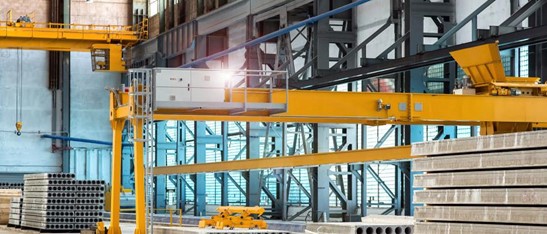
Few companies put magnetic sensing to work as much as sensor and automation specialist Balluff, a global provider of diverse solutions for industrial and machinery environments. Many such as its new Long Distance Positioning System (LDPS), inductive couplers and encoders harness magnetic field strength to get the job done — but the company also creates sensor products that, instead, overcome magnetic effects.
Magnetorestrictive position sensing is the core technology in the LDPS, which can provide reliable, intelligent and adaptable position measurement over several hundred meters in harsh environments with a repeat accuracy of 0.5 mm. This makes the system ideally suited for applications on overhead traveling cranes, loading bridges, gantry cranes, reversing controls, and for crane and trolley travel, which turns process cranes into large-scale robots.
The system consists of a magnetostrictive position measuring system with a Profinet interface and several position encoders installed along the travel path of a crane, whose position is read by the magnetostrictive sensor mounted on the crane. This information is transmitted to the controller, which calculates the absolute coordinates of the crane position with high accuracy. It automatically adapts to the magnetic markings and can be equipped with a fail-safe operation option with redundant markings along the travel path.
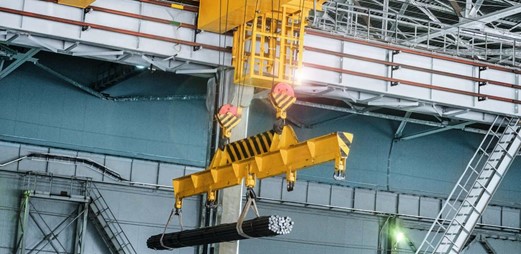
Crane systems are used worldwide and across industries for transporting goods in intralogistics, in warehouse management or in various production processes. The loads here are often very high and the environment also places enormous demands on the sensor technology. In addition, the operator must always be aware of the absolute position of the crane or the control system.
This applies particularly if there are two or more cranes on one runway. For correct positioning and to avoid collisions of cranes, laser sensors are usually used, which meet common performance requirements under normal ambient conditions. However, if the level of contamination in a hall is high or if the cranes are operated outdoors, laser-based systems reach their limits.
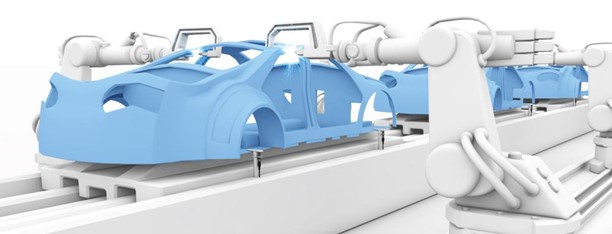
Inductive Factor 1 sensors detect any metal with the same switching distance
While Balluff employs many sensing principles in its products depending on the application, its magnetic sensor technologies include inductive sensors, magnetic field sensors, magnetorestrictive linear position sensors, magnetic linear and rotary encoders. In some cases, however, the application calls for non-magnetic sensing as represented by its recently introduced Inductive Factor 1 magnetic field immune sensors.
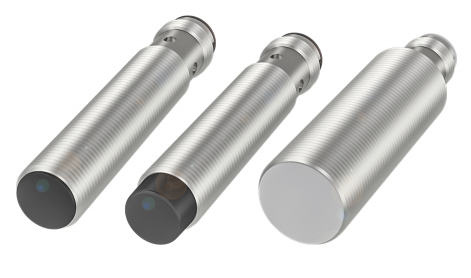
Factor 1 sensors
Factor 1 sensors detect any metal including steel, aluminum or brass with the identical switching distance, an important feature for detecting objects of varied materials in an application. In addition to the Factor 1 properties, the sensors feature an extended temperature range and are magnetic field immune. This ensures a fault-free process, even in the presence of strong electromagnetic fields and harsh environments including near induction hardening or welding equipment.
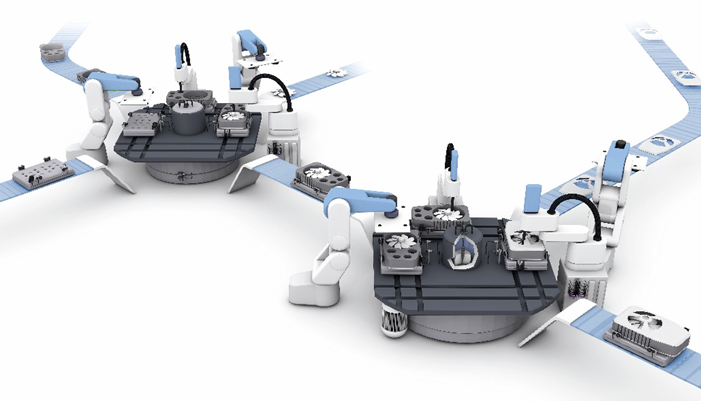
Inductive coupling when lots of power is transmitted
Inductive coupling systems are always used when a particularly large amount of power is transmitted such as in robotics applications involving controlling gripper arms. “Inductive couplers are indispensable in many different applications today,” says Dr. Laszlo Herczeg, product manager.
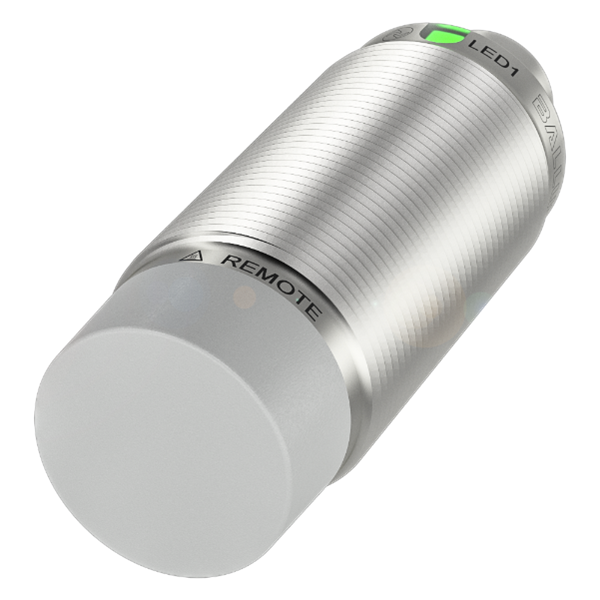
New inductive coupler from Balluff
The company’s new BIC M30 inductive couplers for non-contact power transmission are particularly suitable for production lines where flexibility is required for non-contact power transmission, fast data transfer and condition monitoring. They can transmit up to 1.5 amps of continuous output, transmitting the energy without contact. The IO-Link interface of the inductive couplers enables a frictionless, transparent and fast exchange of data between the IO-Link device and the IO-Link network module. “A unique feature is the second IO-Link channel, which can be used for process and diagnostic data and thus for condition monitoring,” explains Herczeg.
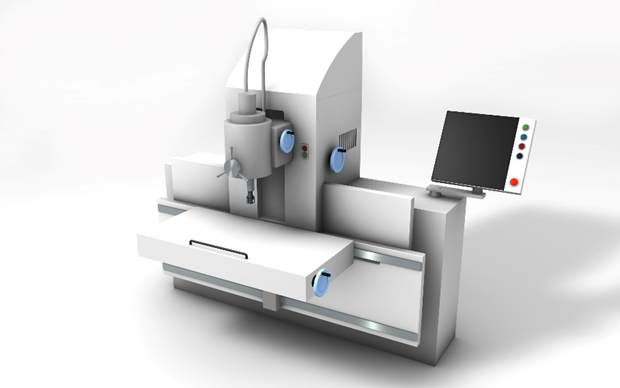
Rotary encoders from Balluff monitor rotary axes that control the precise positioning of workpieces and the movement of machines and systems
Magnetic encoders are typically the choice for harsh environmental conditions as demonstrated by Balluff’s new incremental and absolute encoders designed for difficult environments and high shaft loads for precisely measuring lengths, positions, speeds, rotational movements and angles. In industrial applications, process cycles are precisely timed, making essential the control of rotational and conveyor speeds as well as the exact positioning of workpieces.
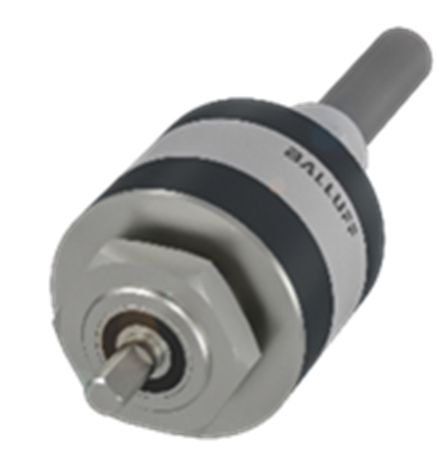
One of Balluff’s new magnetic absolute encoders for machine control
“The encoders monitor rotary axes that control the precise positioning of workpieces and the movement of machines and systems,” explains Josef Albano, product manager. Rotary encoders convert mechanical movements into digital electrical signals. Depending on the application, they have different measuring principles. If a high resolution is required, optical encoders that measure incrementally are usually used. “With incremental displacement measurement, each movement is measured by the positive or negative increase in the distance traveled,” says Albano. The incremental encoders measure angles with the highest resolution. Among other things, encoders are available especially for applications with a high shaft load, suitable up to 500 Newton.
The absolute encoders ensure high-precision positioning of critical machine parts. “With absolute travel measurement, the position is specified as an absolute value. This means that the machine is ready for operation immediately after restarting and does not require a reference run,” explains Albano. The absolute encoders are particularly reliable; their data cannot be lost even in the event of a power failure. Rotary encoders are used everywhere: in automation technology, machine tools or food processing, The new variants complement Balluff’s extensive automation portfolio.
Currently celebrating its founding 100 years ago, Balluff is based in Neuhausen, Germany near Stuttgart. It operates 8 production sites and 38 subsidiaries worldwide, employing about 3,600 people.