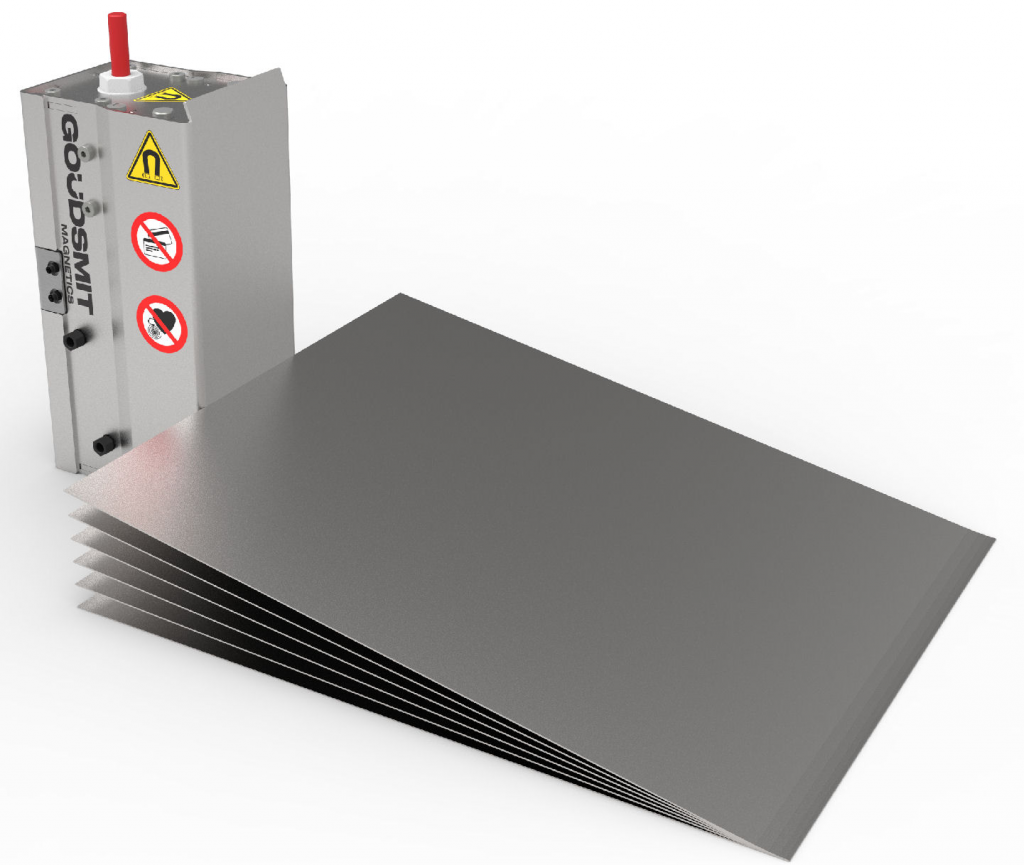
Goudsmit Magnetics, a producer of magnetic systems based in The Netherlands, has recently developed an innovative fail-safe neodymium magnetic sheet separator and, in another project, is providing magnetics expertise to developers of a visionary hyperloop transportation project for Europe.
Equipped with powerful neodymium magnets that can be switched on and off pneumatically using a new patented system, the separator provides automatic separation of steel sheets up to a thickness of approximately 4 mm. This switching is done quickly by rotation of the magnets.
Its unique spring-actuated off position feature makes the equipment extremely safe, says the company. it automatically switches to the off position even if the compressed air supply is interrupted and even at full load at maximum stacking height. The magnet cannot accidentally remain switched on during maintenance either, preventing a situation that can often lead to industrial accidents.
In contrast to fixed sheet separators, switchable sheet separators also allow interim changeover of products during a set process. The new unit can separate steel sheets of almost any shape, length or width, even round and asymmetrical shapes. The permanent magnetic force does not degrade and is guaranteed for decades.
Magnetic sheet separators are used in sheet processing industries and in robotized cells for producing welded assemblies. Robots use magnetic grippers to pick up large sheet metal parts and position them on a welding table. Because the steel sheets are oiled, they stick together, and the robot occasionally picks up two sheets at the same time. Consequently, the second steel sheet may release halfway across the welding table and fall. This can cause tremendous damage in high-tech environments where the welding table is often equipped with sensors, transducers and actuators. Moreover, the double insertion of two steel sheets that are stuck together can cause extensive damage to a die.
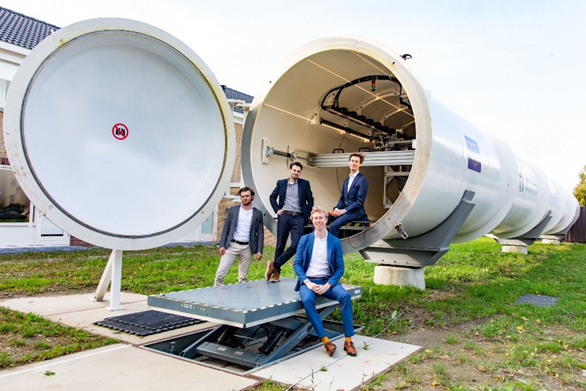
The Hardt hyperloop is being designed as a pneumatic tube dispatch system that transports people and goods at high speed, relying intensively on magnetic technology to function. Inside the tube is a vacuum. With no air resistance or friction, transport pods are expected to reach speed of 1000 km per hour, perhaps even faster at 1200 km per hour.
Unlike a magnetic levitation train, the tube contains a capsule or pod that is suspended from magnets, making it float. Electronics regulate the magnetic field so that the capsule can move through the tube and slow down. The project envisions that by 2030 there could be a 10,000-kilometer tube network alongside the current highways or railways, connecting the main cities of Europe stretching from Sweden to Istanbul and from Moscow to Malaga.
The Hardt effort derives from entrepreneur Elon Musk’s 2012 competition to find the most realistic design for hyperloop transportation. Students from Delft University of Technology won this competition of 300 entries and then founded Hardt. They approached Goudsmit for the magnets and magnetic design.
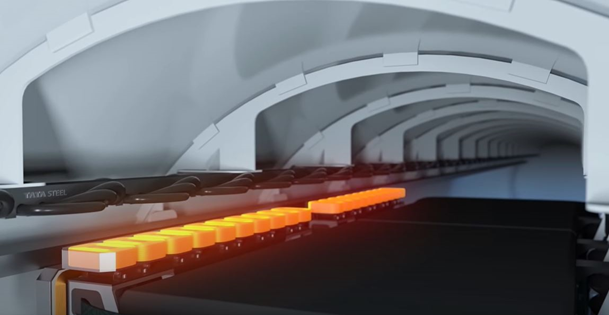
Magnets ensure that the capsule floats freely in the tube, they push it forward and they provide stability so passengers and freight won’t be shaken back and forth even at enormous speeds or during track changes. The magnets need to be particularly strong, notes Goudsmit, because the passengers and luggage together weigh quite a bit. Magnets also make it easy to change tubes, so that you can turn right or left at full speed without any stops. Hardt and Goudsmit have developed a fast changeover technology which sets the Hardt project apart from other hyperloop development programs (see www.MagneticsMag and query “hyperloop”).
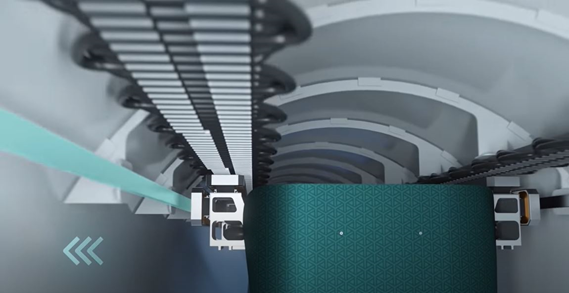
The hyperloop switch allows the vehicle to pass from one track to another, creating a network of tubes connecting multiple cities. What makes this hyperloop switch special is that it allows the vehicles to change tracks without slowing down, decreasing travel time without any moving parts.
The system uses both neodymium permanent magnets and electromagnets. The permanent magnets have sufficient magnetic attraction and are positioned and stabilized by the electromagnets. As a result, the suspension system uses virtually no energy. The combination of the two types of magnets allows the technology to lift more than the weight of a car using only the amount of energy necessary to turn on a light bulb.
The project is not without considerable challenge, notes Goudsmit. “Our R&D engineer has calculated that one Hyperloop route from Amsterdam to Frankfurt would require more material than the three largest mines in China can supply for that route. That’s far too little, so we need to look for other sources,” says the company.
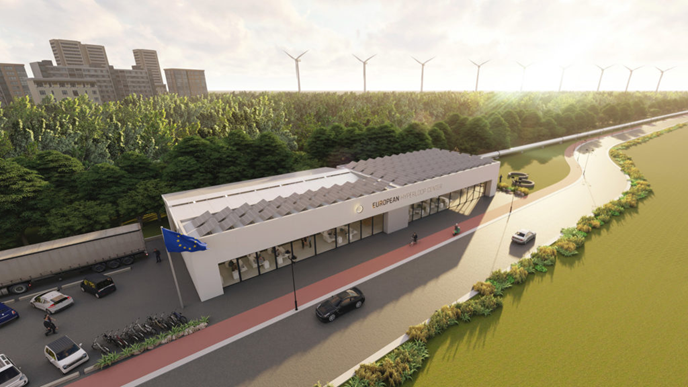
Other partners in the Hardt venture include electrical steel maker Tata Steel and automotive company Continental. Dutch clean energy company Koolen Industries is a financial backer.
For more info, see www.goudsmitmagnets.com and https://hardt.global.