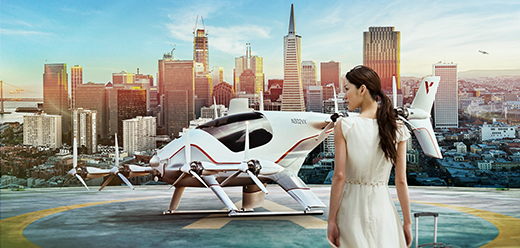
The race to develop autonomous electric aircraft is poised to open new markets for permanent magnet motors as several leading aviation firms are breaking into the skies with new prototypes of vertical take-off and landing craft designed for commercial passenger and cargo transport.
Boeing’s Aurora Flight Sciences and Airbus are both flight testing new models powered by an advanced, integrated motor and controller from MAGicALL, a developer of innovative magnetic technology. In May, Boeing also completed an important flight test for a cargo UAV that is fully electric.
Airbus leads the way. It recently celebrated the 50th full-scale test flight of its Vahana aircraft which the company envisions as a technological breakthrough in urban air mobility — a self-piloted, highly automated vertical take-off and landing passenger aircraft that can become a replacement for short-range urban transportation like cars or trains. Applications seen for the craft are cargo delivery, emergency services, search and rescue or even as a tool to deploy modular infrastructure in disaster sites.
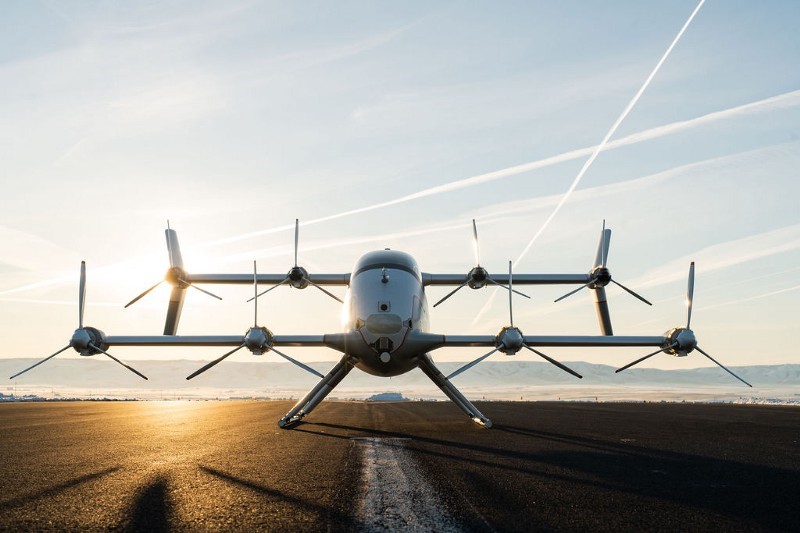
Vahana powered by 8 integrated electric motor-controllers
Vahana uses eight 45-kW electric motors and a tandem tilt-wing configuration that converts between rotor-borne vertical and wing-borne forward flight. This configuration enables Vahana to achieve both vertical take-off and landing as well as cross-city flight range on battery power alone. Its cruise speed is 100 knots, enabling trip times that are two to four times faster than cars. The vehicle is fully self-piloted, which is enabled by its onboard detect-and-avoid systems that can identify both air and ground-borne hazards.
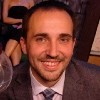
Zach Lovering
Zach Lovering, project executive of Vahana and vice president of urban air mobility systems for Airbus, reports in a recent update that more flights are planned through the first half of this year as the development team studies and checks flight controls, navigation, failure detection and mitigation, and noise. “To date we’ve flown 50 full-scale test flights totaling over 5 flight hours,” said Lovering. The flight tests take place at a test range for autonomous aircraft at Eastern Oregon Regional Airport in Pendleton, OR. Airbus built a specially configured 9,600 sq ft hangar for the Vahana project there in 2017. The Vahana project is being developed by A3, the Silicon Valley outpost of Airbus. A3 functions as an emerging technology development unit for the parent company which is based in Toulouse, France.
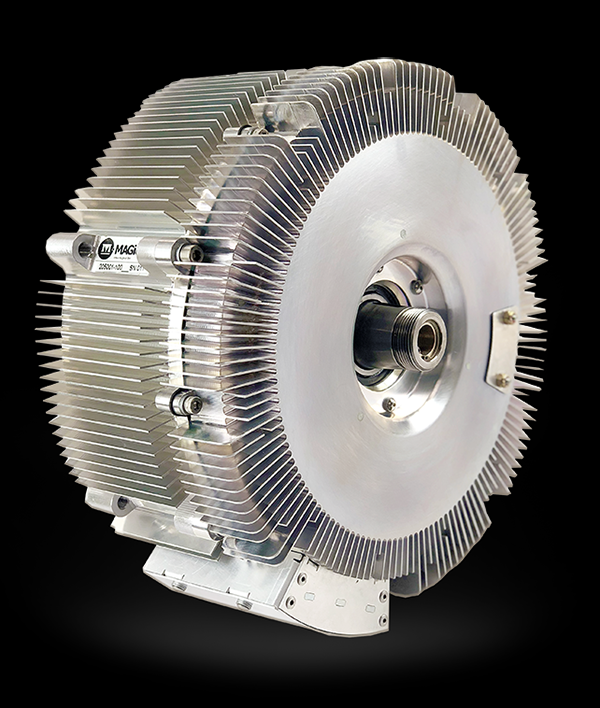
MAGiDRIVE integrated motor/controller
The motors, provided by MAGicALL of Camarillo, CA, are integrated with controllers to configure the company’s MAGiDRIVE system which features fully bi-directional four-quadrant operation since they can operate in both directions as either motors or generators. The latest versions in the product line feature specific torque greater than 40 Nm/kg and power levels up to 500 kW, according to Joel Wacknov, CEO. The units are available in sizes from 4” to 24” diameter, with torque capability up to 5000 Nm. DC bus voltages can range from 24V to 800V depending on the model.
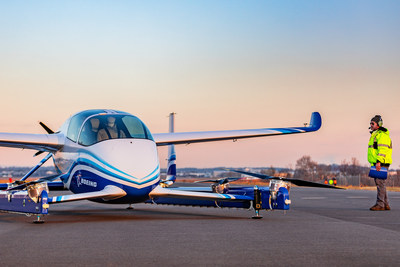
Flight test for passenger UAV from Boeing/Aurora Flight Sciences
Boeing is also using the MAGiDRIVEs in its autonomous passenger air vehicle (PAV). In January, the prototype performed its first flight test in Manassas, VA. Boeing NeXt, which leads the company’s urban air mobility efforts, worked with Boeing subsidiary Aurora Flight Sciences to design and develop the electric vertical takeoff and landing aircraft (VTOL).
The flight test involved a controlled takeoff, hover and landing which tested the vehicle’s autonomous functions and ground control systems. Future flights will test forward, wing-borne flight, as well as the transition phase between vertical and forward-flight modes. This transition phase is typically the most significant engineering challenge for any high-speed VTOL aircraft.
“In one year, we have progressed from a conceptual design to a flying prototype,” said Greg Hyslop, Boeing’s chief technology officer. The prototype is designed for fully autonomous flight from takeoff to landing, with a range of up to 50 miles. Measuring 30 ft long and 28 ft wide, its airframe integrates the propulsion and wing systems to achieve efficient hover and forward flight.
“This is what revolution looks like, and it’s because of autonomy,” said John Langford, CEO of Aurora Flight Sciences, based in Manassas. “Certifiable autonomy is going to make quiet, clean and safe urban air mobility possible.”
The test flight represents the latest milestone for Boeing NeXt. The division works with regulatory agencies and industry partners to pioneer the introduction of a new mobility ecosystem where autonomous and piloted air vehicles safely coexist.
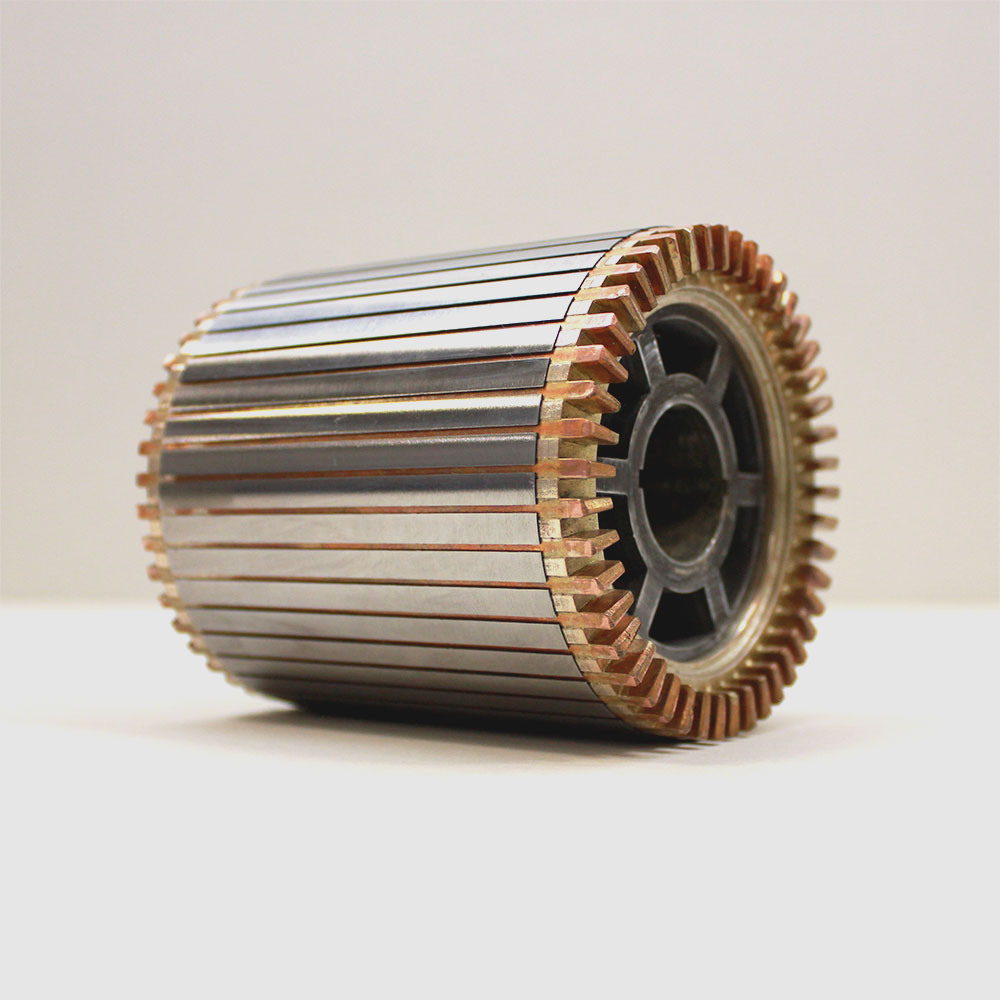
The company produces a wide range of custom designed components including motors, generators, inductors, and transformers. It has full system design expertise, including the ability to design power electronics and digital controls tailored to specific applications and magnetic components. “Delivering open-frame or a complete assembly, our advanced design technology results in unparalleled low weight, small size and highly efficient components, tailored specifically to the client’s product,” says Wacknov. An AS9100C certified organization, the company also provides build-to-print magnet production service, fabricating magnets to customer specification.
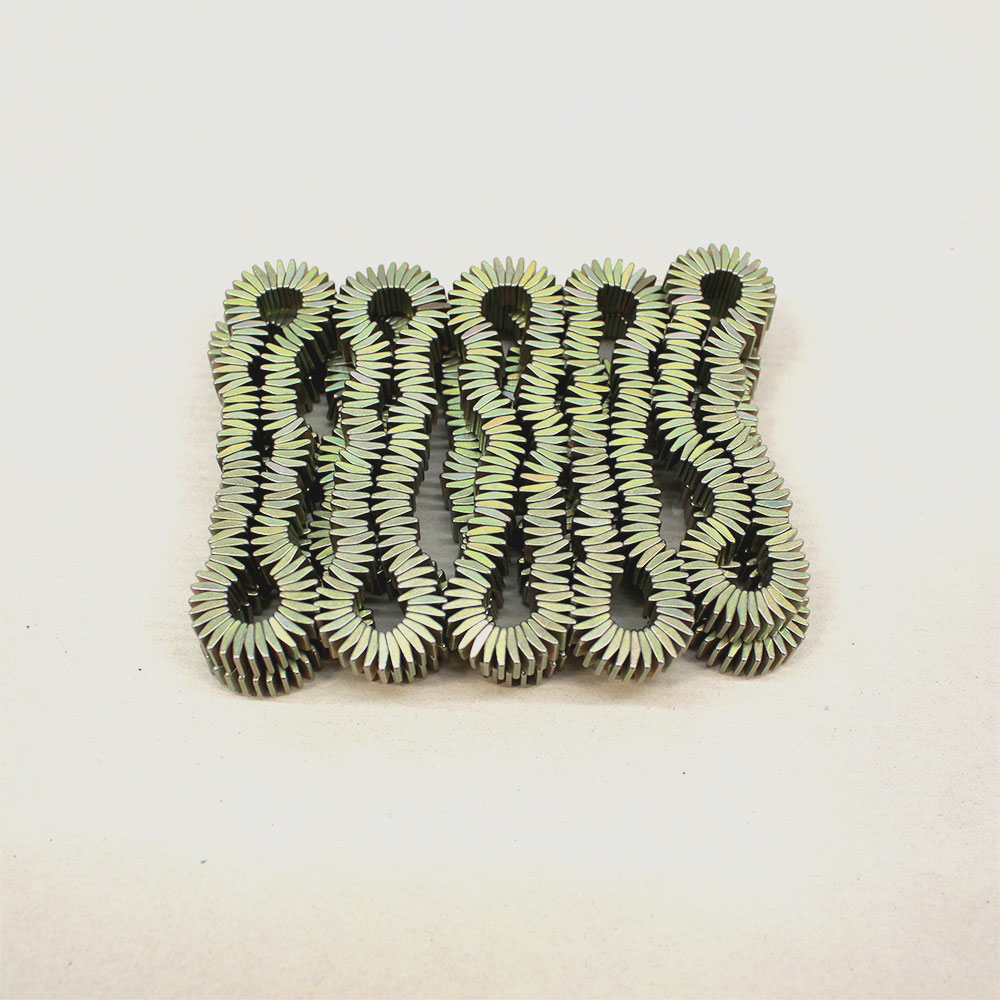
Custom magnet from MAGicALL
It also develops inductive motor technology for applications where permanent magnet motors are not suitable. It has developed a proprietary brazing process for manufacturing copper rotor induction motors. These motors are extremely rugged and fault tolerant, making them ideal for demanding aerospace and downhole applications.
For more info, see www.airbus.com, www.boeing.com, www.magicall.biz.