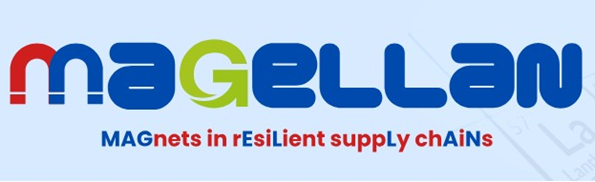
Running from January 2024 to December 2026, Magellan Project aims to revolutionize the way Europe recycles and manufactures permanent magnets. With co-funding from the European Union and a total budget of €7.5M, the project is bringing together a cluster of 15 companies and organizations to pool their capabilities in magnet technology toward the purpose of building a stronger domestic supply chain that can help shape the green transition across the continent, particularly for electric vehicles and wind turbines.
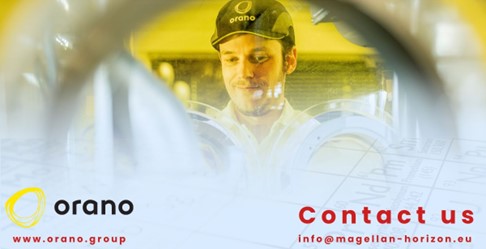
Led by French nuclear fuel company Orano Group, key partners in the consortium are from academia, research and industry in eight countries. Participating also in France’s Magnolia Project which seeks to bring magnet manufacturing back to that country, Orano is emerging as a potential future stalwart in the magnetics industry as it seeks to apply its considerable resources to new areas of activity such as recycling and processing magnetic materials.
Launched in 2022, the Magnolia project brings together industrial and institutional partners including Orano, automotive supplier Valeo, waste management company Paprec, recycler Daimantel France, and the energy R&D institute CEA-Liten, aiming to structure in France a sovereign, competitive, and cutting-edge sector for producing sintered permanent magnets.
Orano is serving as project lead for the Magellan project. With more than 17,000 employees worldwide, the group has know-how in powder metallurgy, industrial production with complex powder in inert atmosphere, process industrialization and management of complex industrial sites. The effort is part of the group’s strategic objective to apply its capabilities to new areas of activity.
Benoit Richebe, Project Director for Rare Earths/Magnets at Orano, provided these insights in an interview with Magnetics Magazine:
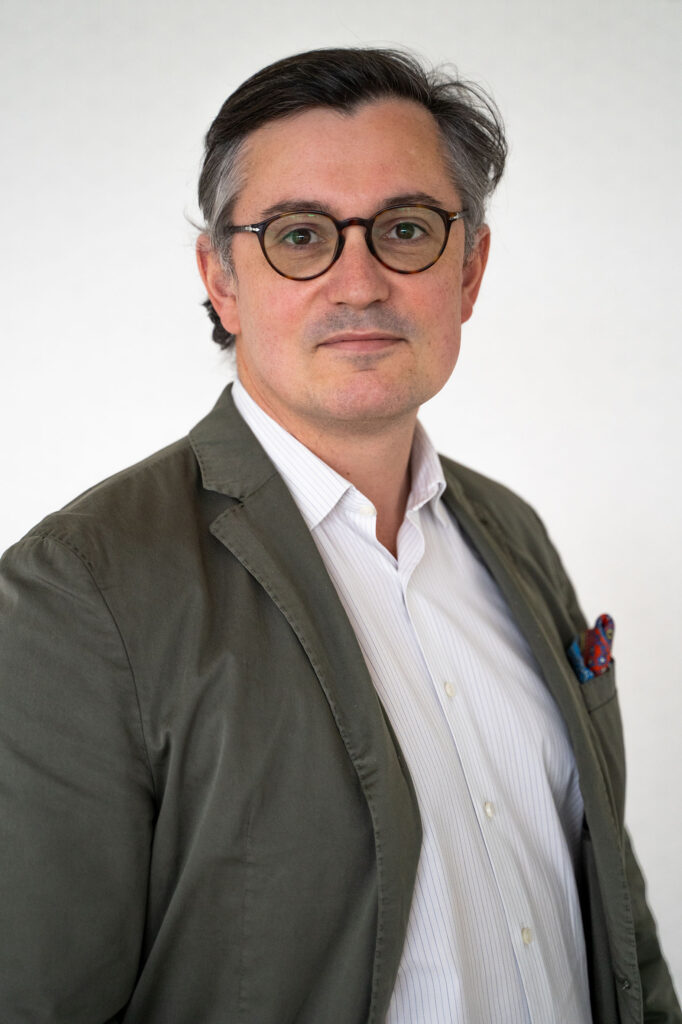
Q. What are Orano Group’s current activities and future plans related to magnets?
Orano is a world expert in nuclear fuel processing and recycling. We also ensure excellence right across the fuel cycle and all services activities to contribute to the production of low-carbon footprint electricity.
Aligned with the Group’s commitment to “develop know-how in the transformation and control of nuclear materials for the climate, for a healthy and resource-efficient world, now and tomorrow, today”, Orano is opening up to new activities in connexion to its areas of expertise and key technical competences:
- Alternative treatments for cancer via targeted alpha therapy
- Production of critical materials (cathode materials and precursors of cathode materials) and recycling of strategic materials from electric vehicle batteries for valorizing them in new batteries components Stable isotope production facility based in our Tricastin plant
- Molten salt reactors (GenIV type of reactor) for reducing the nuclear wastes’ volumes
- The “Rare Earth elements and magnets recycling” (REE and PM -permanent magnets- project) falls into this category of innovative projects, leveraging our technical competences in powder metallurgy and processes’ industrialization.
Permanent magnets are critical components for many rising markets in the near future, including among others: Electric vehicles and wind turbines. The forecast for these two sectors shows a strong growth accompanied by a significant job creation by 2050, and with a strong contribution to attain the carbon neutrality objectives taken by the French Government and the European Union.
Among the different types of permanent magnets, Neodymium-Iron-Boron (Nd-Fe-B) sintered magnets have the highest magnetic energy density at room temperature: they make it possible to design more compact, lighter and more efficient electric motors and devices. In terms of value, they represent a high share of the permanent magnet market, and permanent magnet volumes are expected to double in the decade, generating strong price pressures.
However, high-performance permanent magnets systematically incorporate rare earths metals. About 80%-90% of these metals are currently produced in China (with variations by segment of the value chain), which:
- China holds the world’s largest reserve of rare earths elements and represents the largest mining operations,
- and masters the entire value chain up to the finished product.
A quasi-monopoly that places France and Europe in a situation of high dependence, and constitutes a strategic risk for both the economy and the energy transition.
he ambition of the REE and PM project is to structure on French soil an industrial tool for the manufacture of sintered Nd-Fe-B permanent magnets, from independent material sources, to initiate a sovereign, competitive and efficient sector.
To do this, the project will work on 4 axes:
- The development of innovative technologies for the manufacture of sintered magnets and their deployment on pilot manufacturing lines.
- The development of a scheme to secure supplies and production of magnets outside Asia.
- The preparation in France of a competitive sector of collection, dismantling and recovery of electric motors.
- The reduction of the environmental impact: recycling of magnets, reduction of manufacturing waste, recovery of rare earths, ecodesign of electrical machines facilitating the dismantling of motors and the recovery of magnets.
Tell us about the Magellan Project.
MAGELLAN is a ground-breaking project funded under Horizon Europe, running from January 2024 to December 2026 with a total budget of €7.5M. Its goal is to revolutionize the way Europe recycles and manufactures permanent magnets (PMs), a key component in advanced technologies that will shape the green transition across the continent, like for example electric vehicles (EVs) and wind turbines.
The project brings together 15 partners from 8 European countries. Its renowned experts from academia, research and industry will work jointly to find the best recycling and manufacturing routes for permanent magnets used in electric vehicle traction motors. Starting from our good ideas validated in a lab environment, we will make every endeavour to make them work in real life conditions in order to pave the way for a complete EU supply chain in the longer term.
The MAGELLAN solution will:
- Increase the reuse of rare earth elements (REE) from end-of-life magnets, achieving up to 50% improvement in yield
- Contribute to the reduction of PMs’ CO2 emissions of up to 50% when compared with standard magnet manufacturing processes
- Avoid mining operations equivalent to 535 tonnes of light REE per year
- Increase material- and cost-effectiveness of the REE recycling process
- Pave the way for a 2000 tonnes/year supply chain, about 10% of the 2040 forecasted European market for electric vehicle traction motors (EVTM).
MAGELLAN is a step towards a greener and more self-sufficient Europe. By improving the recycling of rare-earth magnets, the project will make sure that the European Union stays at the cutting edge of the green transition, thus securing a cleaner, more sustainable future for all of us.
Tell us about the timeline: when did it begin, what is the current status, what is ahead?
On top of its R&D and industrialization efforts engaged in MAGNOLIA* and MAGELLAN projects (and other to come!), studies have already started for a state-of-the-art industrial pilot. The Final Investment Decision of the industrial pilot is expected by early 2025. Based on its long-lasting experience with complex powders, Orano considers that industrialization of these advanced processes will be key.
The industrial plant will be positioned immediately afterwards in order to kick start operations before the end of the decade, for both recycling and manufacturing of high quality sintered NdFeB magnets.
Please describe Orano Group’s technical capabilities for magnet recycling.
Although Orano has mastered hydro-metallurgy processes, it focuses on the recycling short loops in order to be more sustainable and cost effective instead of the long loop. In such loops, scrap magnet material is incorporated with primary raw material, either in a melting furnace (melting / fusion route) or blended in powder form at milling stage (powder route). Different innovative strategies will be applied according to the scrap magnet material composition and degradation state.
The material follows the other conventional process operations up to the magnetization stage to become a permanent magnet. Many of these steps call on Orano’s expertise in Mixed Oxydes (MOx) fuel fabrication, in particular with regard to the particle size control and powder blending, shaping, sintering.
Magellan Project overview, other partners and their roles
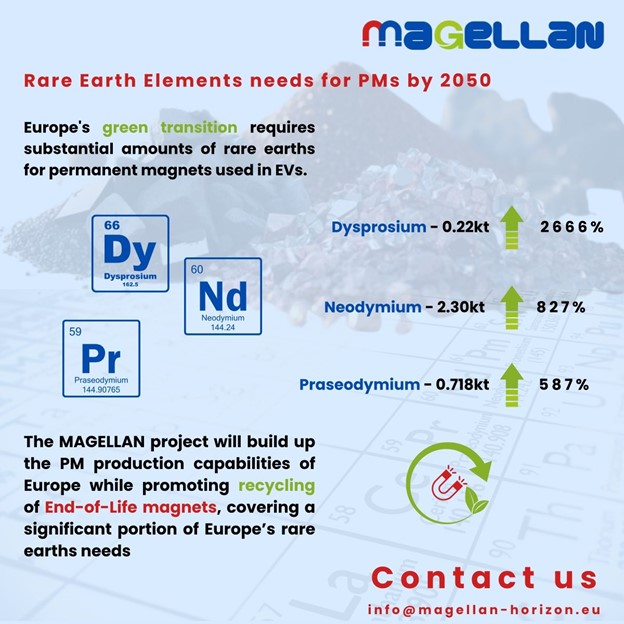
Through innovative techniques such as neodymium substitution and functionally shaped permanent magnets through powder injection molding, the partners plan to produce a new EVTM rotor design that improves assembly, motor performance, reduces permanent magnet content and facilitates dismantling of end-of-life motors. The project’s optimization of magnet recovery and recycling seeks to minimize the dispersion and dilution of heavy REEs, avoid downcycling, and support standardized magnet labelling.
Among other Magellan partners and their roles are:
- IFP Energies Nouvelles, a French research organization in the fields of energy, transport, and the environment, will focus on the qualification of magnets for electric vehicle traction motors (EVTM), integration of recycled permanent magnets in existing EVTMs currently in production, prepare the inverter and controller for the EVTMs and validate the new rotors in endurance testing. They will also contribute at establishing recommendations for the design of magnets and EVTMs to facilitate dismantling, labelling, and validation of end-of-life magnets.
- The GeMMe research group at the University of Liege brings together a team of engineers, scientists and technicians from different disciplines focused on recycling end-of-lief heavy rare earth elements-rich permanent magnets. They will develop characterization protocols and specifications to qualify PM materials for their ideal recycling routes. Their innovative thermos-mechanical technique for PM extraction will also be tested to evaluate its efficiency on different rotor designs, seeking a seamless integration with Magellan’s recycling loop.
- Magneti Ljubljana, a manufacturer of permanent magnets, bonded magnets, and magnetic systems located in Slovenia, will produce specialized powder batches, conduct injection tests, and implement grain boundary diffusion processes. It will also participate in the demonstration of the MAGELLAN solution on a pre-industrial pilot line.
- CEA brings its expertise in advanced materials and energy solutions to the project, focusing on the production of alloy batches and the optimization of powder injection molding processes, aiming to achieve improved magnet properties through recycling.
For more info, see Magellan Project on LinkedIn, and www.orano.group.