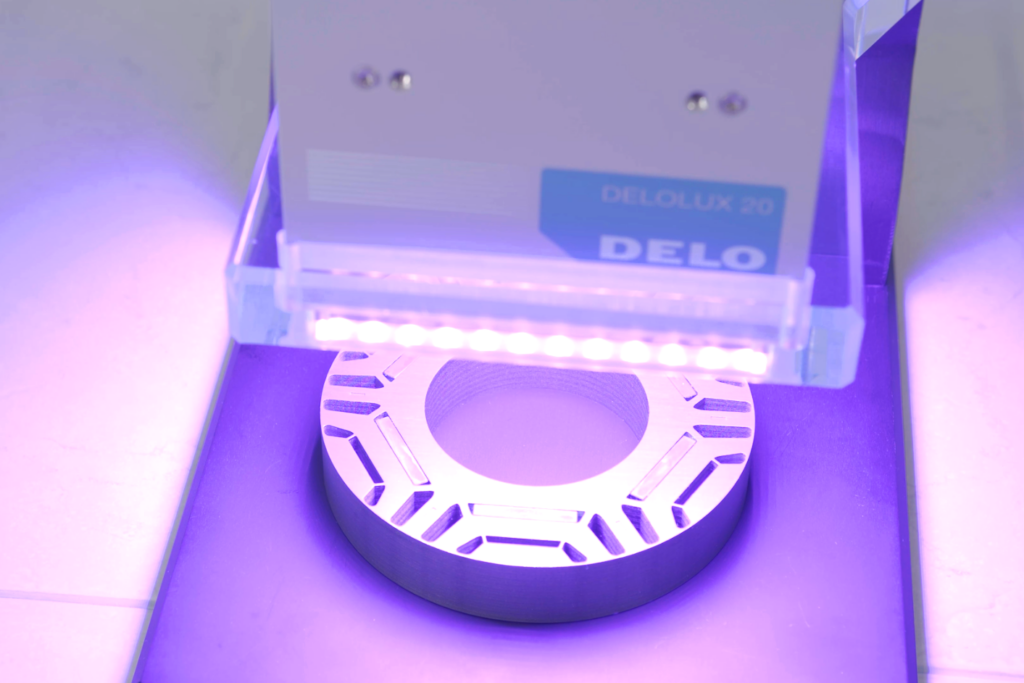
DELO has developed its first dual-curing, high-temperature adhesive for electric motor applications. DELO DUALBOND HT2990 is designed for use in multiple processes, including magnet bonding and magnet stacking in electric motor manufacturing.
With the increase in the production of electric vehicles, durable adhesives to bond electric motors, as well as efficient processes that help streamline production and meet high demand, are critical. That is why DELO has developed DELO DUALBOND HT2990.
It is the first high-temperature-resistant structural adhesive capable of light fixation. This supplemental means of curing helps electric motor manufacturers quicken assembly processes and optimize efficiency in their production, achieving light fixation in 5 to 10 seconds.
In magnet bonding, while heat is the standard method of curing, complementing it with light fixation creates an already-cured outer layer that helps keep everything in place. The adhesive does not seep outside or onto the motor laminations. In magnet stacking, supplementing heat curing with light fixation lets you forego having to keep magnets under a jig in the oven to reach the desired bondline thickness.
Final curing with heat takes 30 minutes at 150 °C or 60 minutes at 130 °C. If exposure to heat occurs later in electric motor assembly, for example via heat shrinkage, there is a possibility for the heat curing step to be skipped. Induction curing can be another alternative to oven curing as well.
At room temperature, DELO DUALBOND HT2990 can achieve a compression shear strength of up to 70 MPa on steel. This compares to 45 MPa achieved by standard high-performance heat-curing epoxies. It also has a high glass transition temperature of 165 °C. In heat as extreme as 180 °C, it still exhibits a tensile shear strength of 7 MPa on aluminum. This is equivalent to 70 kg/cm² of force, a very secure bond.