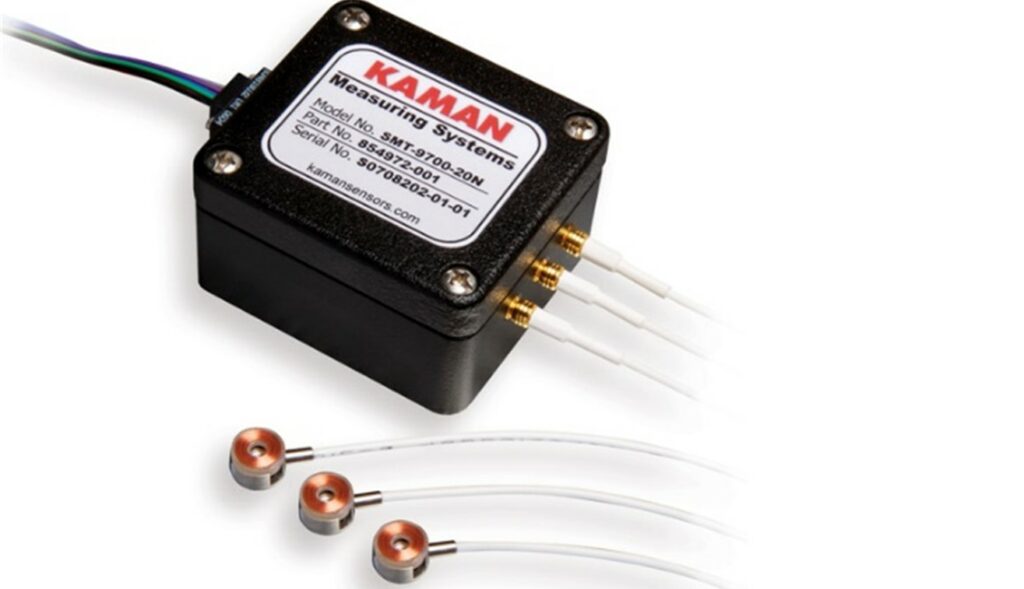
Kaman Corporation, maker of a broad range of rugged-duty, high-precision inductive, eddy current sensors, and also EMI shielding products, is taking the corporate route from a publicly held company to becoming privately held. The move began in January when Arcline Investment Management agreed to acquire Kaman for $1.8 billion, essentially buying out the shareholders. Upon completion of the transaction, expected in the first half of this year, plans are to convert the company to a privately held enterprise that will continue to be led by current management.
Likely, the deal will lead to more aggressive product development and future acquisitions as the company rationalizes its portfolio to focus on high-growth markets. “Over the last several quarters, we have made significant progress executing our strategy by transforming our portfolio, through investing in innovation, pivoting to new growth technologies, and optimizing the company’s cost structure,” commented Ian Walsh CEO of Kaman.
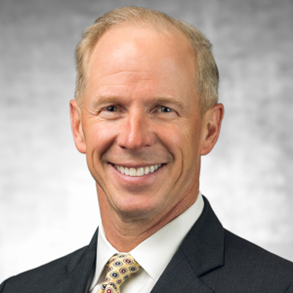
Founded in 1945 by aviation pioneer Charles Kaman, and headquartered in Bloomfield, Connecticut, Kaman produces a broad array of components for aircraft, also for arming military missile and bomb systems through its 11 business units. Its sensor lineup includes thousands of displacement sensors for extreme environments with different measurement ranges, materials, environments, temperatures and pressures. They range from handmade custom precision sensors to sensors manufactured in a fully automated environment. Sensors made by the company can operate in temperatures from cryogenic to 1,100° F.
Many of them are based on its core technology of inductive, eddy current sensing. Its sensors provide non-contact indication of linear position and displacement by outputting an analog voltage, or, in some cases, a current that is proportional to the distance between the sensor face and the target being sensed.
While some are general purpose, others are designed particularly for certain applications. Its SMT-9700, for example, shown at top, enables flexible, high-resolution position and displacement systems for analytical and OEM applications such as XYZ stage position feedback in atomic force microscopy, Z axis feedback in semiconductor photolithography equipment, Z axis feedback in precision grinding of bearing races, optics positioning, and engrave head position feedback.
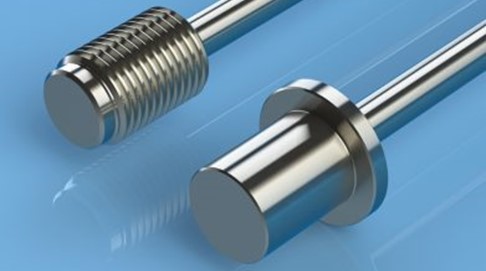
Many sensor options are available for machine condition monitoring, including inductive technology, linear variable differential transformers (LVDTs), laser triangulation, capacitive, and ultrasonic systems, as well air gauging, Hall effect, and optical systems. Each technology has distinct advantages and disadvantages, depending on the application.
Eddy current sensors are generally much more insensitive to environmental contaminants than other options. They operate on the principle of impedance variation caused by eddy currents induced in a conductive target by a sensor coil. The sensor coil is excited by a high frequency oscillator, which generates an electromagnetic field that couples with the target. Signal conditioning electronics sense impedance variation as the gap between sensor and target changes and translates it into a usable displacement signal. This technology provides extremely high (sub-micro inch) resolution.
Eddy current sensors can “see through” non-conductive materials, making these sensors useful in such applications as paint, rubber, and paper thickness. They can also be a good option for operation over a wide variety of temperatures and environments, including dust, oil, gas, diesel fuel, liquid oxygen, and rocket fuel.
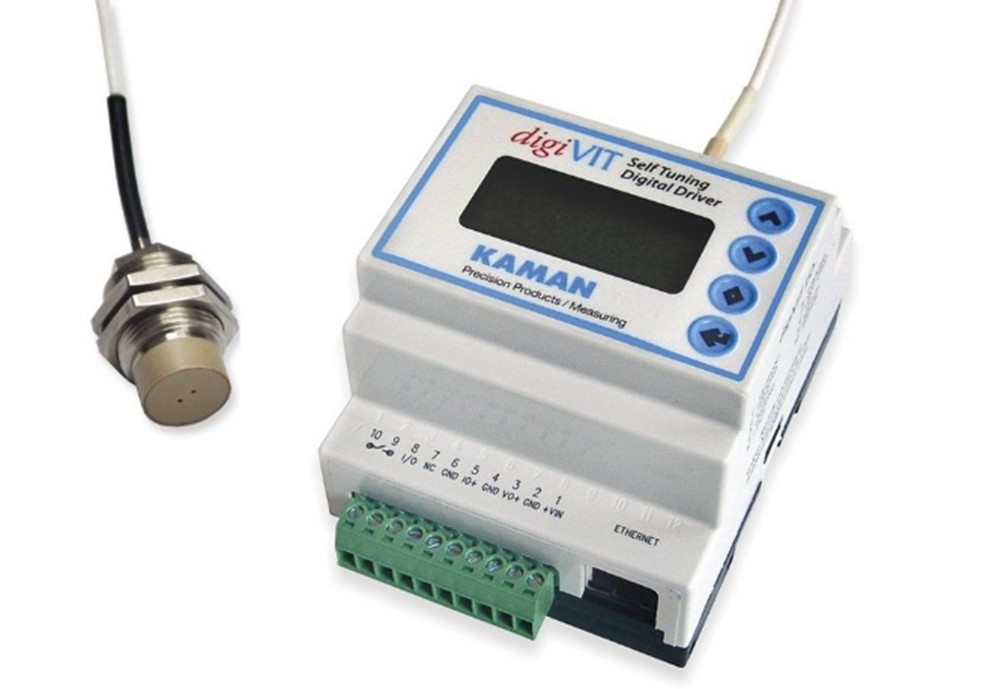
Inductive technology is used for many higher performance sensor applications, especially those needing higher frequency responses in challenging environments and temperatures. They allow operators to monitor a machine and determine when it has to be taken offline for maintenance. Conversely, the sensor may indicate that the machine is running well, so maintenance is not yet required. If, for example, the machine in question is a critical pump operating in an inaccessible location, precise information on machine condition can be critical to a company’s bottom line.
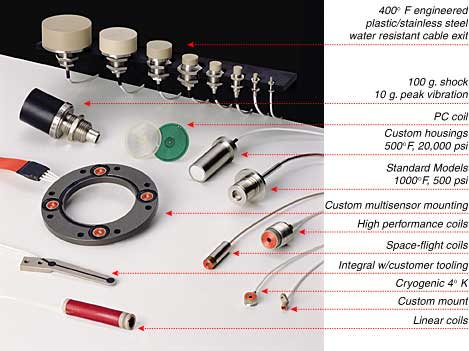
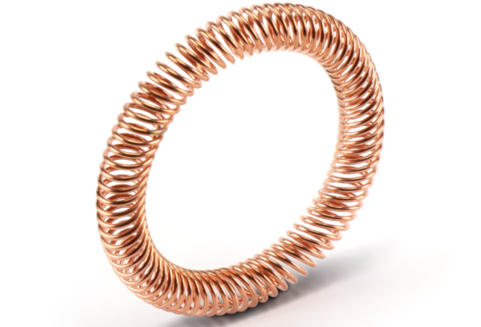
Another Kaman unit, Bal Seal Engineering which Kaman acquired in 2020, also has strong ties to magnetic technology, particularly related to electromagnetic interference (EMI). With the Bal Spring canted coil spring, engineers can protect sensitive electronics in their designs from the harmful effects of conducted or radiated EMI and radio frequency interference. Its independent coils serve as multiple contact points for optimal conductivity in shielding applications, even under shock and vibration. It provides effective attenuation across a broad EMI spectrum, but is particularly effective in high-frequency, small-package applications.
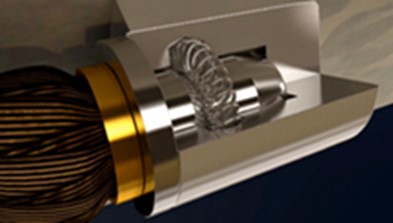
For more info, see www.kaman.com.