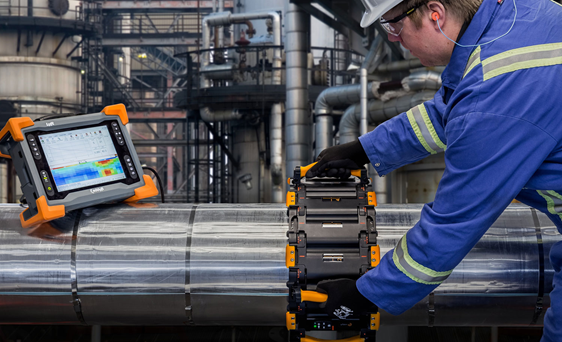
November is Magnetic Sensing Month at Magnetics Magazine!
Stay tuned and check the website frequently for new updates on the latest technology for magnetic sensing.
In the high-stakes world of non-destructive testing where failure to detect flaws can lead to disastrous consequences in energy facilities, pipelines and aircraft, Eddyfi Technologies continues to build its magnetic systems while also growing aggressively into ultrasonic and other methods. Now a formidable global player providing both equipment and crews for testing, in little more than a year the company has tripled in size through acquisitions and expanding business activities.
A hallmark of the company’s capabilities is the ability to detect corrosion under insulation commonly seen as one of the greatest challenges facing asset integrity. Its specialized Pulsed Eddy Current (PEC) system, depicted above, has become a familiar sight where technicians need to quickly screen insulated steel for corrosion.
Earlier this year, the company broadened significantly via the acquisition of Dublin, Ireland-based NDT Global, a leading supplier of ultrasonic inline inspection and integrity (ILI) services. The move brought both a major play in ultrasonic testing to Eddyfi, now part of the new parent company Eddyfi/NDT, as well as a large service operation capable of employing a spectrum of NDT methods.
It capped a string of acquisitions in recent years that have broadened the firm into both a manufacturer of a variety of types of NDT equipment as well as a provider of field services. In about a year’s time, the company has grown from a $100 million operation to $300 million, emerging as a disruptive top player in the NDT market in just the tenth anniversary year for the Quebec-based firm.
“We have spent the past 10 years developing, acquiring and perfecting the most advanced NDT modalities in the world,” said Martin Theriault, CEO of Eddyfi/NDT. “At every level of technology, pushing the limits of NDT to new heights has allowed us to solve critical problems and deliver superior, information-rich data for the benefits of our clients. But selling inspection instrumentation & technology alone in certain very niche and specialized sub-verticals, such as ILI inspection, simply doesn’t suffice. We are therefore excited to join forces with NDT Global and work with them and their clients to take ILI NDT to the next level.”
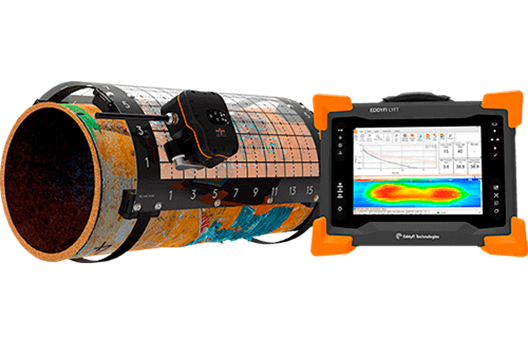
Along the way, its developments in a variety of magnetic inspection methods have been a key factor in propelling Eddyfi forward to new technical capabilities and into new markets. Its pulsed eddy current technology is a good example. Eddyfi makes specialized eddy current instruments such as Lyft along with a line of application specific probes by which the system can be adapted to various structures in the field needing inspection such as pipelines, storage tanks, ships and many more. Its innovative PEC Array Probe employs a six-channel array and slashes the inspection time of single-element probes while accommodating a variety of surfaces and materials.
A PEC system will use a magnetic pulse to induce eddy currents in the bulk of carbon steel components. Cutting the pulse sharply generates eddy currents in the part. The system listens to the decay of these eddy currents and analyzes the signal to evaluate the remaining wall thickness. Recent development in PEC by Eddyfi Technologies has resulted in a drastic increase in both productivity and detection capabilities enabling new applications, notes Gabriel Cyr, applications engineer. An example he describes in a recent blog, available on the company’s website, is how it can be used on ships to find corrosion in steel deck plates, an application of particular interest for navy fleets.
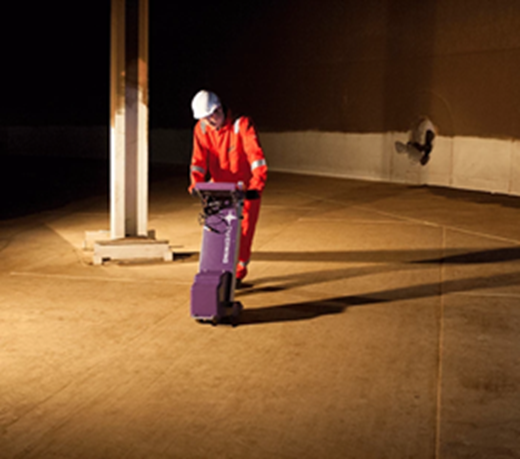
Another innovation, employing Hall effect sensing, has been to combine two of its technologies to elucidate both topside and bottom-side corrosion in the floors of steel storage tanks. The company’s Silverwing Floormap tank bottom inspection system combines Magnetic-Flux Leakage (MFL) and Surface Topology Air-gap Reluctance Sensors (STARS) to quickly generate the two views.
The technique relies upon strategically placed Hall effect sensors to detect the magnetic leaking field that is created by corrosion. On its own, MFL cannot differentiate if the corrosion is topside or bottom side of the tank bottom. Surface Topology Air-gap Reluctance Sensors (STARS), however, is a patented technology that determines whether corrosion is top side or bottom side. When combined with MFL users can switch between top side, bottom side, and complete plate views to show the origin of the corrosion. STARS also provides a simple visual representation of the inspection surface through thick non-magnetic material up to 10 mm thick.
This system is explained by Matthew Kircough, senior application specialist, in another blog that is available on the company’s website. While magnetic flux leakage (MFL) is the most deployed technology for corrosion surveys of storage tank floors, there is a growing demand to report whether corrosion originates at the top surface, the product side, or the bottom surface, the soil side. This is something that cannot be determined from MFL data alone, he notes. Without the use of technology, gathering this valuable information is a time consuming, laborious, error-prone task involving a whole lot of ‘hands and knees’ time.
STARS (Surface Topology Air Gap Reluctance Sensors) is Eddyfi Technologies’ proprietary, patented technology. STARS data is collected alongside MFL data during an inspection and used by the Floormap software to automatically discriminate between soil side and product side corrosion. The amplitude of an MFL signal from a top-side defect is different from the bottom side; STARS in combination with MFL helps reduce this ambiguity. This relatively new technology has already provided substantial real-world benefits to most tank owners, but it is generally not well understood, says Kircough.
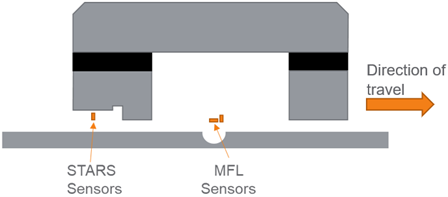
As seen in the image above, the horseshoe shape magnet bridge is suspended over the plate being inspected. The Floormap includes two separate Hall-Effect sensor arrays, one for MFL and the other for STARS, each with a resolution of 64 channels across the 300-millimeter width of the bridge. Hall-Effect sensors are sensitive to magnetic fields that are perpendicular to their surface. MFL sensors are located between the front and rear poles of the magnet to detect magnetic leakage fields caused by corrosion pitting from either the top or bottom surface of the plate. STARS sensors are mounted on the bottom surface of the rear magnet pole and are oriented to respond to top surface variation only.
STARS works on the principle of air-gap reluctance. When scanning over areas with no product side corrosion, the gap will remain mostly constant. The magnetic flux lines will travel vertically, taking the path of least reluctance between the pole and plate surface. They travel parallel to the STARS sensor, do not intersect it, and there is no response from STARS.
For more info and to see the blogs, go to www.eddyfi-ndt.com.