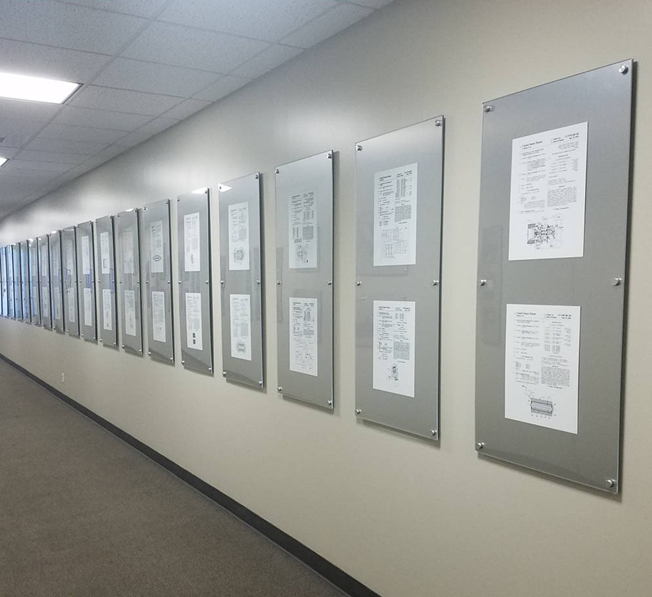
Upwing Energy, inventor of a sophisticated magnetic drive system for downhole pumps for the oil and gas industry, has been issued 10 new patents for its artificial lift technologies. The patents cover design features in its downhole rotating tools and its methods to increase hydrocarbon production. Now the company’s innovative technology is being further developed and tested in the Deepstar project, a multicompany effort to pioneer new methods for subsea exploration and production in deeper waters.
Upwing is an offshoot of parent company Calnetix Technologies, a developer and manufacturer of high-speed rotating systems for a variety of industries. The new inventions include Upwing’s Subsurface Compressor System (SCS) and Magnetic Drive System (MDS), positioned as a reliable and retrievable drive system for downhole pumps.
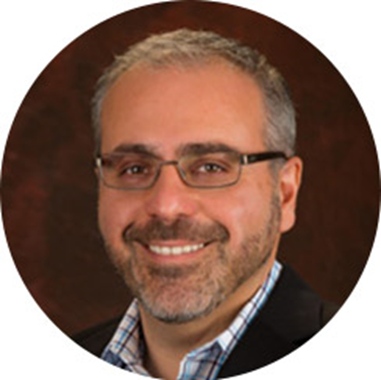
“The newly issued patents are an important part of our intellectual property portfolio and validate our team’s advanced engineering design proficiency and deep knowledge of downhole rotating technologies,” said Herman Artinian, president and CEO of Upwing. “The issuance of these patents will pave the way for the commercialization of our disruptive downhole artificial lift technologies.”
Eight of the new patents protect aspects of the company’s downhole technologies including high-speed motor drives, seal-less downhole systems, thrust load support systems, active magnetic controls, magnetic couplings and electric machine isolation, which underpin key elements of the SCS and MDS downhole artificial lift systems.
One covers its development of a small, highly reliable velocity sensor system that can be used to measure vibration within a rotating downhole tool. Developed for use with its passive magnetic bearings, the unique sensor offers direct measurement of pump dynamics and can be placed anywhere in the tool, including the pump stages.
Another covers the company’s downhole blower system that utilizes a highly efficient passive magnetic bearing system, providing an unsealed lubrication-free bearing system for increased reliability and operating life. The other patent covers an advanced, high-efficiency electric motor configuration suited for flooded operation and applicable for downhole electrical submersible pump systems.
Upwing has exclusively licensed core technology patents from Calnetix and has filed its own system-level and application-related patents for downhole rotating devices. Upwing now holds 23 U.S. patents and has filed 47 U.S. and 28 foreign patent applications to date. Its headquarters, engineering and manufacturing facility is co-located with parent company Calnetix on a seven-acre campus in Cerritos, California where the patent wall shown above is located.
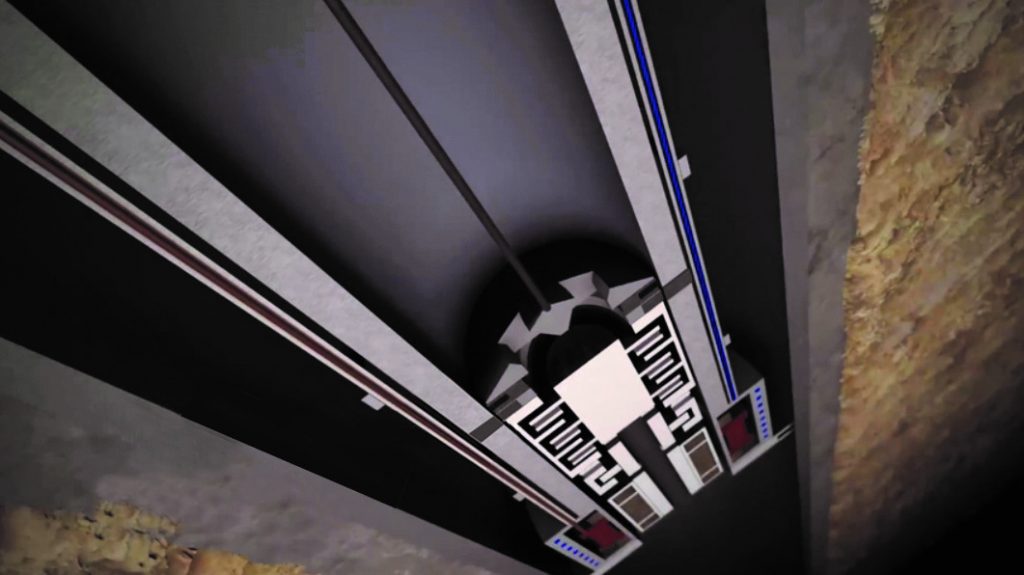
In the DeepStar program, Upwing and its project partner Mitsubishi Heavy Industries (MHI) recently were awarded the next phase of the Magnetic Drive System project by the global offshore research and development consortium. Following their completion of a design study last year, the new phase will include the design, build and test of enabling technologies that are the backbone of Upwing’s MDS concept for a reliable and retrievable electric submersible pump.
“The innovative MDS topology built on advanced magnetic technologies will significantly increase production uptime while decreasing the total cost of ownership by 75 percent in deepwater offshore applications,” said Artinian. DeepStar is a joint industry technology development program. Members include Shell, Total, CNOOC, Anadarko, Equinor, ExxonMobil, JX Nippon, Chevron, Petrobras and Woodside.
Upwing will design, fabricate and test a full-scale passive radial bearing assembly as well as a magnetic vibration and temperature sensor system to be utilized between the pump stages and motor in the MDS. Upwing and MHI engineers planned to begin work on Phase II in June and are scheduled to complete the experimental prototype, including component testing, by May 2021.
Robust magnetic designs inside
Upwing’s artificial lift technologies are bringing reliability to downhole rotating devices by leveraging permanent magnet motors and applying magnetic fields to the architecture of its tools. All of its innovative technologies are proprietary and patented or patent pending, says the company, which has provided the following details about them.
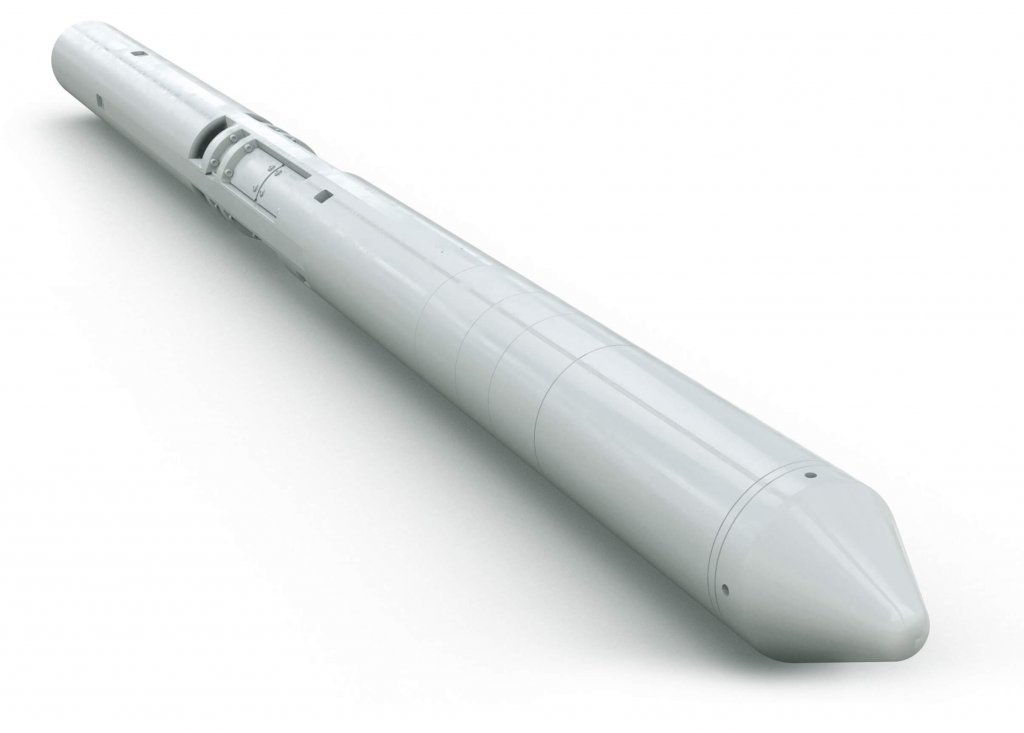
The SCS is a high-speed downhole compressor system driven by a magnetically levitated permanent magnet motor. The high-speed permanent magnet motor’s rugged, compact design delivers higher energy density and lower heat dissipation to provide much greater efficiency than standard electric motors, says the company. The entire motor is hermetically sealed to isolate electrical components from hostile downhole fluids.
The magnetic coupling transmits torque from the motor to the compressor without a mechanical shaft, which eliminates the need for a rotary seal, pressure-compensating chambers and dielectric oil. The active magnetic bearing provides support to the thrust loads in the compressor. With no physical contact and no lubrication needed, the bearing delivers extensive operational life with zero friction. Passive magnetic bearings provide radial support for the high-speed, rotating components.
The following details are excerpted from the company’s descriptions which can be fully seen on its website.
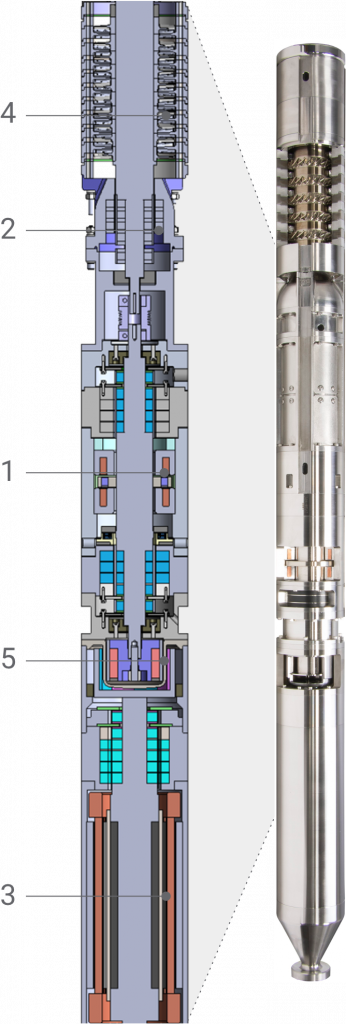
The accompanying diagram illustrates five key features of the SCS:
- Active Magnetic Thrust Bearings – The active bearing system supports hydraulic section thrust loads without any physical contact or lubrication, delivering unlimited bearing life. Magnetic bearing controllers located on the surface provide real time information on thrust loads from the compressor to enable system diagnostic and prognostic capabilities.
- Passive Magnetic Radial Bearings – The radial bearing system supports high-speed rotating components radially without any physical contact or lubrication, delivering unlimited bearing life. Smart damping without the need of active controls improves system stability by minimizing the vibrations of the motors and compressors.
- Hermetically Sealed High Speed PM Motors – In comparison to other types of motors used downhole, Upwing’s permanent magnet (PM) motors enable a shorter tool length due to their higher energy density and lower heat dissipation from higher efficiency levels. The completely canned motor system, including both the rotor and stator components, isolates the failure-prone electrical system from hostile downhole fluids.
- Hybrid Compressors – The hybrid multiphase compressor system decreases the bottom hole flowing pressure dynamically at the intake of the compressor and boosts the pressure and velocity at the discharge to carry liquids uphole.
- Magnetic Coupling – Upwing’s novel “protector-less” design is enabled by transmitting the torque from the hermetically sealed motor to the compressor without a mechanical shaft.
PM Motor as Magnetic Coupling
The permanent magnet motor serves as a magnetic coupling. In the MDS, the stator is canned as a part of the well’s permanent completion, allowing the rotor and other rotating pump components to be retrieved independently from the stator. There are no connections between the rotating and stationary components. The stators initially are varnished with a vacuum pressure impregnation process. All varnished copper wires are potted, and the complete stator is inserted into a hermetically sealed chamber for protection and reliability.
Lower Heat Dissipation
Magnetic losses are generated when magnetic field variations cause losses in magnetically and electrically conductive materials. The high strength magnets positioned on the rotor that provide the magnetic field, rather than coils that need to be energized, in a PM machine serve to minimize any field variations to which the components on the rotor may be exposed.
Traditional ESP topologies, however, cannot take full advantage of PM motor benefits by replacing an induction rotor with a PM rotor, explains Upwing. The limiting factor of delivering power in ESP applications is thermal management. In conventional ESP motors, which operate in liquid filled chambers that have a balanced pressure with the environment, the friction losses generate more heat than the motor electromagnetic losses. This heat must be removed from the motor and put into the pumped fluid, where the only path is through the housing over the stator. Therefore, replacing an induction motor rotor with a PM rotor will not have significant value because the same amount of friction losses are generated with the PM rotor, and the same poor conduction path for heat to the production fluid is present. A system level approach specifically for specifically for downhole applications is required.
Isolation from Harsh Environments
In order to deliver the full potential of PM motors, Upwing has developed a unique motor and hydraulic architecture for both the SCS and MDS. For the SCS, the hermetically sealed motor operates in an inert gas at atmospheric pressure with large gaps, and therefore, does not generate significant friction losses even at 50,000rpm. The heat, which is mostly generated in the stator component of the motor, is cooled through the flow of the gas over the surface of the sealed chamber.
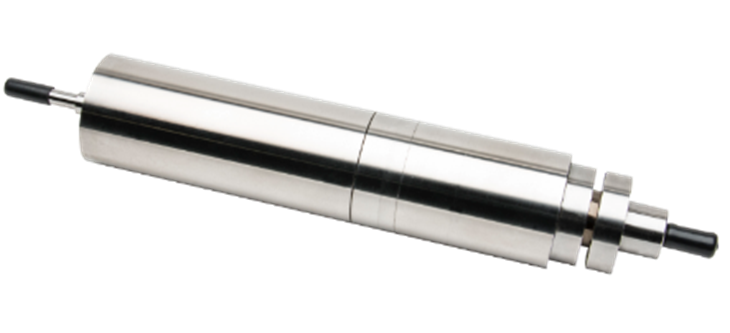
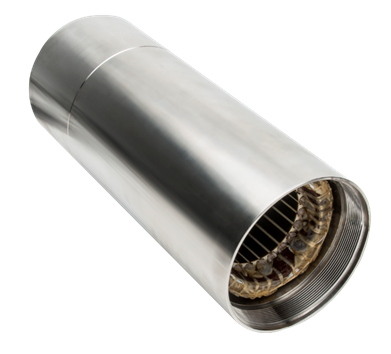
For the MDS, the motor assemblies are completely canned. The stator and rotor are independently hermetically sealed and operate with a large clearance. The motor is integrated such that the separate rotor can be retracted along with the pump section independent of the stator, as the stator is part of the permanent completion. This flow through architecture not only provides cost effective rotor retrievability without the need to affect any electrical connections or the permanent completion downhole, but also provides direct access to the production fluid as a coolant medium to the maximum motor surface area to increase the heat dissipation. The motors are on the order of five times the energy density of conventional induction motors due to their open architecture that can dissipate more heat and to run to higher speeds.
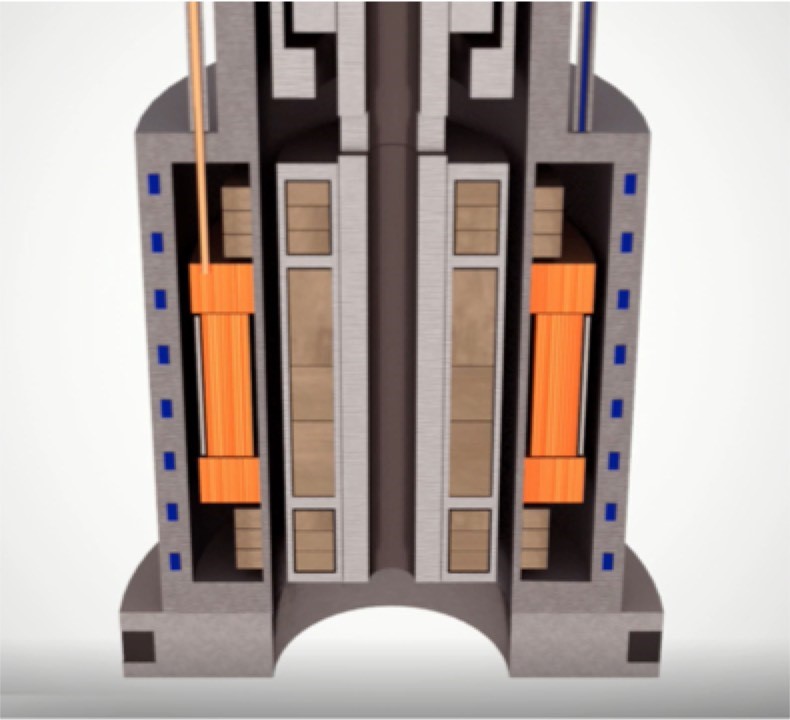
Magnetic Coupling
The radial gap type coupling includes an inner rotor that is connected to a thrust module shaft, with a surrounding sleeve to protect the magnets that generate a magnetic field. This inner rotor is designed to be exposed to the downhole fluids, offering a fully sealed assembly capable of operating in the high pressure, high temperature well bore environment for the life of the device.
The outer rotor of the magnetic coupling is sealed with the PM motor in a hermetically sealed section that is maintained at a low-pressure gas environment, since it generates higher windage losses due to its larger diameter. An isolation sealing can between the inner rotor and the outer rotor allows for magnetic field linkage between the two rotors for torque transmittal from outer to inner rotors.
For more info, see www.upwingenergy.com.