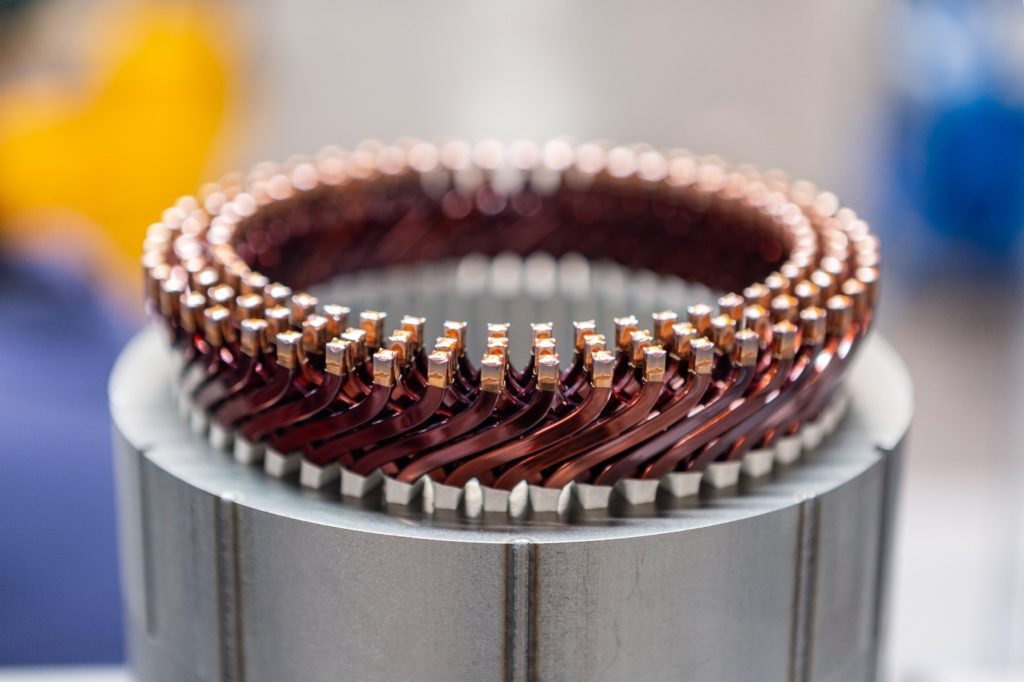
Bosch workers in Charleston, South Carolina at the company’s largest production facility in the USA are learning the intricacies of magnets and hairpin windings as it transitions from a diesel power manufacturing site to electric motor production to meet the new demands of electrification and e-mobility. Production of electric motors began there in October and additional capacity being added is expected to be operational by the end of this year as Bosch expands its long history of mobility-related manufacturing with new electrification products.
“We have grown our electrification business globally and here in the North American region,” said Mike Mansuetti, president of Bosch in North America. “We’ve invested more than $6 billion dollars in electromobility development and in 2021 our global orders for electromobility surpassed $10 billion dollars for the first time. Local production helps to advance our customers’ regional electrification strategies, and further supports the market demand for electrification.”
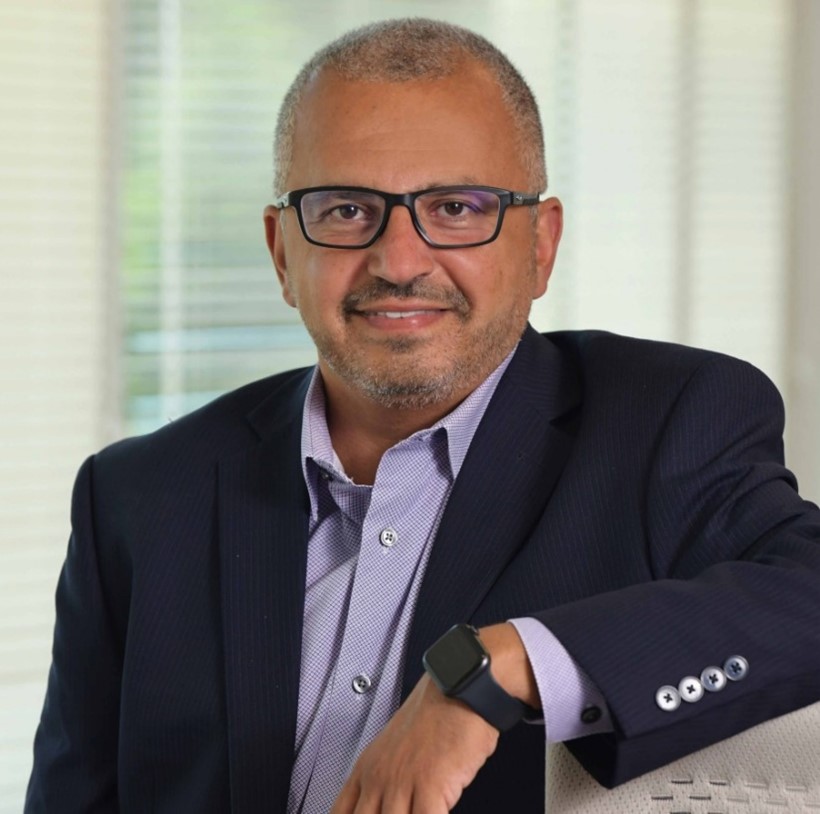
Production of electric motors at the Charleston site began in October 2022, covering about 200,000 square feet in an existing building on the campus. The new assembly area includes the production of rotors and stators, and the final assembly of the electric motor.
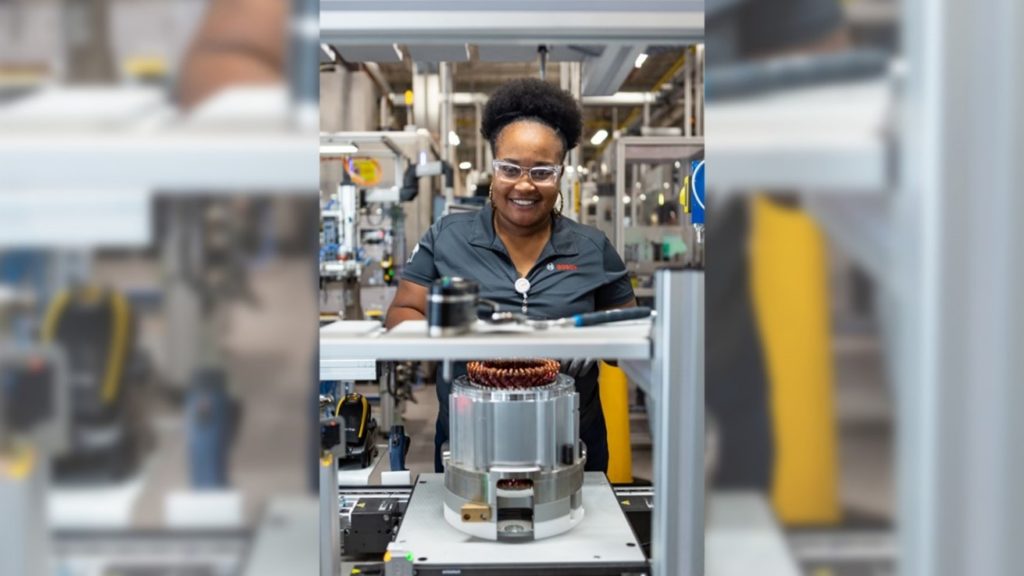
The company has secured additional electromobility business that requires further expansion at the plant. An additional approximately 75,000 square feet will be added onto the existing building to make room for future production. The total investment for the expansion will be more than $260 million for the expansion and new high-tech manufacturing equipment.
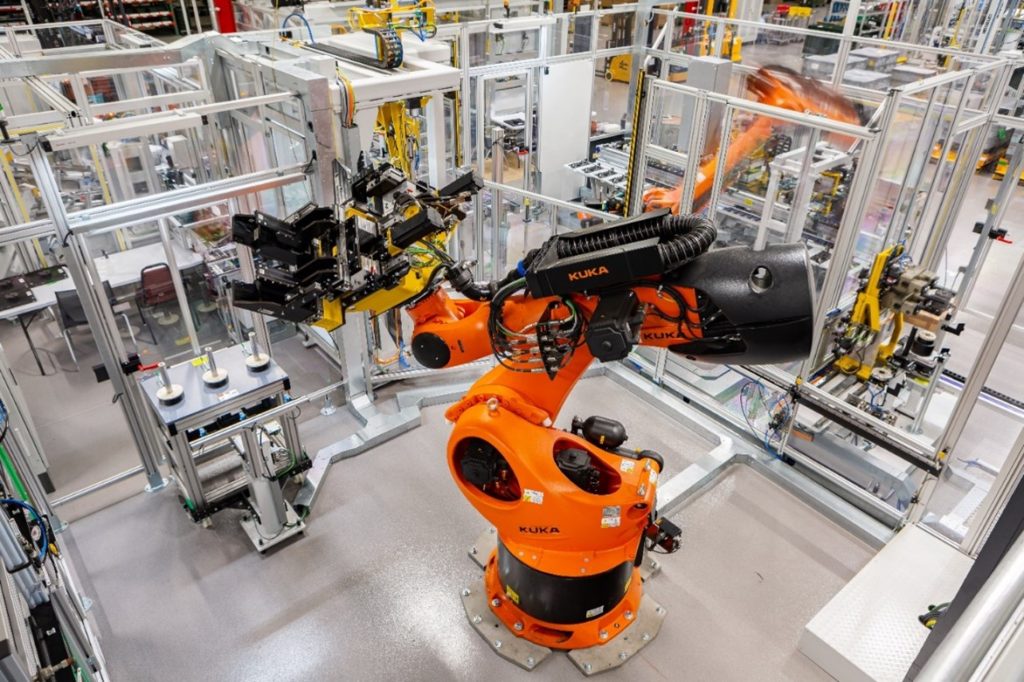
The Charleston plant stands out with a long history of process competency as well as its knowledge in the area of automation and robotics. Production at the site features highly automated processes, and the site utilizes artificial intelligence and Industry 4.0 methods to gain more efficiency.
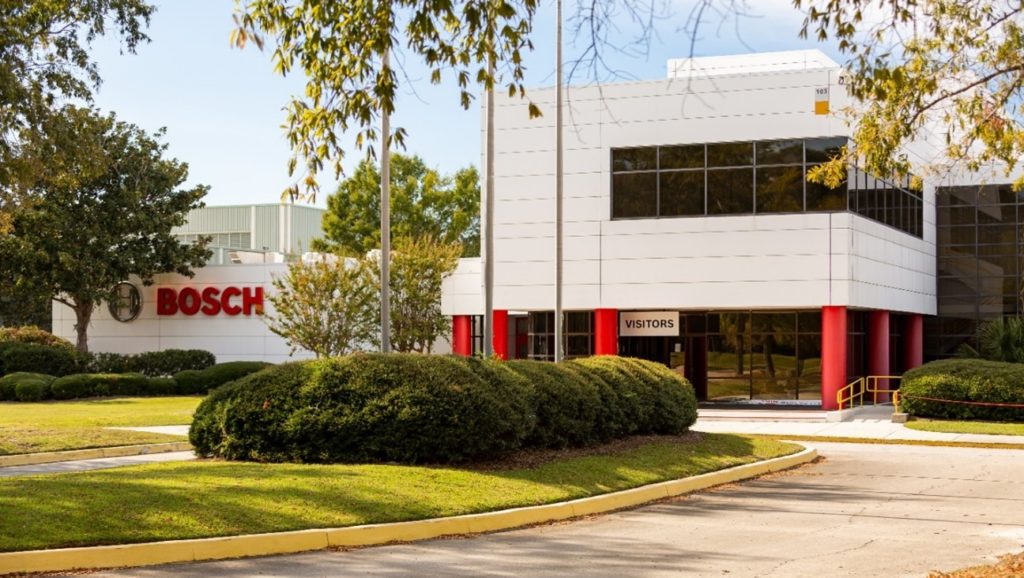
Opened in 1974, it is the largest manufacturing site in the United States for Bosch from an employment perspective with around 1,500 associates. It covers more than 900,000 square feet of floor space located on 118 acres. The site supports multiple products from the Bosch Mobility Solutions portfolio. It also produces high-pressure fuel injectors and pumps for internal combustion engines and also manufactures safety-related products such as electronic stability control to combat skidding.
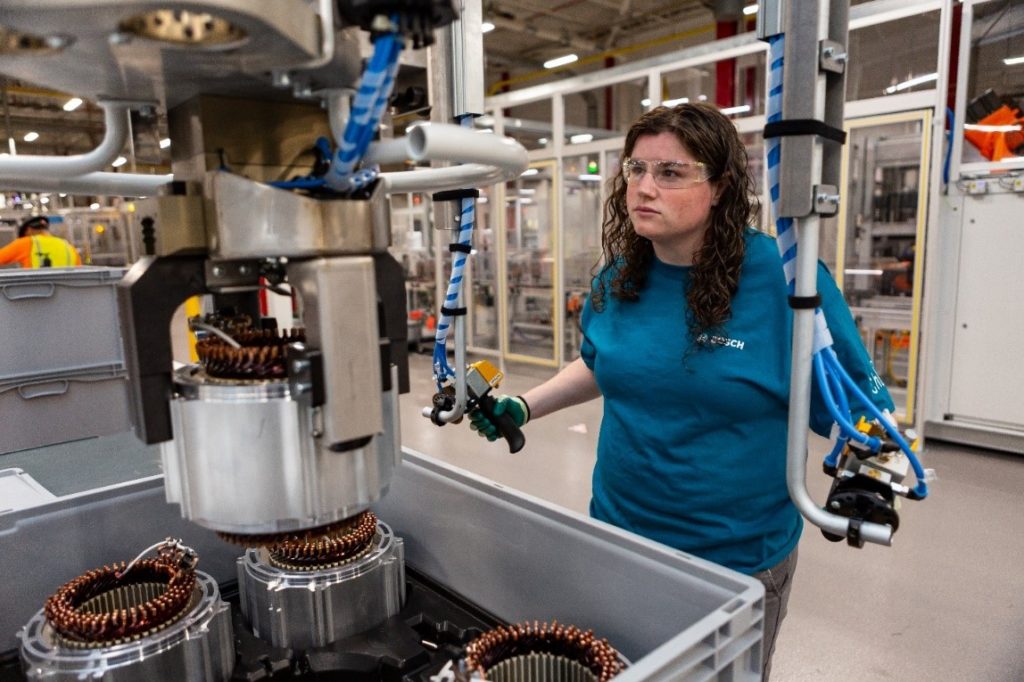
The newly launched production of electric motors is located in a building formerly occupied by production of diesel components. Bosch announced in January 2020 that production of diesel powertrain components would be slowly ramped down in favor of securing electrification business.
“This launch delivers on a commitment to our associates and to the local community in Charleston,” said Mansuetti, who started his Bosch career as a manufacturing engineer at the facility. “We are in the midst of major shifts in mobility, and the story of reinvention in Charleston is a model for how electrification production can evolve from within an existing facility. We are building on the long-standing expertise and commitment of the Charleston team with this new production.”
At the facility Bosch will produce the rotor and stator and the final assembly of electric motors that will drive electric vehicles on the road in the United States. Staff are learning the related fundamentals and the intricacies: A rotor is the rotating part of the motor and contains a precise design of magnets to create a magnetic field. A stator is static and made up of electric coils that are fed energy from alternating current coming from the power electronics via the battery. As current flows into the stator, the magnetic field of the rotor will chase the magnetic field in the stator, creating the motion that is transferred to the wheels of the vehicle.
The Bosch approach to electric motor development is flexible and allows easy integration in different vehicle topologies based on customer needs while still providing competitive costs. The company uses approaches such as bar winding technology to maximize power density while minimizing size, which enables more freedom in the electric motor layout. Thinner lamination tailored to customer needs provides greater efficiency. As electric motors continue to develop, Bosch is enlisting the help of artificial intelligence and new design methods to continue to optimize development, efficiency, performance and use of materials.
Electric motors from Bosch can deliver anywhere from 50 kilowatts to up to 500 kilowatts with torque ranging from 150 Nm to 1000 Nm. They feature up to 98 percent efficiency, which helps to maximize range of the vehicle. With a voltage range up to 850V, Bosch has developed electric motors suited for a variety of applications from passenger cars to light commercial vehicle use.
“We have long been believers in the potential of electromobility and we have been investing heavily to bring this technology to market at scale for our customers,” Mansuetti said.