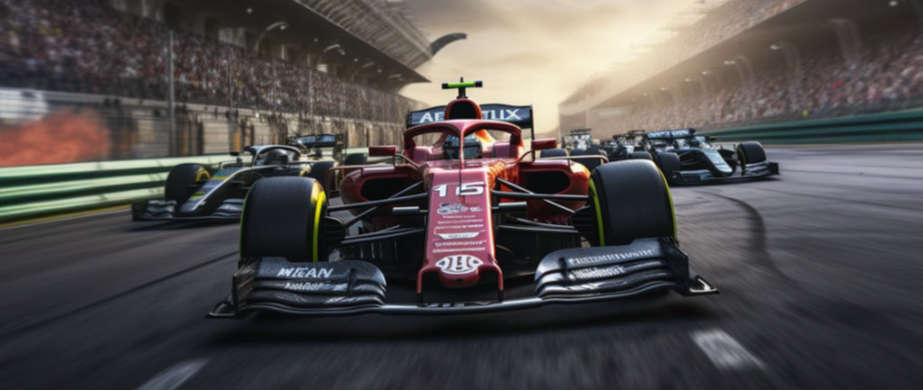
Introduction
Magnet quality matters for the performance of permanent magnet electric motors. That is the main conclusion of this case study, where we show that e-motor manufacturers can realize an impressive factor of 2x to 4x improvement on key motor performance characteristics, such as torque ripple and cogging torque, by optimizing magnet quality in the early stages of motor production. These results open up new possibilities for high-end electric motor/generator applications. In the automotive sector these include motor sports and high performance consumer cars, as well as the broader electric mobility market. The results equally apply to other application fields of electric motors, such as aviation, industrial automation, consumer goods and medical equipment. Keep reading to find out how Magcam can help you unlock the untapped potential of your permanent magnet electric motors.
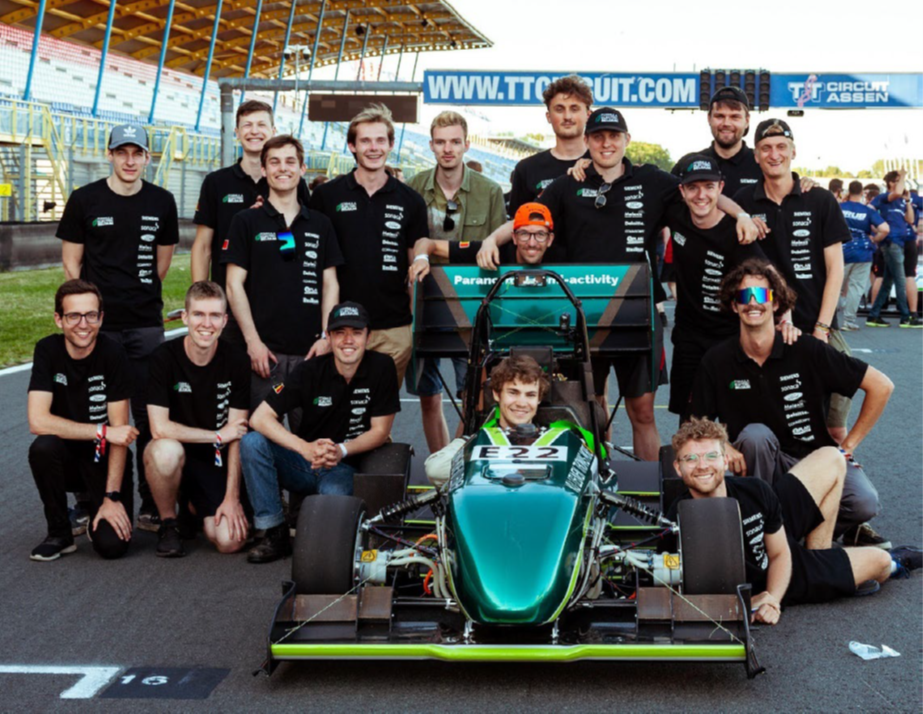
Background
When the Formula Electric Belgium team sought to optimize the performance of their 2023 season race car, they partnered with Magcam, expert in magnet inspection, and Fischer Elektromotoren GmbH, a top-tier German electric motor manufacturer, to ensure magnetic quality in their four radial-flux permanent magnet synchronous electric motors, one for each wheel. While Fischer supplied the magnets and took charge of rotor and motor assembly, Magcam’s expertise centered on ensuring the magnetic quality of these electric motor rotors. This was accomplished using Magcam’s unique magnetic field camera measurement technology, combined with its advanced data analysis capabilities, applied to both the individual magnets, before assembly, and to the assembled rotors.
The objective was not only to enhance the performance of the vehicle but also to provide a comparative analysis by creating a ‘worst-case’ rotor made from deliberately chosen poor quality magnets. Keep on reading to find out how Magcam achieved this and what can be learned from the results.
Magnetic Field Measurements and Selection of the Magnets
Individual Magnet Scans by Magcam
The study started with Magcam employing its sophisticated magnetic field camera Combi Scanner to measure high resolution magnetic field distributions of 200 magnets provided by Fischer. The batch size was far larger than the number of magnets needed for the rotors, since it was anticipated that a substantial portion of the magnets would have to be rejected based on their quality.

The measurements involved stepping Magcam’s MiniCube3D magnetic field camera over the magnet surface in a few steps at high speed and subsequently stitching the individual frames together. The integrated onchip 2D array of over 16000 Hall effect sensors allowed for short cycle times, limiting the full batch measurement time to a few hours. From the subsequent analysis of the measured magnetic field distribution data emerged an array of quality parameters for each magnet, including magnet strength, magnetization angle error, and localized magnetic homogeneity maps, allowing in-depth quality assessments, unparalleled by any other magnetic inspection technique.
After pouring these results in histograms, the quality variation within the batch of magnets could be visualized and further analyzed. The objective? To identify the most optimal magnets from the batch for the race car rotors, while also selecting a set of inferior quality magnets for a ‘worst-case’ rotor, in order to show the potential consequences of poor magnet quality.
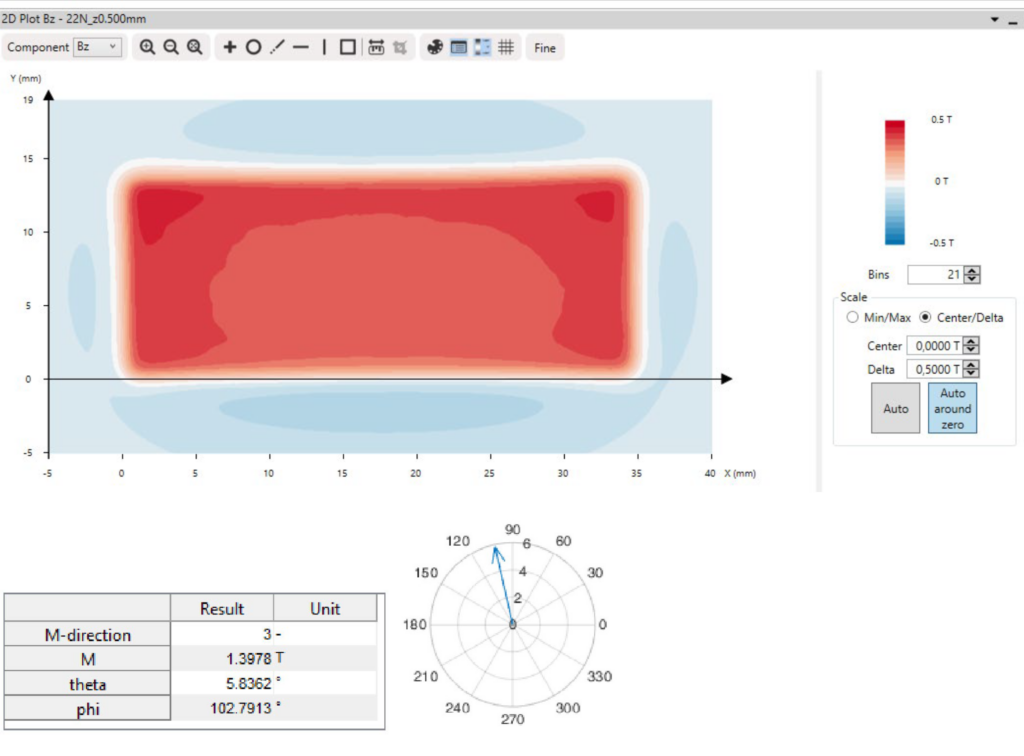
A first pre-selection was done by rejecting all magnets that exhibited a too large magnetization vector angle deviation, leaving only about half the magnets in the running. Next, magnets that exhibited large inhomogeneities within their internal magnetization distribution were also removed, a characteristic that can only be measured using the combination of magnetic field mapping and Magcam’s proprietary analysis algorithms. Within this remaining set of magnets, there still existed a considerable variation in internal magnetization strength, a metric that Magcam’s algorithms can also extract from the external magnetic field distribution. Since the goal was to create high-performing motors, high-strength
magnets with tight tolerances were selected, while at the same time maximizing the homogeneity of magnet quality among the four rotors. This careful selection resulted in 4 sets of high-caliber magnets, one for each rotor. Another set of lesser-quality magnets was picked for the ‘worst-case’ rotor,
exhibiting a large variation in magnet strengths, angle deviations and magnet inhomogeneities, in order to see how such motor would perform on functional motor tests.
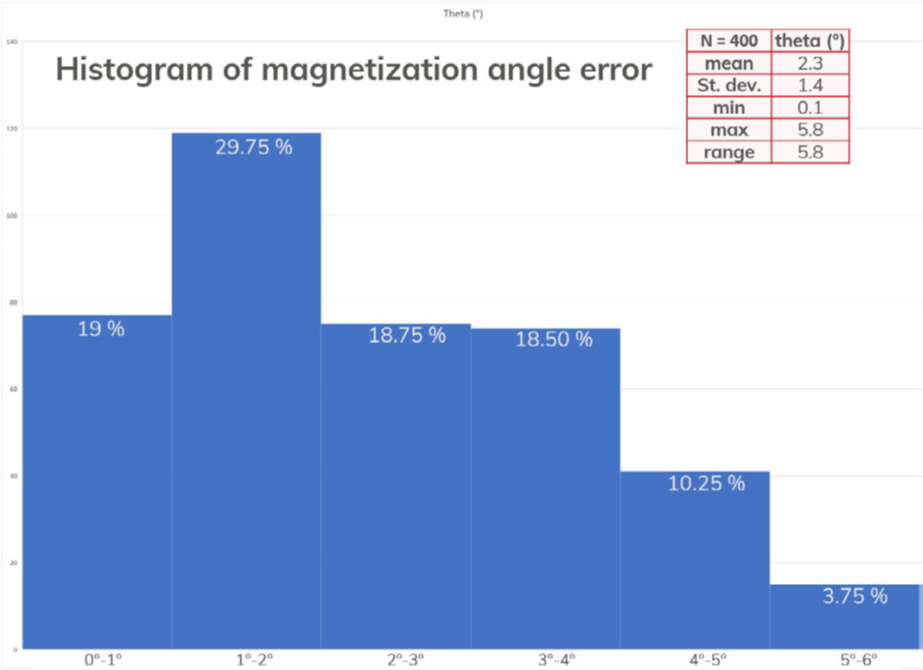
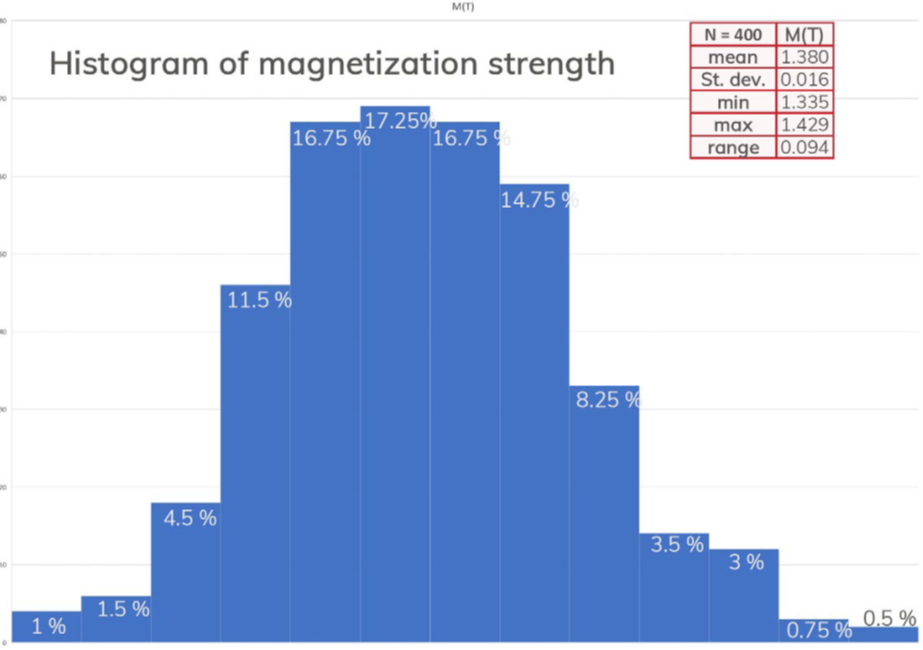
Insights
• The optimized rotors, assembled using the best-selected magnets, demonstrate between 2x and 4x better performance on key magnetic metrics in comparison to the ‘worst-case’ rotor.
• Smaller differences among the optimized rotors are still observed, deemed to be due to assembly tolerances, showing the potential to further perfect the assembly process.
• This comprehensive analysis demonstrates the direct benefits of a two-stage quality control: first, in magnet selection, and second, after rotor assembly.
Functional Motor Tests and Correlation Analysis
Motor Tests by Formula Electric Belgium Team
Armed with the assembled rotors, the Formula Electric Belgium team performed functional tests on the finished motors, focusing on key performance metrics such as torque ripple and cogging torque, which are essential parameters in electric motors used in automotive applications. Their tests resulted in a Fourier analysis of the torque ripple and cogging torque of all five produced motors.
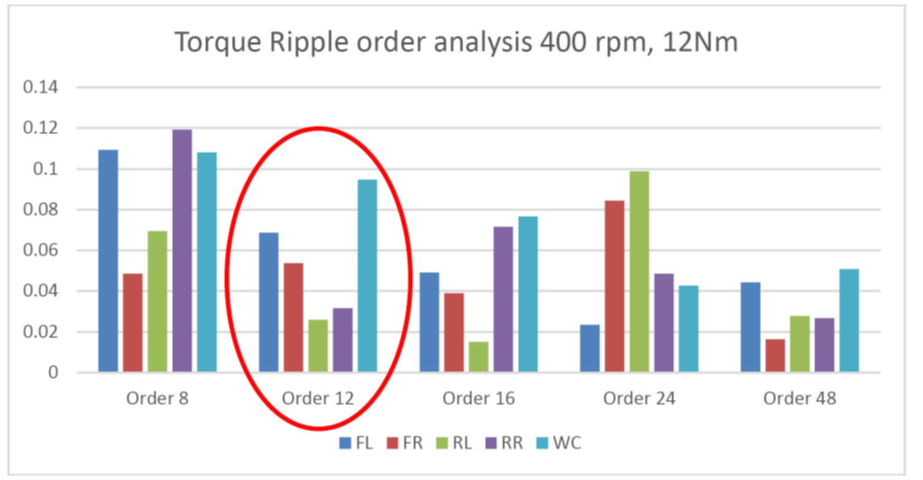
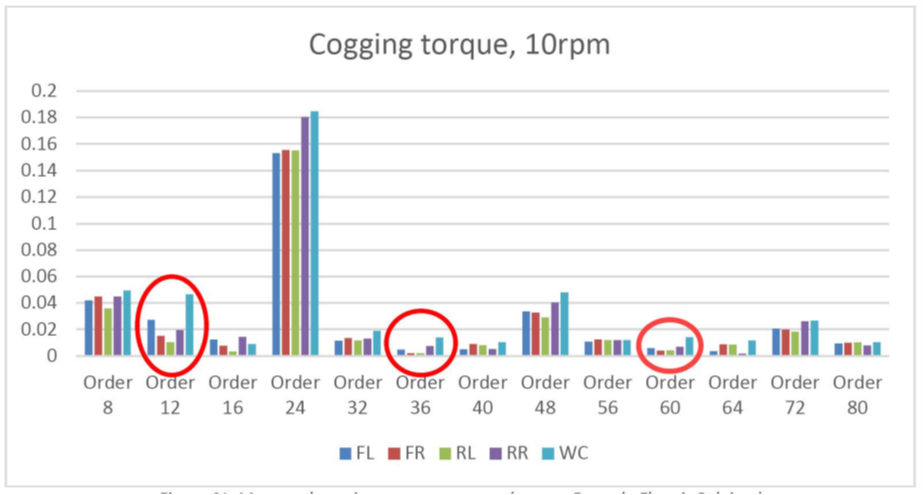
Comparative Analysis & Correlation by Magcam
When looking at the resulting graphs of the rotor-relevant harmonics of the cogging torque and torque ripple of the optimized motors, a familiar picture was observed: the values of the optimized rotors were found to be a factor of 2x to 4x better than those of the worst-case rotor. Moreover, the relative values of these functional metrics perfectly mirrored those of the various magnetic quality parameters obtained from the Magcam rotor measurements.
The powerful conclusion of this comparative analysis: the magnetic quality parameters obtained from Magcam measurements on the rotors correlate perfectly with cogging torque and torque ripple in the final motors. In otherwords: final motor performance can be predicted from the measured magnetic
pole angle deviations, magnetic peak field variations and field gradient variations from a Magcam rotor measurement, without the need for assembling a full motor.
This conclusion opens the door to tremendous cost savings, as bad rotors can be scrapped before motor assembly, thereby saving time and material, by performing a magnetic scan of the bare rotor.
Conclusions
• A clear and direct correlation emerged between motor performance, rotor magnetic field distribution metrics and the quality of magnets utilized.
• Motor manufacturers can optimize motor performance by a factor of 2x up to 4x through individual magnet quality control before rotor assembly.
• Motor characteristics can be predicted from the measured magnetic field distribution of the assembled rotor, before final motor assembly.
Key Take-Aways for the Electric Motor Industry
- Even within a single magnet batch, there can be a vast range of variation. To fabricate top-tier rotors, these variations need to be reduced. Supplier magnet quality screening, pre-assembly measurement and magnet pre-selection lead to significantly better final products.
- Using the Magcam magnetic field camera scanner and MagScope data analysis software, motor engineers can optimize key magnetic rotor parameters, such as pole width variations and field uniformity, leading to 2x to 4x improvements compared to rotors assembled with inferior magnets.
- By strategically selecting high-quality magnets, manufacturers can improve motor attributes like cogging torque and torque ripple by a factor of 2x to 4x.
- By measuring the magnetic field distribution of assembled rotors (even without pre-selected magnets), magnetic rotor parameters can be gauged to assess rotor quality and even predict functional motor characteristics before full motor assembly, thereby saving time and scrap.
- Magcam can assist motor manufacturers and magnet suppliers at every stage of motor development and production by providing top notch magnet inspection equipment, along with expert advise and service.
About the partners
Magcam NV
Magcam is the technology leader in permanent magnet inspection based on its unique magnetic
field camera technology. Magcam’s hardware, software, and services work closely together
to measure, visualize, and analyze full threedimensional magnetic field distributions with high spatial resolution at high speed for in-depth analysis of permanent magnets, permanent magnet rotors,
and other magnet assemblies. Magcam’s complete solution guarantees a better development of high-end applications of permanent magnets, improved incoming and outgoing quality control, and 100% in-line production testing. Magcam’s expert team also offers measurement and analysis services, application consulting services and of course outstanding customer support. www.magcam.com
info@magcam.com
LinkedIn: @magcam
Youtube: @magcam
Fischer Elektromotoren GmbH
Fischer are experts in the development and production of high quality, customer-specific electric motors of different types, offering comprehensive services, from development and design to reliable series production. Their services also includes the professional repair of electric motors, gear motors, servo motors, pumps, fans, electrical appliances and other drive systems.
www.fischer-elektromotoren.de
info@fischer-elektromotoren.de
Formula Electric Belgium
Formula Electric Belgium unites a group of motivated engineering students from different campuses of KU Leuven University and Thomas More University College in Belgium. Each season a new electric race car is designed, built and driven at several events in the international Formula Student competition. The team is supported by partners who help realize the building of the car. For the 2023 season, Magcam and Fischer supported them with the optimization of their electric motors.
www.formulaelectric.be
info@formulaelectric.be