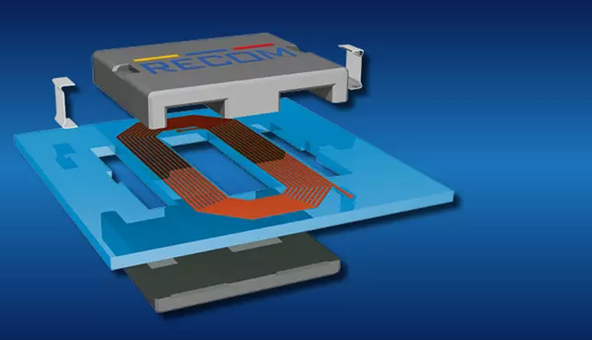
Transformers can be a thorn in the side of designers of DC/DC converters. They are bulky, expensive and can be hard to manufacture. Find out how planar transformers can boost quality and lower the cost of low-wattage DC/DC converter designs in a helpful presentation from RECOM, a specialist in the development and manufacture of standard and custom DC/DC and AC/DC converters located in Austria. A few highlights are given here, the complete presentation is available on the company’s website.
The transformer is at the core of any DC/DC converter design and is the most critical component in determining the overall performance. First, it is important to understand the difference between planar versus toroidal transformers.
Traditionally, transformers and inductors are wound components. Most mass-produced low-power DC/DC converters use hand-wound toroidal transformers; it is extremely difficult to develop an automatic manufacturing process for a transformer that requires up to six separate windings with a diameter core as small as 6mm with a 3mm hole. Manufacturers such as RECOM have developed automatic winding machines to manufacture such tiny toroidal transformers, but such solutions can be hard to find.
Planar magnetics have existed since the 1980s, but the manufacturing process was initially prohibitively expensive, so planar transformers had limited market penetration outside of specialized applications. However, as manufacturing technology has advanced, the cost of planar transformers has decreased, allowing for the development of new applications.
Planar transformer construction and design
A planar transformer or inductor uses the copper layers in a multilayer printed circuit board (PCB) to form the windings; a ferrite core surrounds the windings. In order to make the required number of turns, hidden vias are used to form connections from one PCB layer to the next. Multiple vias connected in parallel can carry sufficient current to make a useful miniature power transformer.
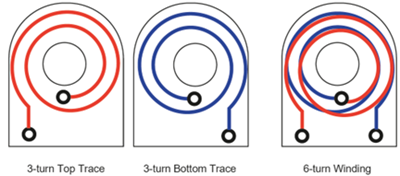
This figure shows how a six-turn winding can be formed by stacking two layers connected with a hidden via. Observe how this arrangement places the two ends of the winding conveniently outside the ferrite core. The primary and secondary windings are typically interleaved to reduce leakage inductance. Using a printed circuit board gives a mechanically stable winding structure that is extremely consistent and lends itself to automated production. In addition, advances in multilayer PCB construction mean that the epoxy insulation between the windings can withstand high isolation voltages between primary and secondary circuits.
There are certainly technical challenges in design and construction, but once these problems are resolved, planar technology enables the construction of an extremely flat transformer capable of transmitting large amounts of power, allowing the DC/DC converter to have a very low height profile. Other advantages include better heat dissipation in the windings, low leakage inductance and higher power densities.
Planar transformers move to lower power levels
As a result, the planar transformer has become an indispensable component in high-power DC/DC converter technology, but RECOM is now incorporating planar technology into lower-wattage, smaller-sized converters.
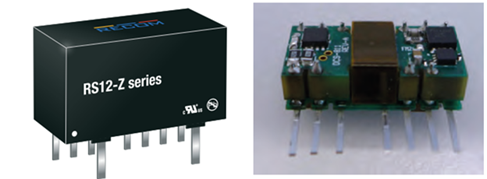
Changing to a planar transformer improves the quality of these designs by allowing for a more automated manufacturing process with reduced hand assembly. It is also easier to develop customized designs because it is not necessary to change transformer windings to accommodate different voltages.
RECOM manufactures a full range of standard and customized DC/DC and AC/DC converters in every power class from sub-1W to tens of kW, alongside switching regulators and LED drivers in a wide selection of formats. Embracing the benefits of planar transformer technology, it is adding planar transformers across its DC/DC converter product line. The company headquarters are located in Gmunden, Austria. For access to the full presentation, visit www.recom-power.com.