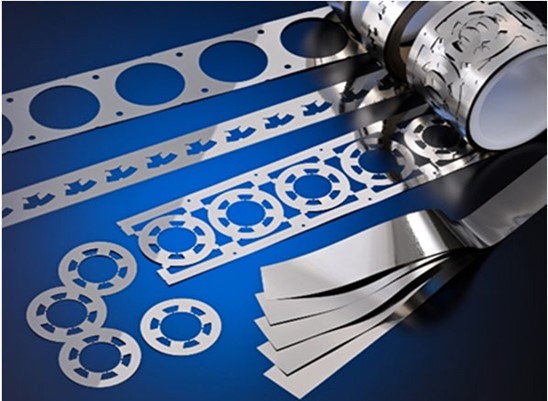
Proterial, formerly known as Hitachi Metals, has recently developed two magnetic materials that bring new capabilities to product design engineers – one is a laminated bonded amorphous alloy ribbon for motor cores in high-efficiency motors, the other a highly heat-resistant magnetic shielding sheet for electronic devices.
Amorphous alloys are a low-loss material and considered to be suitable for high-efficiency motors such as those used for propulsion in electric vehicles, however, because of their greater hardness and thinner material compared to electromagnetic steel sheets, their application in the mass production of motor cores has been limited to those for axial-gap motors. The newly developed ribbon has a thickness close to that of electromagnetic steel sheets, enabling its application to radial-gap motors commonly used in EV drive motors.
In recent years, amorphous alloys have been attracting attention as a low iron loss material that exceeds the limitations of some electromagnetic steel sheets. However, amorphous alloys are about five times harder than electromagnetic steel sheets, resulting in a shorter service life of the punch die. Additionally, the material is only about 1/10th the thickness of electromagnetic steel sheets, resulting in lower productivity in the punching process. Due to these issues, their application in mass produced motors has been limited to axial-gap motors that avoid the use of punching processes.
However, Proterial, a leading manufacturer of amorphous alloys for transformer cores, has been engaged in ongoing research and development and been able to build upon its accumulated knowledge of the alloys, to accomplish extending the application of cores made of them to radial-gap motors.
Now, Proterial engineers and scientists have developed a technology for continuously laminating and bonding multiple sheets of amorphous alloy ribbons for radial-gap motor cores. Key factors are selection of the adhesive and control of adhesive layer thickness. With the development of proprietary technology that enables formation of layers of adhesive thinly and uniformly, they have been able to achieve a high space factor of 90% or more and laminate the material, with no degradation in the excellent magnetic properties of amorphous alloys.
The laminated and bonded material has a thickness comparable to that of electromagnetic steel sheets, which improves material handling and significantly reduces the number of processing man-hours required. Another feature is that with this increased thickness, the machining accuracy of the punch die can be relaxed.
Proterial says its engineers will continue to provide solutions to the thinness issue through lamination and at the same time provide solutions to the punching issue through the optimization of die materials and coatings tailored to amorphous alloys to help further expand the range of motors that can use them. Meanwhile, the company has begun offering samples of the new ribbon to motor manufacturers and core fabricators.
Highly heat-resistant magnetic shielding sheet
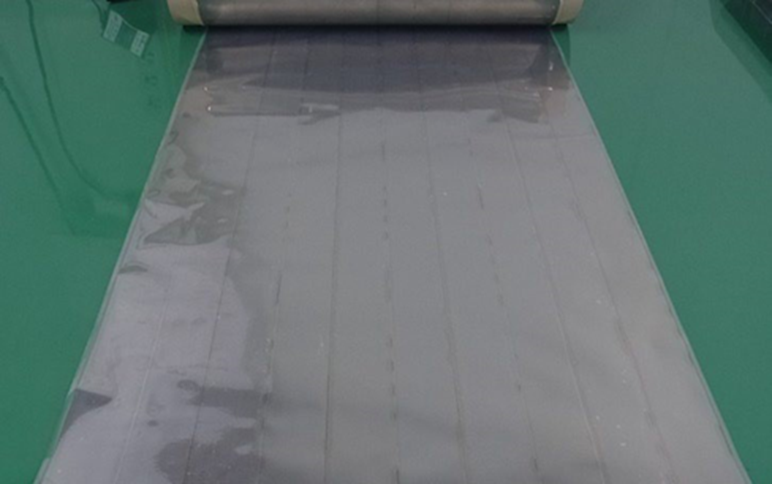
The new magnetic shielding sheet, MS-FH, contributes to the miniaturization and weight reduction of electronic devices used in high-temperature environments, says Proterial, with improved heat resistance over its MS-F magnetic shielding sheet made of nanocrystalline soft magnetic material Finemet. The new sheet exhibits improved heat resistance up to 130°C, 50°C higher than the previous product, and is only about 40% of the thickness. Mass production is scheduled to start in December 2024
The original MS-F magnetic shielding made of Finemet provides excellent magnetic properties including high magnetic permeability and saturated magnetic flux density as well as being thin, lightweight, flexible in its handling, and providing good processability for easy cutting and punching. It has been used for noise suppression in a wide range of applications such as in electronic devices including mobile phones, PCs, cameras, in medical equipment such as X-ray diagnostic equipment, as well as shielded rooms designed to reduce geomagnetism and other external magnetic fields.
In recent years, however, the product has increasingly been used in electromagnetic noise suppression applications for in-vehicle electronic equipment on new-generation electric vehicles. However, sheets with heat resistance greater than MS-F were needed as its usable temperature was 80°C or lower, which meant that high temperature conditions on vehicles would cause its protective film and adhesive to deteriorate while also affect its magnetic properties.
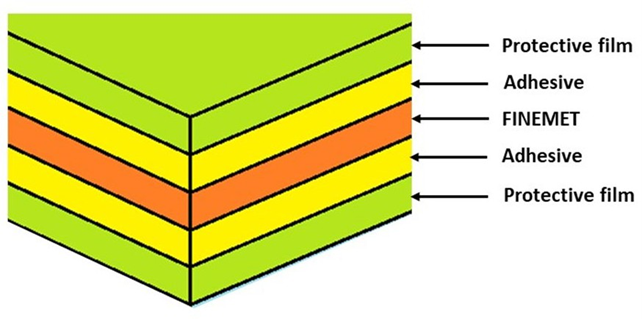
Now, through further research into MS-F’s protective film, adhesive material, and manufacturing conditions, Proterial has successfully developed the new sheet which has a structure where Finemet and protective films are integrated by means of laminate molding. The new film remains stable at high temperatures without deterioration of Finemet’s magnetic properties.
Also, manufacturing processes that may potentially affect the properties of Finemet—especially conditions in lamination processes where thermal expansion and contraction occur due to heating—were revised, helping achieve the improved heat resistance. For more info, see www.proterial.com.