
Bmax, a provider of magnetic pulse systems and services for metal processing, showcased its technology at this year’s Consumer Electronics Show, CES 2024, demonstrating to product developers how it can help them realize products they might never have thought were possible. The systems are based on the high concentration of electrical energy used to manipulate metal at extremely high deformation speeds.
Special Report: Magnetic Technology Innovation at CES 2024
Its systems are currently being used for mass production of parts in automotive, aerospace, packaging and other industries. Welding aluminum to steel in drive shafts and forming deep and sharp details in packaging are just two commercial examples of how the technology has helped product managers and designers realize their product innovations.
Headquartered in Toulouse, France and with USA headquarters in Orion, Michigan, produces equipment and accessories such as specialty coils for industrial-grade magnetic pulse processing. The technology is developed and backed up by a team of over 70 engineers with decades of combined practical expertise and research.
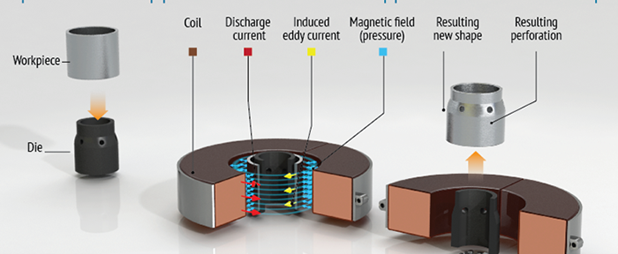
Basically, magnetic pulse forming gives product designers the power to create complex and detailed shapes more efficiently and with less steps and equipment. A special coil is placed near the metallic workpiece, replacing the pusher in traditional forming. When the system releases its intense magnetic pulse, the coil generates a magnetic field which in turn accelerates the workpiece to hyper speed and onto the die. The magnetic pulse and the extreme deformation speed transforms the metal into a visco-plastic state which increases formability without affecting the native strength of the material.

Magnetic pulse welding uses electromagnetically generated forces to create a solid-state cold weld at room temperature. The weld is completed in microseconds and is stronger than the base metals joined. No heat, filler materials or gases are required.
The conductive workpiece is placed inside or next to a Bmax coil which accelerates it over 1mm to impact the second workpiece at extremely high speed. The acceleration is a result of repelling magnetic fields between the workpiece and the coil, produced by the eddy current in the workpiece. Solid-state cold weld is created when two metals are forced together in such intensity their atoms start sharing electrons, practically fusing the two metals together. Since there is no heat or melting involved, dissimilar metals can be welded using this technique. It triggers the phenomenon by accelerating the metal into visco-plastic phase and impacts the other workpiece at an exact speed and angle.
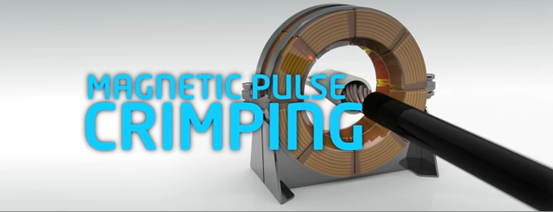
Magnetic pulse crimping is a contact-less process using Lorentz forces to crimp a wide variety of materials of different shapes and sizes. An alternative to mechanical processes, it uses the same principles as magnetic pulse forming and welding, able to shrink elements enabling new designs with extreme mechanical properties.
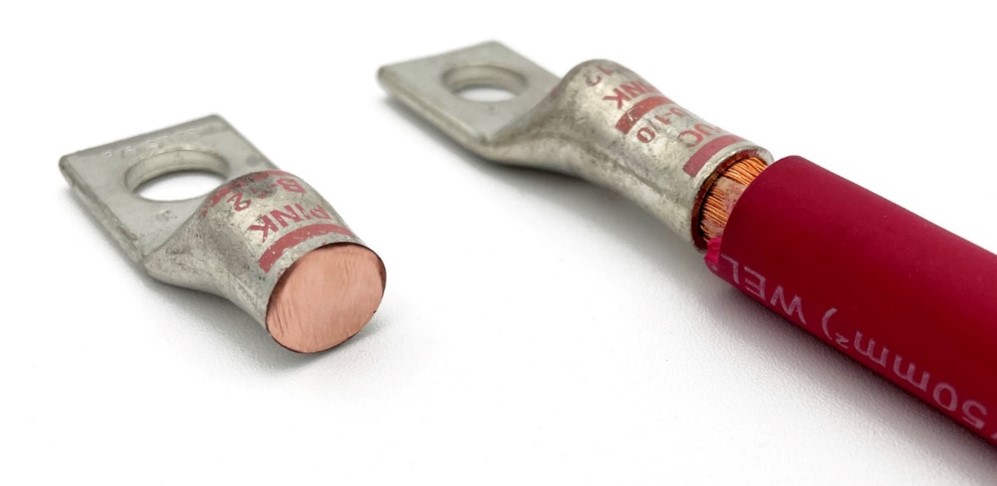
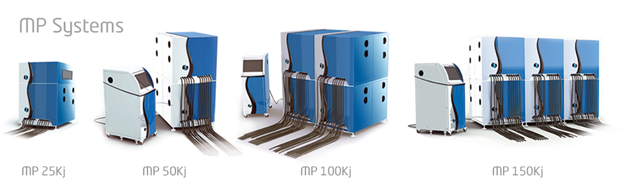
All Bmax systems are constructed of special capacitors able to store a large amount of energy in a relatively small space – and discharge it in milliseconds or microseconds. The heart of the system is a basic unit, holding a few capacitors and a specially developed switching device to hande the intense current flow. The system includes a pulse generator, connected to a control unit and a workstation where the workpiece is made, either manually or automatically. There is a wide range of auxiliary equipment such as special high-power transformers, coils and feeding systems.
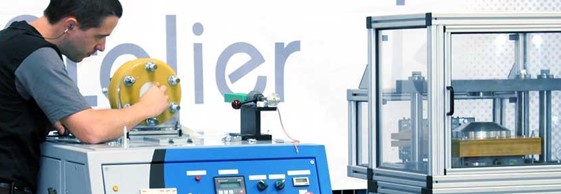
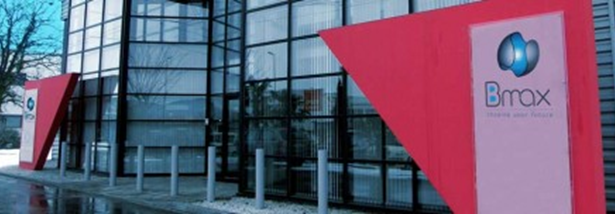