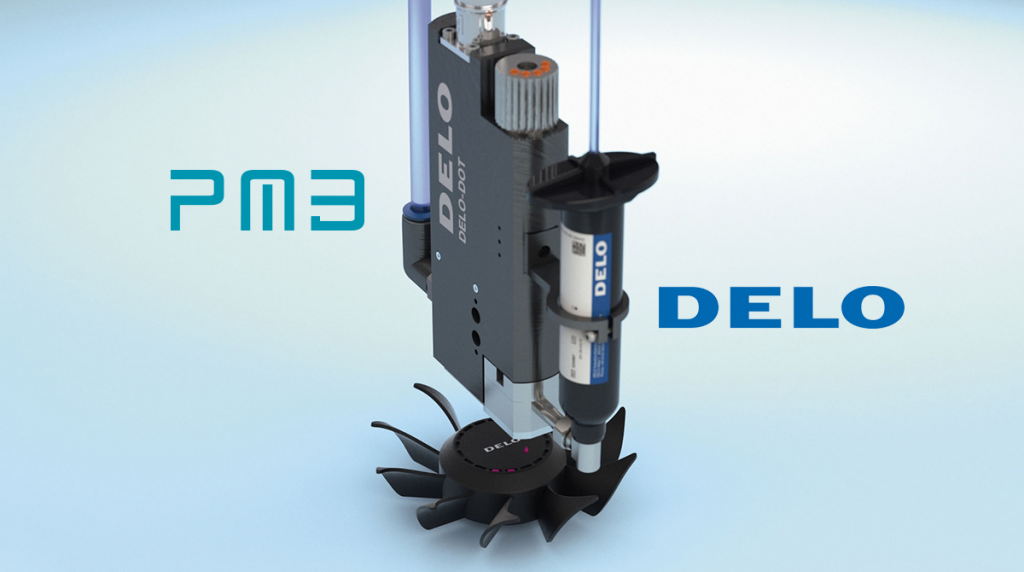
DELO, a manufacturer of industrial adhesives for automotive, consumer and industrial electronics applications, has collaborated with the German-based mechanical engineering company Praezisionsmaschinenbau Bobertag (PMB), to create a new additive balancing technology for rotating parts in electric motors, fans, pumps and turbines. This high-precision process helps bring parts used in electromechanical components and electric machines into balance without having to remove any material from the product.
To achieve maximum accuracy in industrial serial processing, PMB uses a balancing compound from DELO to correct any unbalances identified in a highly accurate measurement. The material, which is dispensed quickly and precisely in minimum quantities, is cured within seconds, reducing noises and increasing the lifetime of a product.
With minimum possible correction accuracies of 0.1 mg, residual unbalances of 1 mg*mm, as found in the optical industry, can be achieved. The excellent reliability also makes this process ideal for medium unbalances of 50 to 100 mg*mm, that can be found in small fans.
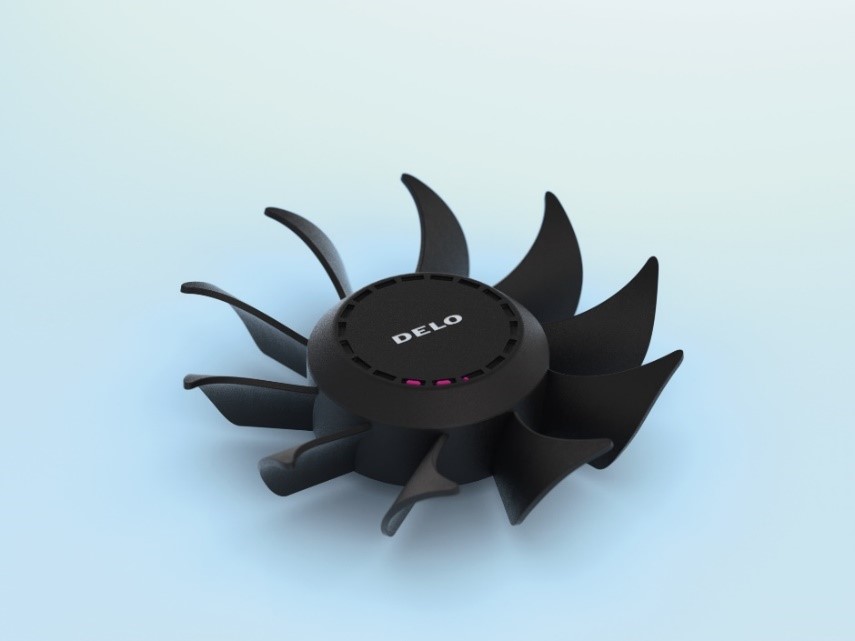
During the production process, a measurement station in the PMB balancing machine determines if there is an unbalance in the item being measured. Once an unbalance has been identified, DELO’s DELO-DOT D4 microdispensing valve quickly and precisely applies its high density, specially modified, light-cure balancing material in one or two planes without contacting the workpiece.
Irradiation with the company’s Delolux UV lamps cure the balancing material completely within a few seconds. A control measurement verifies the result. Performed directly in the measurement station, balancing is usually completed following one correction step. If short cycle times are to be achieved for large-scale production, the process steps can be performed simultaneously on multi-station systems.
“This new development is available as a standard solution which is easy to implement and is scalable from small batch to large-scale production,” explains Manfred Bobertag, managing director of PMB. “In comparison to existing processes, this new approach offers users fast cycle times, freedom from chips and perfectly controllable unbalance correction.”
“This is one more example showing that adhesives can do much more than just permanently connect components to each other,” says Karl Bitzer, head of product management at DELO. “In fact, our products are multifunctional materials that are tailored to enable entirely new applications and intelligent processes.”
Up to now, subtractive processes such as machining, and increasingly, lasering have been the dominant balancing processes. In comparison to additive processes, subtractive processes require components to be designed with additional ‘sacrificial material’ that can be partially removed. Additive balancing is more material-efficient, say the developers, because the exact amount of material required is applied to the workpiece, bringing it into balance.
Balancing is required for most applications involving rotating components. An improved unbalance enhances quality by reducing vibrations and loads. It enables higher rotational speeds, lower noise volumes and longer lifetime.
For more info, see www.delo-adhesives.com and www.pmb-bobertag.de.