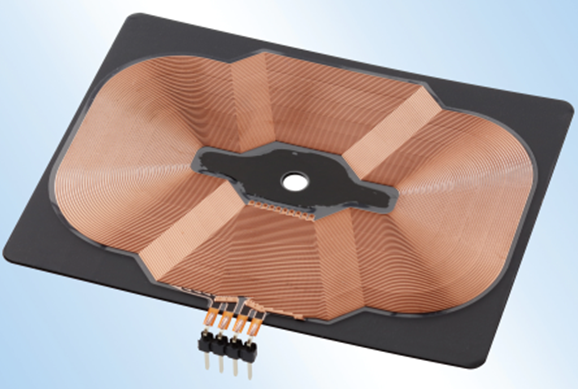
Linking new plating technology with its core competency in magnetic materials, TDK has developed a novel thin pattern coil that could revolutionize wireless charging of mobile devices. The new approach applies the magnetic material in a copper pattern on a thin film instead of the traditional process using winding wires, achieving a five-fold reduction in thickness. Mass production began in May and the company has already begun construction of a new plant in Japan to rapidly scale up further development and manufacturing.
The coil was developed without employing conventional lithographic exposure and etching techniques. Instead, TDK’s game-changing process technology was leveraged, in combination with plating technology using nano-dispersion of the organic compound polypyrrole, developed by Achilles Corporation, a Japanese plastics processing manufacturer.
Although wireless charging coils have generally been produced by winding wires, this new approach has made it possible to manufacture them using a thick copper pattern on a thin film. This, along with the application of TDK’s proprietary magnetic materials has enabled coil thickness reduction down to 0.76 mm which is approximately one-fifth of the thickness of traditional 3.8 mm diameter wound wire coils.
The use of TDK’s original optimal coil shape pattern means that the new coils cover a larger charging area, resulting in greater user convenience. Additionally, while it was previously necessary for three coils to be incorporated into wireless charging systems, now only one coil will be required, thereby enabling system miniaturization.
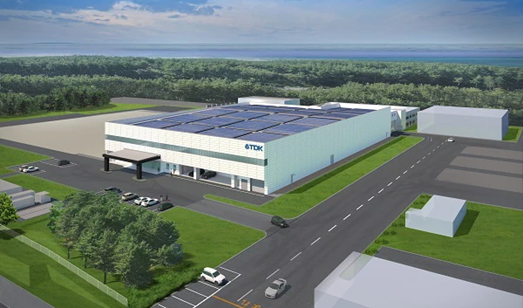
Separately, TDK has announced that it is building a new highly automated factory in Japan for the production of its wireless charging coils and modules. Plans call for construction to be completed in April 2023 and mass production at the facility to begin in September 2023. The Inakura Factory West Site is located in Nikaho City, Akita Prefecture along the Sea of Japan northwest of Sendai. The two-story plant will have about 13,000 square meters of floor space.
Key technical advancements are planned for the factory. It will operate its electricity needs with 100% renewable energy, supported by power from a new offshore wind farm. Also, it will respond to the labor shortage that has confronted the domestic manufacturing industry in Japan in recent years by building a futuristic factory that achieves labor saving in the production processes, says the company.