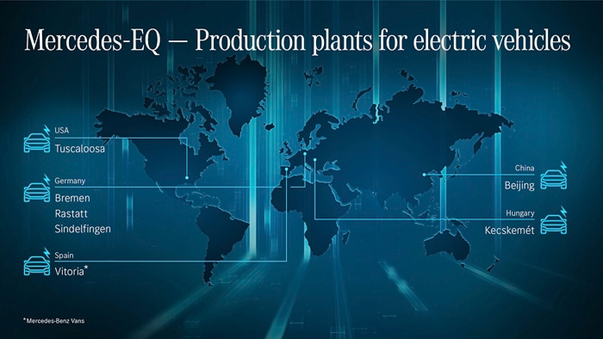
Emphasizing a dedication to in-house development and manufacturing of e-drive systems and axial-flux permanent-magnet motors, Mercedes-Benz is preparing its car production network for its new electric portfolio. Expansions in battery production and supply are also key elements. Highlights of the far-reaching plans, announced June 29 in Stuttgart, include:
- Mercedes-Benz foresees a highly flexible production network for “electric only”: Management and employee representatives reach consensus on future European production setup.
- Top End Luxury: Sindelfingen, the lead Mercedes-Benz plant for high end vehicles to produce models based on the AMG.EA platform (AMG Electric Architecture) from 2025.
- Core Luxury: The Mercedes-Benz plants in Bremen, Germany and Kecskemét, Hungary to manufacture vehicles in Europe based on the MB.EA platform (Mercedes-Benz Electric Architecture).
- Entry Luxury: The Mercedes-Benz plants in Rastatt and Kecskemét to produce the repositioned models of the MMA platform (Mercedes Modular Architecture) from 2024 in Europe.
- Highly efficient battery systems to be supplied by the global Mercedes-Benz battery production network.
Mercedes-Benz is aligning its global production network to manufacture its reshaped product portfolio focused on luxury electric vehicles as the world’s most valuable luxury car brand prepares to go all electric by the end of the decade – wherever market conditions allow. The future product portfolio will focus on three categories: Top End Luxury, Core Luxury and Entry Luxury as outlined in the company’s Economics of Desire event in May.
Jörg Burzer, Member of the Board of Management of Mercedes-Benz Group AG, Production and Supply Chain: “Following the successful launches of Mercedes-EQ models in recent months, we are taking the next step: To outline the plan for our future production setup. Together with the employee representatives, we are consistently implementing the Mercedes-Benz strategy towards ‘electric only’. The global Mercedes Benz production network is sustainable, digital and flexible. We are ready for the rapid scaling of electric vehicle volumes – not least thanks to our highly qualified and motivated team worldwide. With the new production setup we are further increasing our flexibility and efficiency and securing the future of our locations.”
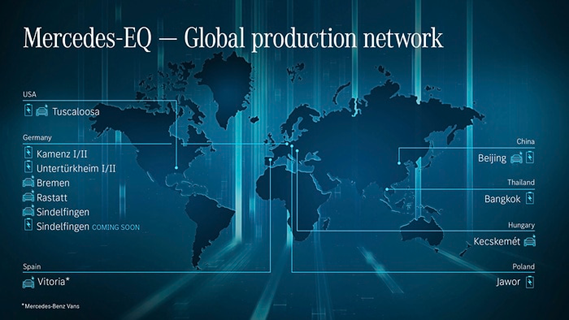
The Mercedes-Benz plants in Sindelfingen, Bremen, Rastatt and Kecskemét will start production of new models in the Top End Luxury, Core Luxury and Entry Luxury segments from the middle of the decade.
The Mercedes-Benz Sindelfingen site is the lead plant for the Top End Luxury segment and will produce models based on the electric AMG.EA platform from 2025. The Mercedes-Benz plants in Bremen, Germany and Kecskemét, Hungary to manufacture vehicles in Europe based on the electric MB.EA platform. Rastatt and Kecskemét will also produce the repositioned models based on the MMA platform from 2024 onwards. As part of implementing the Mercedes-Benz 2022-2026 Business Plan, the company is investing more than two billion euros into its European production sites. This step marks a new phase of introducing next-generation electric platforms in production, securing future employment at European locations. The new production plan is the outcome of constructive discussions with German employee representatives, resulting in far-reaching measures to further increase flexibility and efficiency.
Ergun Lümali, Dep. Chairman of the Supervisory Board and Chairman of the Works Council of Mercedes-Benz Group AG: “It is our job to ensure that the shift towards ‘electric only’ is fair. With today’s decision on the production setup, we are ensuring that this remains the case. It’s good news for the company, the locations and most of all, for our employees. As employee representatives we demanded German production sites continue to play a significant role. The introduction of new technologies to our production sites is the key to becoming future proof and to ensuring continued employment. With investments into the new production setup, we have ensured that vehicles with new electric architectures are built at our locations, helping to secure production capacity. This gives our colleagues, who have for decades worked for the three-pointed star, security and a new opportunity. We demand that the same should happen for our Powertrain-locations. The works council will continue to work towards this goal.”
Sabine Kohleisen, Member of the Board of Management of Mercedes-Benz Group AG, Human Resources and Labor Director: “The shift toward an electric and digital future is a big challenge and at the same time an opportunity. What is clear is that our production portfolio is undergoing a transformation, and with it our tasks and employment profiles. Today we have once again shown that we, together with the works council, have reached viable and forward-looking solutions for our production sites, our company and its employees. I am delighted that we are able to offer our colleagues new opportunities in future.”
The production portfolio already includes six all-electric Mercedes-EQ models. These roll off the production line at six locations on three continents and have been consistently integrated into ongoing series production. Thanks to early investments into flexible production and the use of the state-of-the-art MO360 digital production system, Mercedes-Benz is already able to produce battery-electric vehicles in large volumes. The batteries for the Mercedes-EQ electric vehicles are supplied by the global battery production network with factories on three continents. Local battery production is a key success factor for Mercedes-Benz’s electric offensive. Mercedes-Benz has been producing CO2-neutral in all of its own plants worldwide since this year and has also been purchasing electricity in Germany that comes exclusively from renewable sources (CO2-free) since this year.
Mercedes-Benz vehicle plants consistently implement electric production
Thanks to highly flexible structures, the plants of Mercedes-Benz AG can produce vehicles with different drivetrains on a single production line. With the strategic goal of shifting to all electric, the high degree of flexibility is a decisive advantage. It makes it possible to adjust production at short notice according to market demand.

Production of the all-electric EQS luxury sedan started last year at Factory 56 at the Mercedes-Benz plant in Sindelfingen. In Factory 56, the S-Class, the Mercedes-Maybach S-Class and the EQS are produced completely flexibly on the same line. The Factory 56 embodies the future of production at Mercedes-Benz and sets new standards in automotive engineering. The Sindelfingen plant is also responsible for the production of the Mercedes-Benz E-Class with Sedan, Estate and All-Terrain off-road variants, CLS as well as the Mercedes-AMG GT family and will soon be adding the GLC to its portfolio. Sindelfingen is the lead plant in the Top End Luxury segment and will produce models based on the AMG.EA platform from 2025.
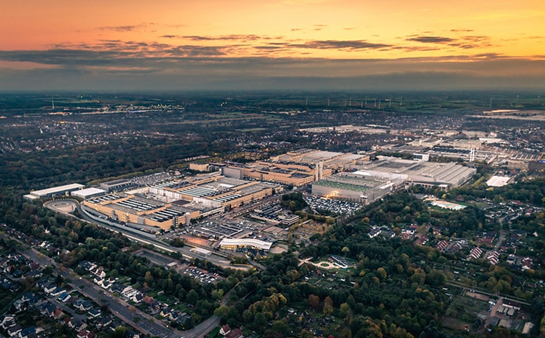
The Mercedes-Benz plant in Bremen started production of the all-electric EQE a few months ago. Already in May 2019, the EQC (combined power consumption: 21.5 kWh/100 km; CO₂ emissions combined: 0 g/km)[1] was integrated into ongoing series production at the Mercedes-Benz plant in northern Germany. In addition to the two all-electric models, the C-Class with Sedan, Estate, Coupe and Cabriolet, the E-Class with Coupe and Cabriolet, the GLC as well as the GLC Coupe and the AMG SL roll off the production line in Bremen. From the middle of the decade, a model based on the MB.EA platform will be integrated into production.
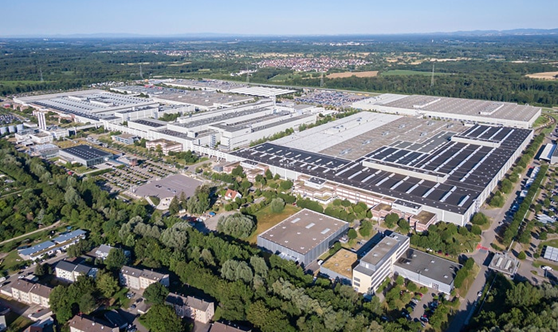
The Mercedes-Benz Rastatt plant has been producing the all-electric EQA compact model since 2021. The plant is also responsible for the production of the compact vehicles A-Class, B-Class and GLA with combustion engine and plug-in hybrid. From 2024, new models based on the MMA platform are to roll off the production line at the plant. In the Entry Luxury segment, Mercedes-Benz will reduce the number of model variants from seven to four while significantly elevating the technological substance of these products. These changes help to reposition Mercedes-Benz in this segment to meet the wishes of discerning customers.
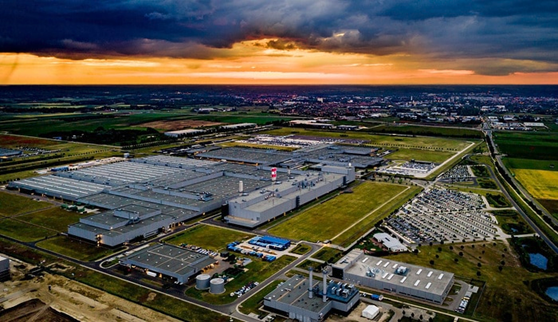
The EQB compact SUV was launched at the Mercedes-Benz Kecskemét plant in 2021 and is the first purely electrically powered series production vehicle from Hungary. The model complements the portfolio consisting of CLA Coupe and CLA Shooting Brake as well as the A-Class with its conventional, plug-in hybrid and AMG versions. From 2024, new models based on the MMA platform as well as a model based on the MB.EA platform in Kecskemét roll off the production line.
Beijing
Beijing Benz Automotive Co. Ltd. (BBAC) has been producing Mercedes-Benz vehicles locally for the Chinese market since 2005. A few weeks ago, production of the all-electric EQE business sedan started at the Shunyi plant. The Mercedes-EQ production portfolio of the joint venture consists of four models: Production of the EQC started in 2019. Since 2021, the EQA and EQB have been produced locally. The C-Class (long version), E-Class (long version), A-Class (long version), GLA, GLB, GLC (long version) and the AMG A 35 L are also produced locally within the joint venture.
Tuscaloosa
The Mercedes-Benz plant in Tuscaloosa, USA, will soon start production of the EQS SUV, with the EQE SUV to follow later this year. Both models are produced on the same line together with the SUVs with conventional drive. The GLE, GLE Coupe, GLS and Mercedes-Maybach GLS roll off the assembly line in Tuscaloosa today.
Global battery production network: key success factor for the Mercedes-EQ electric ramp-up
The batteries for the Mercedes-EQ electric vehicles are supplied by a global battery production network comprising factories on three continents. The local production of battery systems is a key success factor for the Mercedes-Benz electric ramp-up and a decisive component in being able to meet the global demand for electric vehicles flexibly and efficiently.
Accumotive has been producing battery systems for hybrids and electric vehicles in Kamenz, Germany, since 2012. A second battery factory at the site commenced operations in 2018 and has been producing the battery systems for the EQC since 2019 followed by the batteries for the compact electric SUVs since 2021. Since Accumotive began production, more than one million batteries based on lithium-ion technology have been produced at the Kamenz site.
Beijing Benz Automotive Co. Ltd. (BBAC) has established a local battery production facility at the existing site in the Yizhuang Industrial Park in Beijing, China. It supplies the vehicle plants, which produce for the local market. Production of battery systems for the EQC started there in 2019. Production of battery systems for the EQE started this year.
Also in 2019, Mercedes-Benz opened a battery production plant in Bangkok, Thailand, together with its local partner Thonburi Automotive Assembly Plant (TAAP). Battery systems for plug-in hybrids and all-electric vehicles are manufactured there.
The Mercedes-Benz battery factory in Jawor, Poland, has been producing plug-in hybrid batteries for the C-, E- and S-Class since 2020. In 2021, the site expanded its portfolio to include battery systems for the compact Mercedes EQA and EQB models.
Two factories as parts of the Untertürkheim site in Stuttgart, Germany, produce battery systems. The Hedelfingen plant has been producing batteries for the EQS and EQE since 2021. A few weeks ago, the production of plug-in hybrid batteries started in the Brühl plant, which will be used in the new GLC, among other things.
The new battery factory in Bibb County near the Mercedes-Benz vehicle plant in Tuscaloosa, Alabama started operations this year, producing highly efficient battery systems for the all-electric EQS SUV and EQE SUV later this year. The Mercedes-Benz battery production network will also be supplemented by another battery factory at the Sindelfingen site.
Electric drive systems in the global production network
Mercedes-Benz will deepen the level of vertical integration in manufacturing and development, and insource electric drive technology. The next generation of electric drive systems are being developed in house. The manufacturing and assembly of parts of the electric drive systems for future models of the Mercedes-EQ brand will start at the end of 2024 at the Untertürkheim plant.
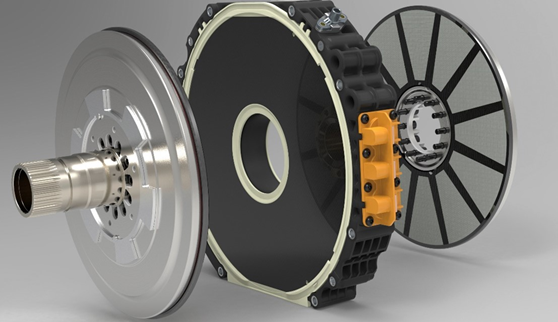
Another important step is the acquisition of UK based electric motor company YASA. With this deal, Mercedes-Benz gains access to unique axial flux motor technology and expertise to develop next generation ultra-high-performance motors. The Mercedes-Benz Berlin plant will expand its production portfolio with the manufacture and assembly of these ultra-high-performance axial flow electric motors in the future.
Sustainability in production
Compared to 2020, Mercedes-Benz is pursuing the goal of at least halving CO₂ emissions per passenger car over the entire life cycle by the end of this decade. The most important levers for this are the electrification of the vehicle fleet, charging with green electricity, the improvement of battery technology and the comprehensive use of recycled materials including batteries and renewable energies in production.
Mercedes-Benz has been producing CO2-neutral in all of its own plants worldwide since this year and has also been purchasing electricity in Germany that comes exclusively from renewable sources (CO2-free) since this year. A green electricity supply contract ensures the purchase of electricity from renewable energies at all times. In addition, the company aims to increase the production of renewable energy at its sites. Solar plants with a capacity of more than 11 MWp are to go into operation by the end of next year. By 2025, Mercedes-Benz will invest a three-digit million sum in the installation of photovoltaic systems. Mercedes-Benz is also planning to invest in new power purchase agreements for wind turbines worth 1 billion euros by the middle of the decade.
By 2030, it is planned to cover more than 70 percent of the energy demand in production from renewable energy sources – 15 percent is to be generated by renewable energy at the company’s own locations. This is to be achieved by expanding solar and wind energy at its own locations and by concluding further corresponding power purchase agreements. Mercedes-Benz is also pursuing the goal of reducing water consumption by 35% by 2030. Next, Mercedes-Benz also wants to make logistics CO2-neutral in which the rail transport of vehicles and components such as batteries play an important role. For more info, see www.mercedes-benz.com.