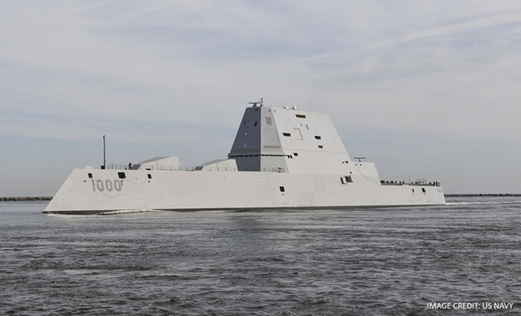
GE Power Conversion is providing Integrated electric power and propulsion systems to navies around the world. Recent projects include the US Navy’s first full-electric power and propulsion ship, the USS Zumwalt, shown above. Two other projects involve new patrol ships for the Royal Canadian Navy and a new combat support ship for the Royal Netherlands Navy.
For the USS Zumwalt, GE’s Power Conversion business was the designer and provider for the high-voltage system, propulsion drive trains consisting of multiphase converters and Advanced Induction Motors (AIM) for the DDG 1000 class of futuristic destroyers.
“Delivery is an important milestone for the Navy, as the DDG 1000 continues more advanced at-sea testing of the Zumwalt Combat System,” said Capt. Kevin Smith, DDG 1000 program manager for the Navy. “The combat test team, consisting of the DDG 1000 sailors, Raytheon engineers, and Navy field activity teams, have worked diligently to get USS Zumwalt ready for more complex, multi-mission at-sea testing.”
For navies around the globe, power and energy are mission enablers, according to Kevin Byrne, who leads the North American marine segment for GE’s Power Conversion business. “Because electric power is needed for various operations and mission systems in parallel, this full-electric power and propulsion ship has the flexibility to direct energy where it is needed on the platform,” he said.
The electric propulsion solution delivers efficiency, cost-of-ownership reductions, and system redundancy for enhanced vessel safety. In addition, machinery layout is more flexible and configurable for containment and isolation, says the company. Employing the innovative Integrated Power System, the DDG 1000 has the capacity to distribute electricity across the entire ship, allowing for enhanced power flexibility for various operational requirements.
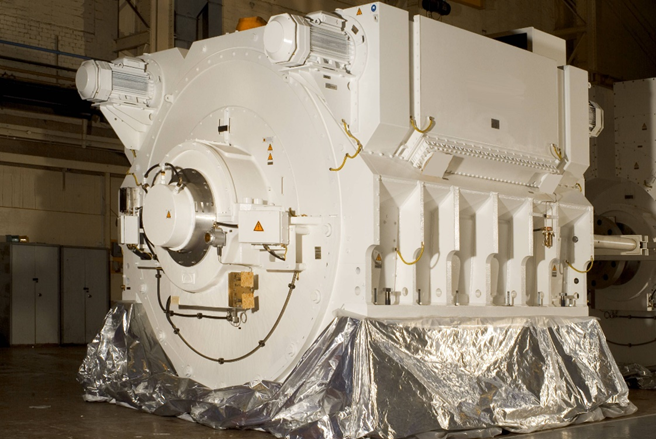
Both of GE’s drive trains have two electric motors in tandem. VDM25000 power converters with three independent channels accompany the 15-phase AIM. Each motor drive train can operate on 5, 10, or 15 phases. This provides high redundancy and is more economical when running at lower power.
Compact enough for combatant ships and powerful enough for an aircraft carrier, AIM technology has demonstrated its performance over more than two decades on land and at sea for mechanical strength, robustness, very low maintenance, and naval performance requirements. For the full-electric propulsion system, GE leveraged its proven technologies, building from the Naval Surface Warfare Center (NSWC) land-based test site and its own Marine Power Test Facility in the UK, alongside the UK Royal Navy Type 45 program, Byrne explained. “The US Navy gets benefits from our other platforms that we then could apply to the DDG 1000 and future platforms.”
With 72 MW of propulsion power, GE’s Integrated Full Electric Propulsion (IFEP) system comprises all shipboard electrical power generation and propulsion including the propulsion motor, VDM25000 variable speed drives, switchboards, and HV equipment. Offering improved efficiency, the electric drive eliminates the need for the drive shaft and reduction gears and brings benefits in acoustic signature reduction, an increase in available power for operational requirements and improvements in the quality of life for crew. The all-electric propulsion of Zumwalt also generates additional reserved power, allowing the integration of future high-energy defense systems and sensors.
Recognizing that navies were demanding more energy amidst space constraints, GE has been developing its full-electric propulsion system for decades, Byrne said. With more than 100 electric and hybrid references with 15 navies globally, it is the top electric propulsion provider to navies around the world.
Arctic & offshore patrol ships for Royal Canadian Navy
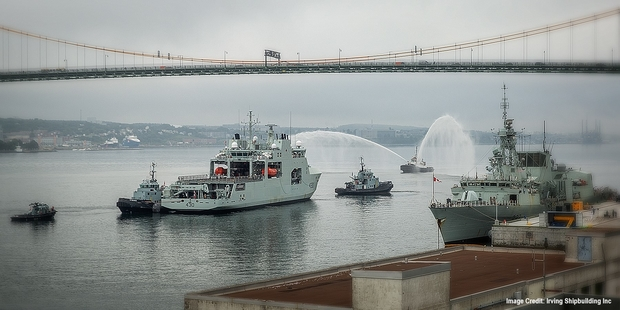
Another recent delivery has been the Royal Canadian Navy’s HMCS Harry DeWolf, its first full-electric power and propulsion ice class patrol vessel with combat package. GE’s Power Conversion business was the designer and provider of the high-voltage electric power system (HV) and electric propulsion drive trains, with specialist capability for operations in multi-year ice, for the Arctic Offshore Patrol Ships (AOPS) class of six vessels.
GE leveraged proven technologies to deliver a low risk, robust full-electric propulsion system which is ideally suited to long range operations above the Arctic Circle, it said. The Integrated Full Electrical Power and Propulsion System (IFEP) includes the induction propulsion motors, variable frequency drive converters for propulsion and bow thrusters, engine generators, medium voltage switchboards, distribution and propulsion transformers, bow thruster motor, commissioning, and sea trials support.
“GE Power Conversion’s dedicated AOPS team developed a close working relationship with the customer, Irving Shipbuilding Inc., maintaining an open line of communication that was instrumental in meeting this key milestone for the Royal Canadian Navy.”, said Ron Krivan, AOPS Program Manager for GE Power Conversion. “Our team will carry the same dynamics with Irving Shipbuilding moving forward in support of construction of AOPS 7 and 8 for the Canadian Coast Guard.”
For the full-electric propulsion system, GE leveraged its proven technologies, building on recent experience in providing power and propulsion solutions for naval ice class vessels for South Africa and Chile, as well as other commercial vessels.
The drive train for each of the two propulsion shafts includes GE’s MV7000 variable frequency drive which is used in many vessel types around the world as well as in numerous industrial applications. Each shaft is directly powered by a slow speed induction motor with optimized design for ice operations, including an ability to deliver high intermittent over-torque at zero and low RPM should the propellers encounter heavy ice loads. This feature makes the AOPS propulsion solution highly suitable for a variety of other ice class vessels that could operate in the Arctic and Antarctic.
With 9MW of installed nominal power propulsion power, the IFEP system comprises all shipboard electrical power generation and propulsion. Offering high over-torque, the electric propulsion system eliminates the need for propulsion reduction gears, an important factor for ships operating in heavy, multi-year ice conditions.
Royal Netherlands Navy new combat support ship
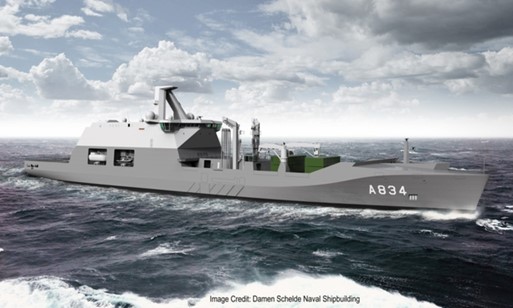
In September, GE’s Power Conversion business reported that it has signed a contract with Damen Schelde Naval Shipbuilding to deliver an energy management and electric propulsion package intended for a new combat support ship, depicted above, for the Royal Netherlands Navy.
According to GE, its technology was selected for its low noise signature, high level of reliability and commonality with the Joint Support Ship (HNLMS Karel Doorman). One of the customer’s key concerns is underwater radiated noise, meaning strict noise and vibration levels are imposed on the propulsion systems. Pulse Width Modulation voltage source inverters feed robust, high-torque density induction motors, allowing high-performance through the modern and optimized propulsion system. Delivery of the vessel is planned for June 2024.
For more info, see www.gepowerconversion.com.