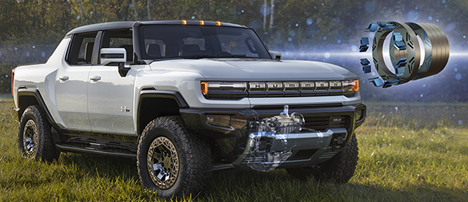
HRL Laboratories, LLC, has begun work on the surface laser architected magnets (SLAM) project to improve magnets within electric vehicle motors, a new Advanced Research Projects Agency-Energy (ARPA-E)- funded effort.
In current EV motors, notes HRL, permanent magnets can present design obstacles due to the heat generated during operation. Expensive heavy rare-earth elements like dysprosium and terbium are added to conventional magnets to prevent demagnetization at elevated temperatures and maintain performance.
“The SLAM project aims to increase the temperature capabilities of magnets. By tailoring permanent magnet architectures, we can mitigate demagnetization and minimize the use of costly, heavy rare-earth elements largely sourced non-domestically,” said Brennan Yahata, HRL’s principal investigator on SLAM. “We’re targeting magnet and motor power density improvements specifically at the operating temperatures of these magnets. Magnet and motor architecture is an exciting, high-value research area in permanent magnet material solutions for EV manufacturers. This kind of technology can create opportunities to rethink electric motor design.”
Yahata also said that in contrast to other research efforts that seek entirely new magnet materials, HRL’s approach is to improve existing magnets by tailoring material architecture at the microstructure level.
HRL will work with General Motors to apply the latest laser-based manufacturing methods to engineer magnets for use in electric vehicles. Over the course of the 3-year, $2.6M program, HRL will develop and fabricate improved magnets and GM will integrate them into electric motors and test their performance.
“By applying additive manufacturing technology to selectively target the surface, we can not only use a minimal amount of rare earth elements but also effectively apply them where they are needed most,” said Raymond Nguyen, HRL materials engineer and fabrication lead on SLAM.
HRL’s approach is to reduce the use of heavy rare earths by locally optimizing the crystallographic orientation of the microstructure on the magnet’s surface. Using laser-based post-processing methods, it magnetically hardens the weakest points on a NdFeB magnet surface against demagnetization, which enables higher torque and more energy efficient motors. By increasing demagnetization resistance, the extent of usable magnetic energy produced at elevated operating temperatures can be increased up to 2X in permanent magnets.
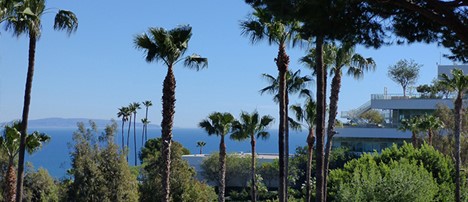
Based in Malibu, California, HRL is a corporate research-and-development laboratory owned by The Boeing Company and General Motors specializing in research into sensors and materials, information and systems sciences, applied electromagnetics, and microelectronics. It was established in 1948 as Hughes Research Laboratories and today is known as one of the world’s premier physical science and engineering research laboratories. Now located on several campuses in southern California, it has over 250,000 sq ft of laboratory space and 10,000 sq ft of Class 10 clean room. See www.hrl.com.