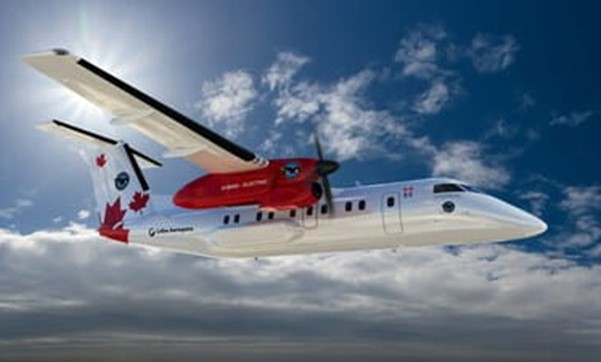
Powered by its breakthrough 1MW permanent-magnet motor, bolstered by a new lab for advanced electric systems and developing a 1MW generator for the military, Collins Aerospace is lifting electric propulsion and electrified power for aviation to new heights. Engineers at the company are developing a family of motors and integrated power systems for broad application in future hybrid and fully electric aircraft as they participate in a range of R&D projects spanning North America and Europe.
Many of the efforts are collaborations with sister company Pratt & Whitney. Both companies, along with Raytheon, are business units of newly named RTX, formerly Raytheon Technologies, which was formed three years ago when Raytheon merged with United Technologies. Today, RTX is the world’s largest aerospace and defense company with 180,000 employees and sales of $67 billion, headquartered in Arlington, Virginia.
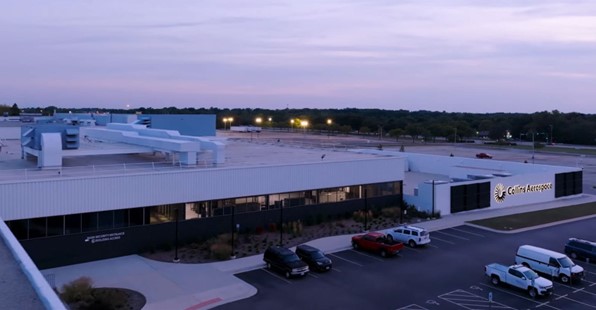
In a ceremony at its Rockford, Illinois campus in October, Collins celebrated the opening of The Grid—a $50 million advanced electric power systems lab. Collins will use the new facility to develop and test key components for hybrid-electric propulsion and more electric systems, a central pillar of the aviation industry’s drive to achieve net-zero carbon emissions by 2050.
“Hybrid-electric aircraft will help our industry significantly reduce carbon emissions, and with The Grid, the most sophisticated lab of its kind, we are investing to help these aircraft take flight,” said Henry Brooks, president, Power & Controls for Collins. “In the coming years, we will use The Grid to break new ground in the development of electric systems that are more powerful, more efficient and lighter than ever before. And in doing so, we will help create a new generation of green aircraft that operate more sustainably with reduced impact on our environment.”
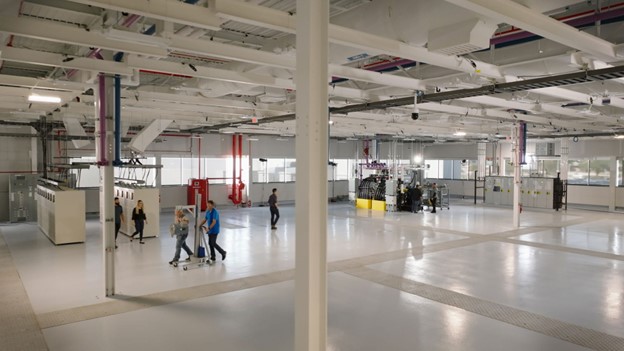
At the opening, Collins displayed its 1MW motor and for the first time unveiled a 250 kilowatt motor. As Collins leaders explained, the company’s technology roadmap calls for a family of electric motors that can be scaled up or down to meet the needs of all aircraft segments including both hydrid and fully electric.
“Across the industry, airframers are exploring electrification options for a range of different platforms including unmanned aerial vehicles, business jets, helicopters and single-aisle planes,” said Brooks. “Whatever the application—whether commercial or military, hybrid-electric propulsion or more electric systems—we are working to ensure Collins is ready with the latest electric technology to meet our customers’ needs.”
In June at the Paris Air Show, a critical milestone in the hybrid-electric flight demonstrator program was announced, completion of a rated power test of the 1 MW electric motor developed by Collins. The motor will be combined with a highly efficient thermal engine, developed by Pratt & Whitney, as part of a hybrid-electric propulsion system that aims to demonstrate a 30 percent improvement in fuel efficiency and CO2 emissions compared to today’s most advanced regional turboprops.
“With its industry-leading power density and efficiency, our 1MW motor will help to significantly reduce aircraft carbon emissions by supporting hybrid-electric propulsion architectures on the next generation of commercial platforms,” said Brooks. “As the motor’s development continues apace, each milestone brings us one step closer to hybrid-electric flight and our industry’s shared commitment to net-zero carbon emissions by 2050.”
Compared to Collins’ most advanced electric motor generators flying today, the 1MW motor will deliver four times the power and twice the voltage, with half the heat loss and half the weight. The company is developing the motor at Collins’ facility in Solihull, United Kingdom, and testing it at the University of Nottingham’s Institute for Aerospace Technology.
Following on from the first low speed engine run at a Pratt & Whitney Canada facility in Longueuil, Quebec in December 2022, testing of the combined hybrid-electric propulsion system – including both thermal engine and 1MW motor – will continue through 2023. The propulsion system and batteries will be integrated on a Dash 8-100 experimental aircraft, with flight testing targeted to begin in 2024. The project is supported by the governments of Canada and Quebec.
“Hybrid-electric propulsion technology offers significant potential to optimize aircraft efficiency across a range of future aircraft applications and is a key part of our technology roadmap for supporting more sustainable aviation,” said Jean Thomassin, executive director new products and services, Pratt & Whitney Canada. “Aside from leveraging the deep expertise of Pratt & Whitney and Collins engineers within RTX, our project draws from extensive collaborations across Canada’s aerospace ecosystem and around the world.”
Clean Aviation SWITCH project in European Union
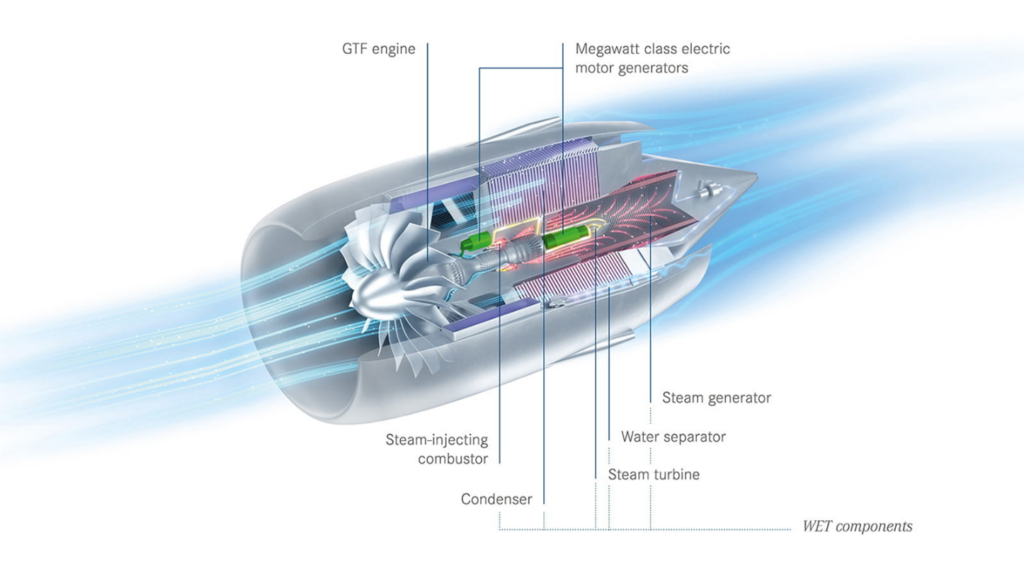
The 1 MW motor is also a key element in the European Union’s SWITCH project where a group of aerospace technology companies are collaborating to develop hybrid-electric and water-enhanced turbofan technology for future aircraft propulsion systems. The Sustainable Water-Injecting Turbofan Comprising Hybrid-Electrics (SWITCH) project is focused on developing a novel propulsion concept built from two revolutionary and synergetic technologies: water-enhanced turbofan and hybrid-electric propulsion. By combining these technologies with Pratt & Whitney’s GTF engine architecture, the concept aims to significantly enhance efficiency and substantially reduce emissions across the full operating envelope of an aircraft.
Generator for Air Force Research Laboratory
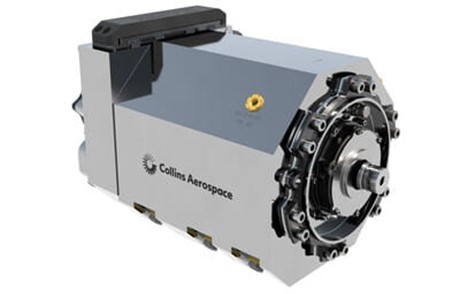
For the Air Force Research Laboratory (AFRL), Collins is developing a 1 megawatt electric generator. The low-spool generator could have multiple applications for future manned and unmanned military platforms. With the addition of advanced mission systems, avionics and high-energy weapons, the next generation of military aircraft will require more onboard electric power than ever before. Applied another way, the generator could be paired with a fuel-burning engine in a hybrid-electric propulsion architecture. In this way, the generator could help increase fuel efficiency to maximize aircraft range, minimize aerial refueling needs and reduce carbon emissions. The company aims to deliver hardware to the AFRL and test the generator to Technology Readiness Level 5 in 2024 using The Grid facility in Illinois.
“While future military aircraft continue to take shape, one thing we know is that these platforms will require electric power in the megawatt range,” said Brooks. “To that end, we’re working with the AFRL to design a generator that will give our customers the onboard power they need and the flexibility to tailor its use for multiple potential applications.”
500 MW motor
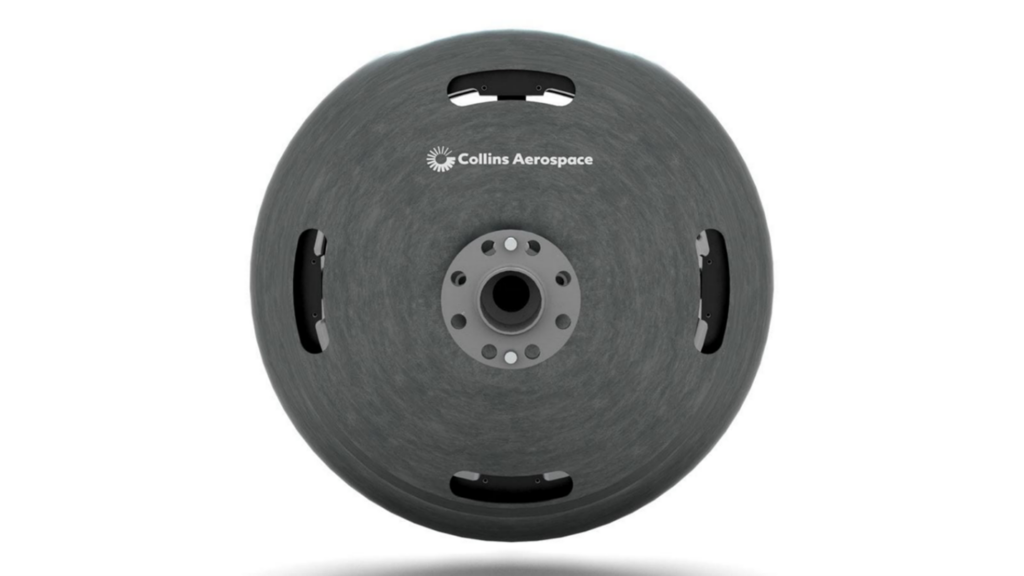
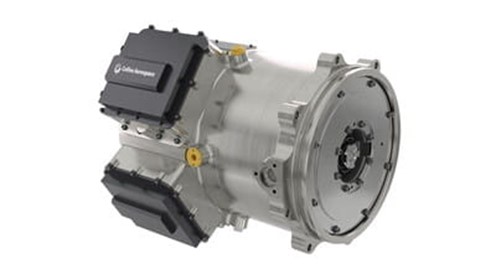
For the 2,000 RPM permanent magnet electric motor, Collins targeted specific power density levels of 9 kilowatts per kilogram and 98% efficiency through the use of a novel motor topology and composite construction. Collins engineers designed the motor at its Electronic Controls & Motor Systems Center of Excellence in Solihull, UK, where it’s also developing its 1 megawatt electric motor and motor controller for the Pratt & Whitney Canada regional hybrid-electric flight demonstrator.
For more info, see www.collins.com, www.prattwhitney.com.