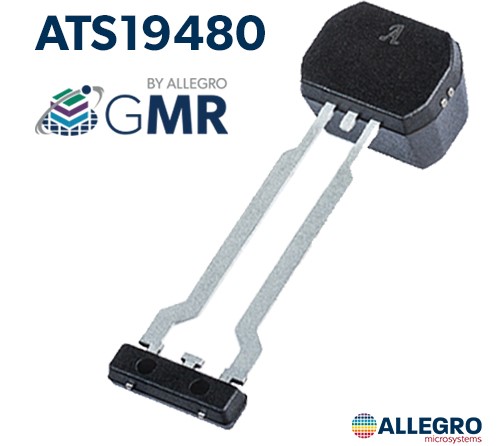
Allegro MicroSystems has introduced two new giant magnetoresistance sensors designed to control crankshafts and camshafts in hybrid electric vehicles. They feature a large air gap for simplified design-in, and an assembly that optimizes the IC-to-magnet positioning for enhanced accuracy.
Welcome to the Annual Magnetic Sensing Fest at Magnetics Magazine
Stay tuned for more!
“They’re unique to the market and outperform competing technologies due to their high air gaps and level of accuracy,” says Peter Wells, speed and sensor Interface business line director. “The industry is transitioning to xEVs quickly, and the ATS16951 (crankshaft) and ATS16351 (camshaft) both offer a level of precision that will help give automakers the increases in motor efficiency they’re targeting.”
With an air gap that’s 50% larger than existing options, the camshaft sensor improves both design-in flexibility and stray field immunity, says Allego. It can be placed virtually anywhere, which is increasingly important as some hybrid engines now include four camshaft sensors. Tight spaces often combine with high current transients, so engine designers need camshaft sensors that work seamlessly through the resulting stray fields.
A three-pin single inline package houses the IC, magnet and EMC protection components, enhancing flexible design-in and system compensation. The precision assembly optimizes IC-to-magnet positioning, as reduced tolerance stack between the IC and magnet increases sensor accuracy and leaves ample margin for in-application installation tolerance.
While the trend toward full electrification continues to accelerate, notes Allegro, recent IHS forecasts predict that 81% of vehicles will include some form of internal combustion engine through 2029, with full and mild hybrids being the most common. Engine architectures are changing as part of the shift toward smaller hybrid designs, and sensor accuracy and positioning flexibility are becoming more important than ever before.
Giant magnetoresistance (GMR) is a newer technology that, over the full range of airgap, can create a signal 50 times higher than Hall-effect solutions. The extensive signal amplitude results in an excellent signal-to-noise ratio and the GMR’s higher sensitivity provides higher accuracy and larger air gap/lower magnetic field operation that many applications can benefit from.
“Our GMR design produces more than 50 times the voltage of a Hall element when a magnetic field is applied, which translates to a monumental boost in signal-to-noise ratio. This allows the IC to sense at significantly larger air gaps and output a periodic signal with extremely low jitter,” says Allegro.
It uses a spin-valve architecture which involves a reference layer with a fixed magnetic orientation and a free layer that aligns with the applied external magnetic field, enabling a relatively low resistance. When the field applied is perpendicular to the reference layer, the element’s resistance becomes higher. This change in resistance transduces the applied magnetic field into the electrical domain for the IC. At a physical level, the element’s magnetic orientation affects the spin state of the electrons, which affects the rate of electron scattering and consequently changes the element’s resistance. For more info, see www.allegromicro.com.