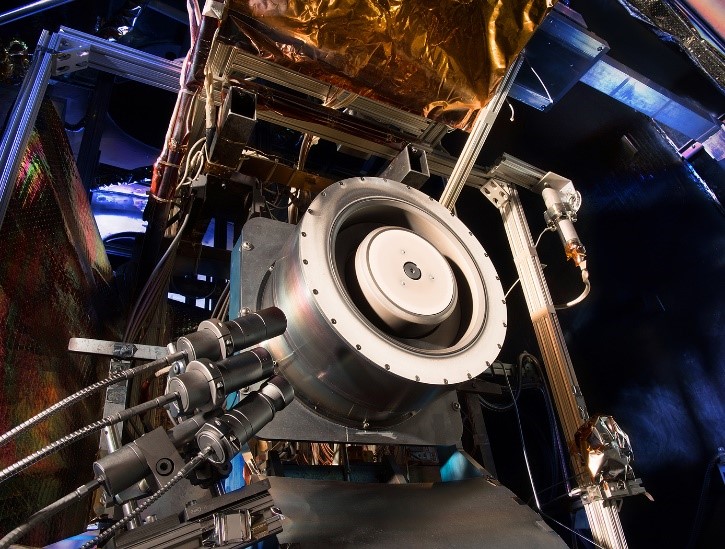
Electric propulsion, which often relies on advanced Hall Effect thrusters (HET), may have been around for more than 50 years, but it still has huge potential. It is being integrated in many cubesats and will also play a big role in the area of sattelite servicing of crewed missions to the Moon including the Lunar Orbital Platform-Gateway and exploration missions that go deep into, or even beyond, our solar system.
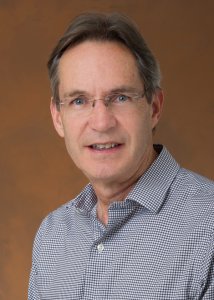
The capabilities of electric propulsion are becoming more apparent and are seen as a real game changer in future missions, according to Dr. John Brophy, engineering fellow and principal engineer of electric propulsion at NASA’s Jet Propulsion Laboratory in Pasadena, CA. He will be presenting a workshop at the upcoming SpaceTech Expo in Pasadena highlighting the history of electric propulsion as well as some key challenges, areas of research and a future outlook on what electric propulsion can bring to the aerospace business. Key learning objectives will range from an overview of the different types of electric propulsion systems, to current standards and certifications for electric propulsion systems and future prospects for electric propulsion in the coming decade.
This workshop will be one of many featured at Space Tech Expo 2019 which takes place the week of May 20 this year in Pasadena. The event is a leading showcase of space technology and services for spacecraft, satellite and launcher systems, sub-systems, components and materials for civil, military and commercial space.
Space Tech Expo USA unites thousands of industry leaders, decision makers, engineers, specifiers and buyers with the manufacturers and supply chain for civil, military and commercial space to network, discover the latest innovations, and grow their businesses. The Space Tech Conference runs alongside the expo and welcomes space and defense executives and technical leaders to hear industry heavyweights share their technical expertise, real-world case studies, and insights on industry trends.
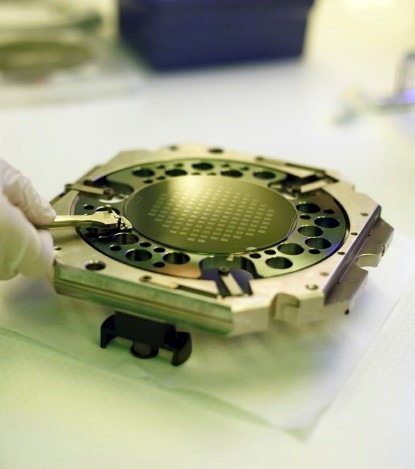
Innovators at NASA’s Glenn Research Center in Cleveland have developed new technologies that increase the operational lifetime of a HET, which is used primarily on Earth-orbiting satellites and can also be used for deep-space robotic vehicles. The operational lifetime of HETs is determined by the amount of time the thruster can operate before the plasma within the channel damages the magnetic system. Prior to this innovation, the plasma would erode the ceramic chamber of the HET in just over a year of operation.
The breakthrough prolongs this operational lifetime through two related innovations. The first is an innovative magnetic field configuration that provides magnetic shielding to eliminate interactions between the high energy xenon plasma produced by the HET and the ceramic chamber that contains it. The second is a means of replacing eroded discharge channel material via a channel wall replacement mechanism. By increasing the lifetime and efficiency of HETs, Glenn’s technology will enable a new era of space propulsion. HET lifetime is extended five times from approximately 10,000 hours to more than 50,000 hours.
Used for propelling Earth-orbiting satellites and deep-space robotic vehicles, the HET gets its name because it traps electrons with an intense radial magnetic field in an azimuthal Hall current moving around the circumference of an annular ceramic channel. The electrons in the circulating Hall current ionize the onboard propellant – the inert gas xenon – and create an ionized plasma. The xenon plasma is then accelerated axially, via an applied electric field along the coaxial channel, to an exit velocity of up to 65,000 miles per hour to produce thrust. The interaction of the accelerated plasma and the downstream edge of the channel, where the plasma is the most energetic, results in erosion of the surrounding magnetic system used to generate the plasma. One of NASA Glenn’s novel designs relies on an azimuthally symmetric configuration that minimizes radial magnetic fields at the discharge chamber walls. This configuration completely shields the walls of the discharge chamber from the high-energy plasma ions. With regard to the discharge-channel-wall replacement innovation, an actuator can be configured to extend the discharge chamber along the centerline axis. The actuator can be either mechanical or programmable. In either case, the sleeve can be extended while an upstream portion of the discharge chamber remains stationary, thereby preventing plasma exposure. These novel designs increase the efficiency and extend the lifetime of the HET to five times that of unshielded thrusters, enabling a new era of space missions.
For more information, visit: http://www.spacetechexpo.com/ and https://www.nasa.gov/