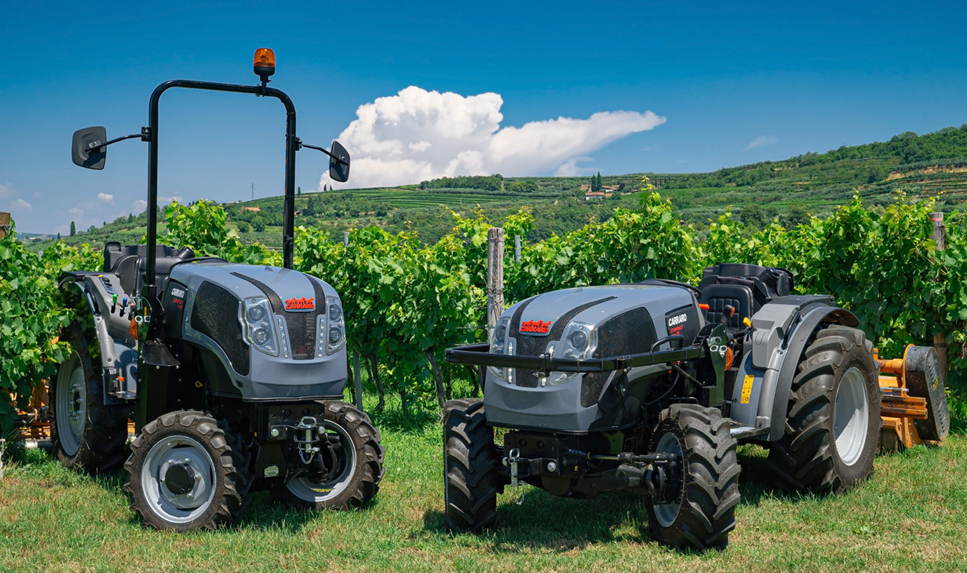
Devoted to thoughtful and innovative engineering, agricultural and construction equipment manufacturer Carraro Group of Italy is bringing advancements in electrified mobility to workfields. It has developed a sophisticated cadre of hybrid and fully electric propulsion systems for powering off-road equipment without compromise compared to traditional internal combustion engine systems. The new machines use permanent-magnet synchronous motors in tandem, or instead.
“Carraro considers vehicle electrification as a significant opportunity to limit emissions without reducing productivity and efficiency,” explains Giacomo Fiocchi, ePower Systems Director of the venerable company. Established 90 years ago in rural Italy as a manufacturer of machinery for seeding agricultural fields, today it makes its own brand of specialized tractors while also providing sophisticated power systems for many of the world’s leading manufacturers of agricultural, construction and material handling equipment.
To support its electrification, transition the company has founded a dedicated division, e-Power Systems, focused on the development of e-mobility variations as well as associated digital and electronic products and services, which integrates and completes the existing product offering. Fiocchi shared with Magnetics Magazine recently his company’s path to product development for the transition, and provided details of the process, using its telescopic handlers as an example.
“The ePower electrification process defines five macro-phases in order to minimize designing and material costs then emphasizing virtual activities,” he notes. “The process starts with three simulation steps: vehicle mission definition, components and architecture identification and performance simulation. Only in the last two phases are real objects realized to complete the components bench tuning and testing and the last step: vehicle testing.”
All data coming from the vehicle are acquired to have a clear definition of all the working cycles and system performances. After this, the simulation tool developed from ePower can create the digital twin where the most important parameters (eg. tractive effort, fuel consumption) are mapped. The real electric process can now start based on the ePower library where all the key components are already built and available for any simulation loop. The library allows ePower engineers to tune all the major parameters in order to obtain different results according to level of customization.
“The telescopic handler is one the most interesting vehicles for the electrification process due to its size and duty cycle,” explains Fiocchi. “It’s also becoming very attractive thanks to the wide range of applications from agriculture to construction equipment.” The ePower engineering team developed hybrid (range extender) and full-electric as two alternatives and both can be used with the P3 or P4 architectures as shown in the accompanying diagrams. If the cost or size of the battery is excessive, the hybrid solution could be a good option. As a second step, when battery costs decrease, a larger battery can be installed in order to have a full electric vehicle. P3 and P4 are two architecture alternatives, identifying where the e-motor is installed; both can exist with the full-electric or hybrid approach.
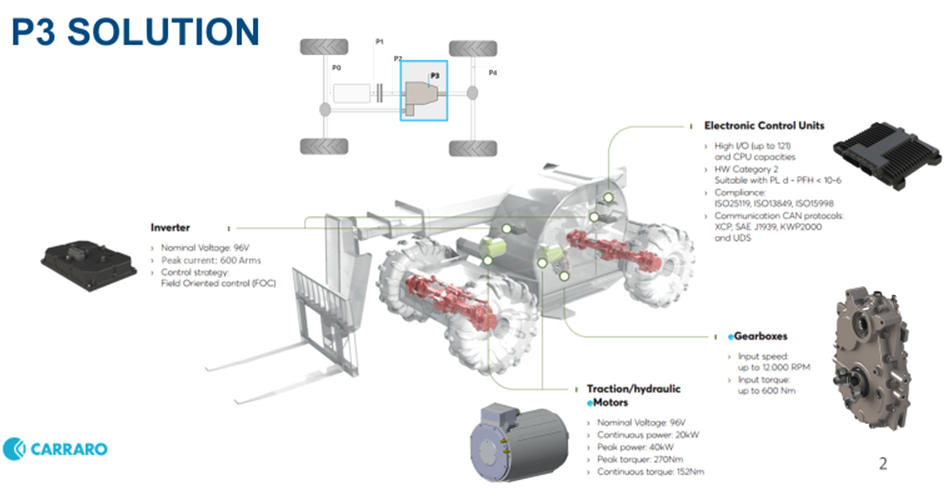
For the hybrid version, the Carraro proposal is based on Hybrid Range Extender where a downsized 18kw combustion engine is used at constant speed (best efficiency point) in order to support an electric generator. The traction mission is achieved by the connection of a 40kw peak power eMotor and a dedicated dropbox (eTB220) able to supply front and rear axle. A 10kwh Lithium battery and an additional eMotor for hydraulics support full electric operations, where the power demand is limited, for at least two hours. The P3 solution is supplied at 96V minimizing safety impacts, cost and complexity. The achievable cost fuel saving is in range of 20-50% and it’s related to three main contributions: the downsize of the original 55kW diesel engine, increased efficiency during all the impulsive transition and full-electric operations The vehicle cost increase for this solution is estimated to 8-10% and it will be compensated along the entire vehicle life with a final total cost of ownership saving of 1-2%. The main advantages are related to the extended vehicle functionalities, notably precise traction control, noiseless operations along full-electric and reduced noise during hybrid and limited maintenance.
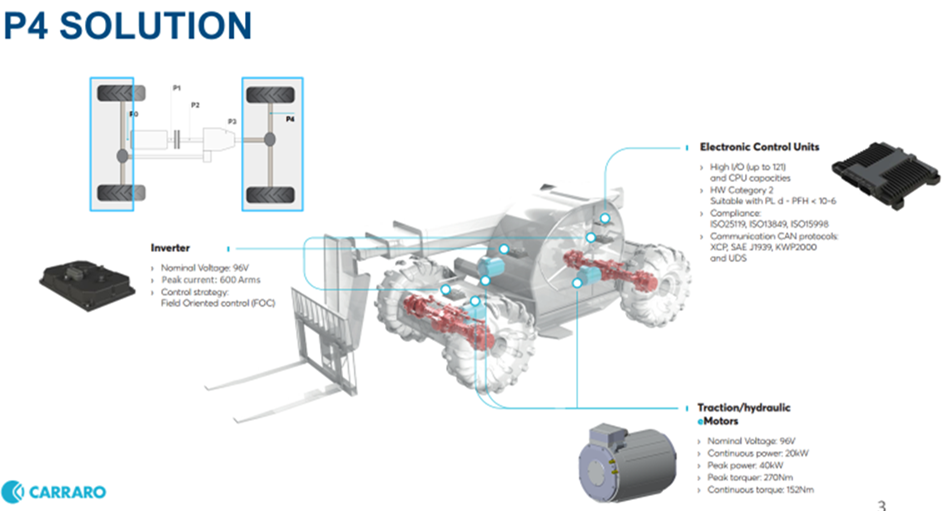
For the full electric version, the proposed solution is a P4 architecture where both the axle are independent and leaded from an integrated 40kW peak electric motor; any dropbox is present into the vehicle with significant advantages in term of layout. An additional electric motor for the hydraulics services is present together with an increased 25kWh Lithium Battery to support the permanent full-electric operations.
The vehicle cost increase for this solution is estimated to 15% and will be compensated along the entire vehicle life, reaching a final TCO saving of 3-6% thanks to the achievable cost fuel saving of 45-50%.
The main advantages are related to the extended vehicle functionalities and include precise traction controls, noiseless operations, limited maintenance and compact layout, in other words able to fit with already existing vehicle platforms.
Overall, its engineers have developed an integrated portfolio of ePower systems and modules to suit various applications. Examples of some are shown below.
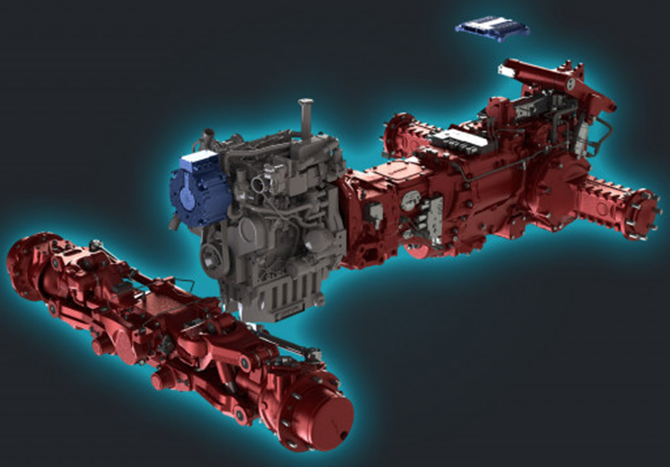
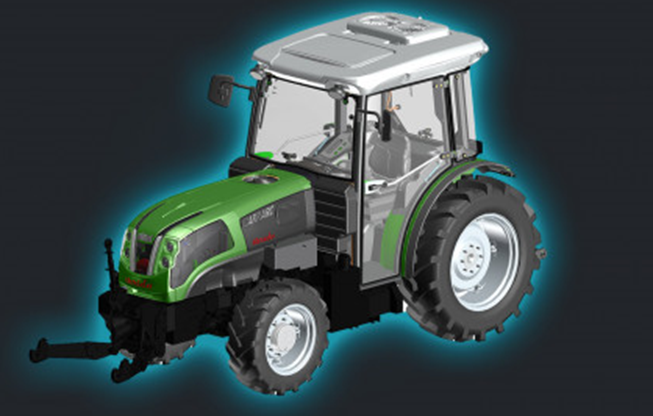
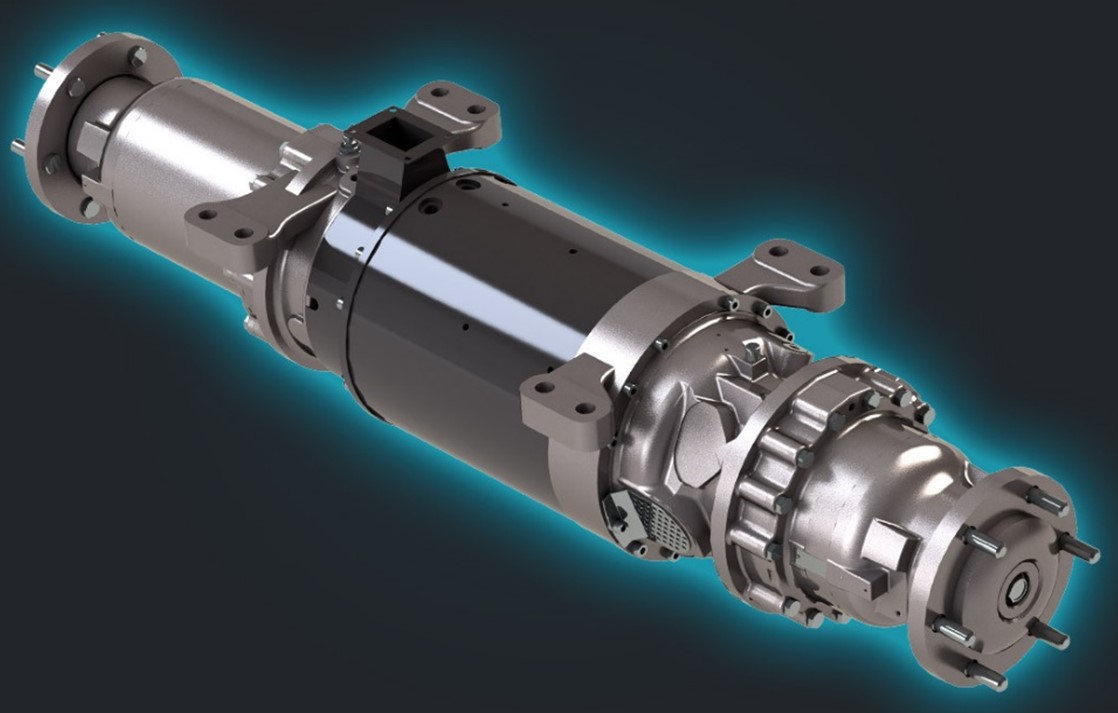
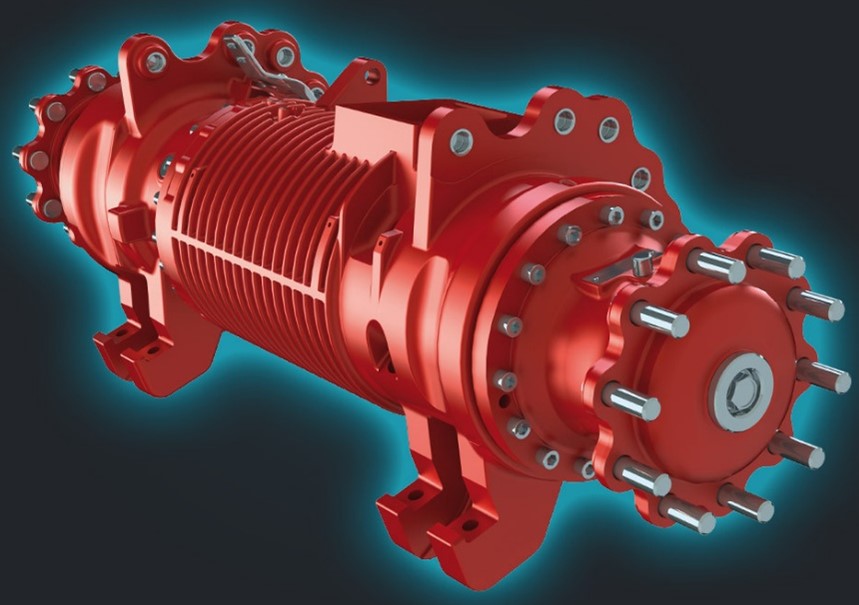
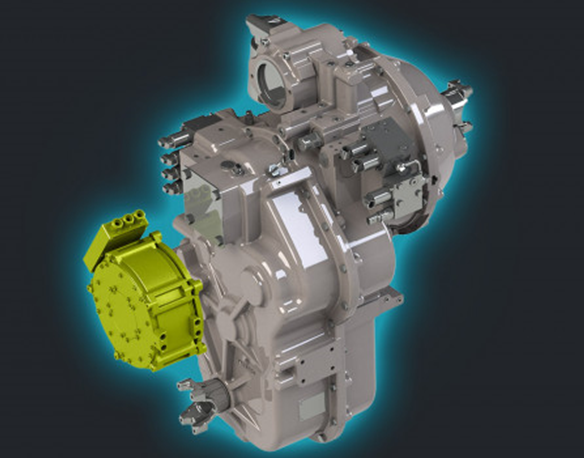
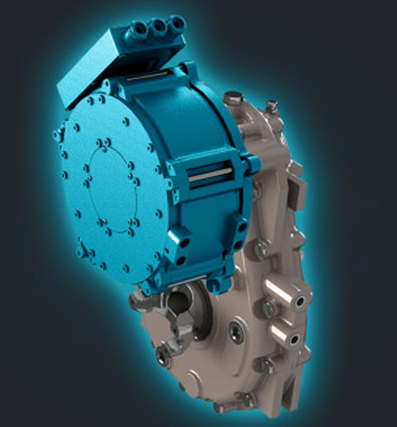
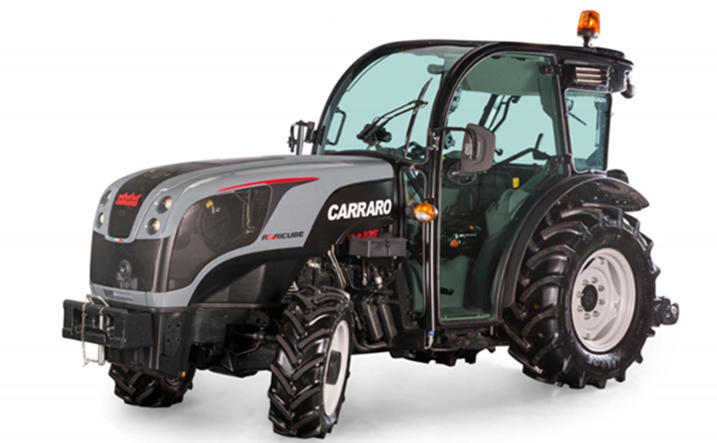
Based in Campodarsego north of Padua, Carraro is particularly well known for its highly efficient power transmission systems. The company’s main market is agriculture, accounting for about half of its output. In addition to its own brand of specialized tractors, it makes gears, transmission systems and special tractors for the world’s primary agricultural machinery manufacturers. Construction equipment accounts for nearly a third of its business, developing transmission systems for backhoe loaders, general loaders, telehandlers, wheeled excavators and compaction rollers. Other areas for its products are forklifts for material handling, automotive and robotic components. One of the company’s hallmarks is that it can manufacture the smallest gear up to complete tractors. For more info, see www.carraro.com.
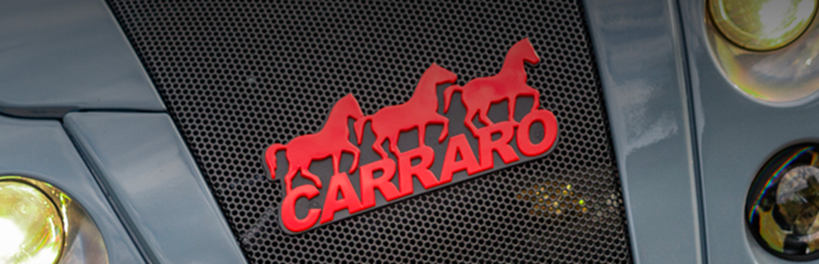