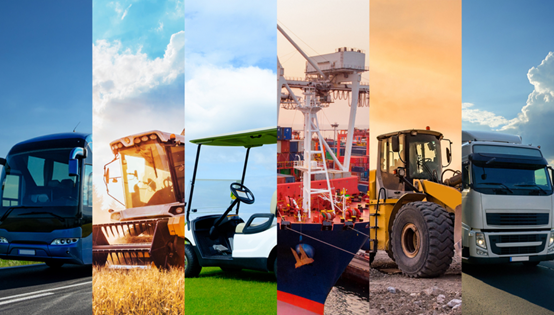
Global trends in increased electrification are creating new challenges and opportunities for companies involved in magnetics. In our ongoing reporting of how they are adapting, REO AG stands out for thoughtfully addressing the evolution, especially related to e-mobility and medical devices. A manufacturer of electrical components and test benches, REO is a fourth-generation family held company based in Sollingen, Germany with about 400 employees and 11 sites globally.
“Electricity is what makes REO’s heart beat. We believe it is the future of mobility,” the company says. With the ongoing move towards electrification, it has bundled together and considered in a logical manner its strengths in the production of inductive, resistive and electronic components. While many providers are forced to purchase technologies, REO can revert to more than 95 years of experience and in-house capability. Recent comments by some of its managers and executives help articulate the view.
“Electric motors are extremely efficient when compared to conventional motor types like the combustion engine”, explains Sven Reimann, management board member and head of development. “At the same time, e-motors benefit from energy recovery during braking, low noise level, simple design and do not cause any local emissions. With REO’s components, we are able to make our contribution to improving e-motors and making them more efficient.”
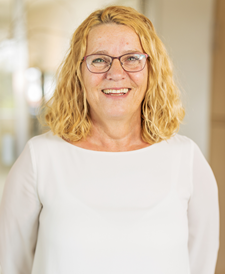
“We had already recognised at an early stage the change in social awareness and resulting potential in the field of e-mobility,” notes Jasminka Usein, board member. “As a result, the research and development work activities we have undertaken previously are now paying dividends. We offer a unique product portfolio globally with our intelligent and smart test systems that can be used in almost any area of e-mobility.”
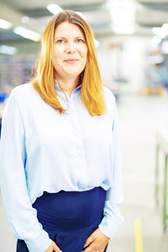
“We recognized a change in social awareness, and the resulting industrial potential in the field of electromobility, at an early stage. We now offer a globally unique product portfolio, containing intelligent and smart components for almost every industry,” explains Jennifer Baatz, manager of the company’s Kyritz branch. Commenting on the firm’s new electromobility website, she adds: “Our mission now is to communicate this and to secure a leading position in the competitive environment.” The site positions REO AG as a holistic partner in the development, production, testing and maintenance of electromobility solutions. The focus is on components for the electrification of power trains and electric engine peripherals, components for charging stations, wall charging stations and wall boxes, and test technology.
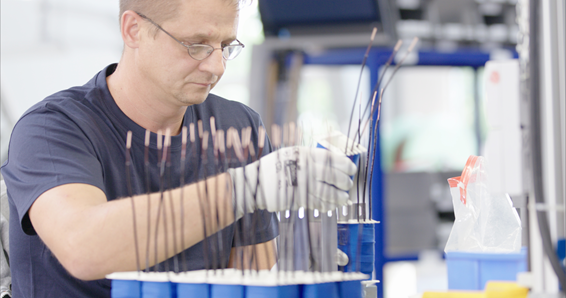
In the field of medical technology, transformers, filters, chokes and current transformers from REO are critical components for transforming and controlling electricity while protecting equipment and patients. Vertical integration of the complete production process is a hallmark for the company.
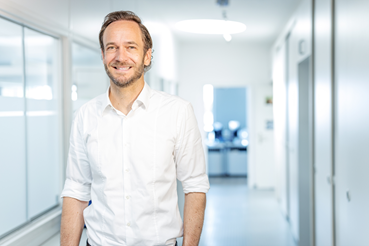
“We worked out at an early stage that high levels of globalization combined with the transfer of production to countries located far away posed particular risks to sensitive medical technology components, explains Philip Twellsieck, chairman of the management board of REO. As a result, excellent medical device quality is achieved due to the holistic production methods employed in REO’s German plants. All of the skills required are pooled together within the company to safeguard production and deliveries.
“All of our medical devices have been designed to ensure the maximum level of safety”, notes Wolfgang Senninger, head of the REO Medical and Current Transformer Division. “This not only protects patients, it also ensures the safety of the doctors and medical personnel administering care.”
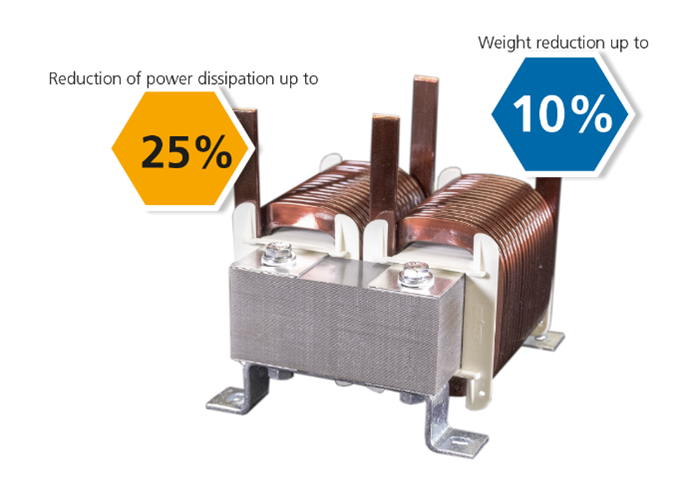
Energy efficiency is a key factor in the company’s designs. For example, by using edge winding in some of its products REO is able to achieve efficient cooling due to single-layer design. Due to the better cooling, an aluminium conductor can be used as a replacement for copper conductors, depending on the design. Skin and proximity losses are reduced, important for the use of silicon carbide and gallium nitride-based semiconductors. Due to the lower winding capacity, the high edge winding is also suitable for higher frequencies. Virtually no insulation material is required, thus increasing service life.
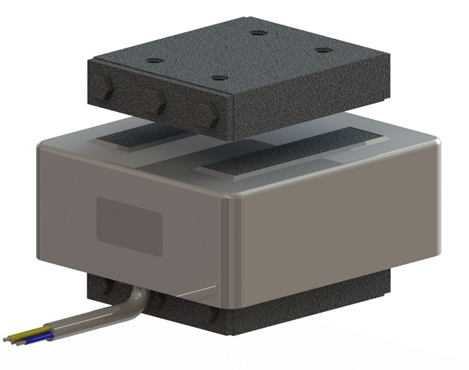
The company’s concepts are applied to other markets, too, such as train magnetics and making vibratory feeding controllers for the pharmaceutical and food industries. Within this specialty, it makes electromagnets in a standard product range from 5 VA to 4000 VA, as well as customer-specific solutions. Shown is an electromagnet recently introduced, the WI 721, which reaches the highest level of corrosion protection through powder coating. This new method completely coats the core, it can be used in high humidity applications as well as wash down and direct water jet applications. FDA approved, it helps feeders run more efficiently and reduce current consumption.
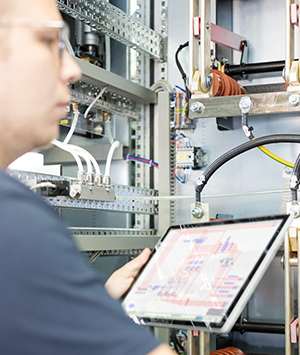
REO offers a broad portfolio of products for test benches used for electronic components. The transformer series are available in a bandwidth up to 150 kHz, achieving a high level of reliability thanks to the testing carried out in advance and completed in the manufacturing process whether vacuum encapsulation, partial discharge measurement or high voltage testing.
For more info, see www.reo.de and www.emobility.reo.de.