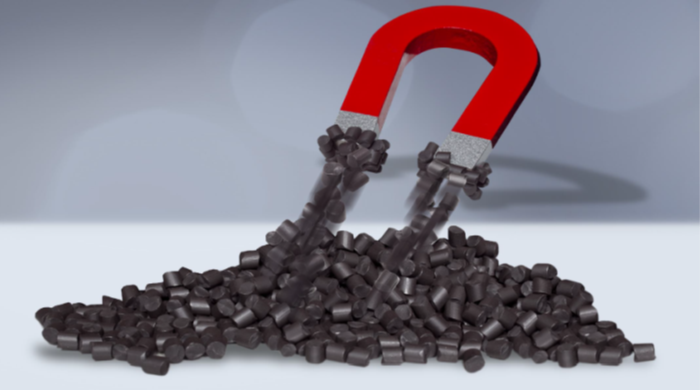
Polymer bonded magnets are destined to play an important role in future electrification efforts, especially with the use of specially formulated plastic magnetic compounds and careful design efforts to optimize manufacturability and product performance.
These were some of the points made by a plastics product development specialist at the Sixth Ruhr Symposium held this fall at University of Duisberg-Essen in Germany. Focus of the event was on the latest advancements in functional magnetic materials for performance enhancement in electric drives and thermal management including magnetocaloric refrigeration. The annual event brings together leading material scientists with research and development staff from top manufacturers including many leading automotive companies.
Because of the importance of magnetics in efficient energy conversion, new attention is being paid to the attributes of injection molded magnets especially using plastic compounds specially formulated and custom engineered to optimize product performance, explained Robert Konnerth, product manager for Barlog Gruppe. They combine the manufacturing advantages of plastic with the magnetic attributes of metal, he noted. Manufacturing process can be efficient especially in high volumes. They offer high design freedom, good ductility, weight-saving and assembly savings along with satisfying magnetic values.
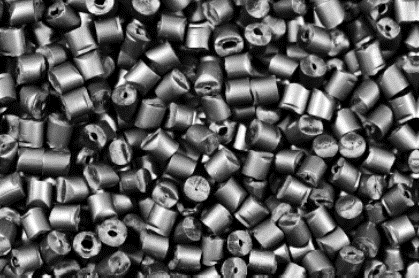
While a supplier of plastic materials, Barlog also provides compound development, plastic granules, application development, prototypes-preproduction and small batch series production, said Konnerth. Its hard magnetic compound, Kebablend M is a permanent magnetic plastic with remanence of max 540 mT and coercive field strength of max 800 kA/m, making it suitable for custom polymer bonded magnets in the manufacture of products such as electric water pumps. Its soft magnetic compound, Kebablend MW, is a non-permanent magnetic plastic with a saturation flux density of 1.200 mT and permeability of max 90 which is suitable for the manufacture of products such as a lightweight E-engine.
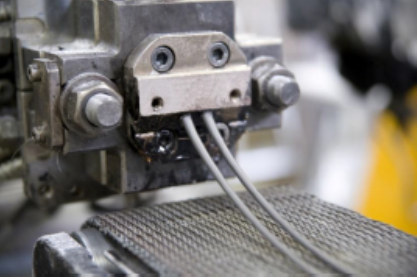
Konnerth gave an overview of how their product development for a client typically works. The first step is material development to come up with a customized magnetic compound. This can involve selection of appropriate polymer and filler, consideration of standards and approvals, small-series compounding, and upscaling for series application. The prototyping process typically involves creation of an aluminium protype tool, design of magnetization equipment, the manufacture of prototypes, small-series production, and verifying performance of the parts.
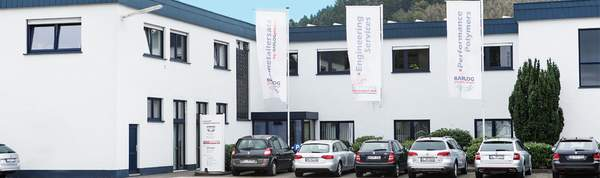
Based in Overath, Barlog is a supplier of plastics raw materials as well as a broad range of resources for product design and engineering including support in material selection and analyses, also prototypes, batch production and staff training. It specializes in products with highly specialized material properties such as magnetizable plastics, highly reinforced polymers as metal substitutes or materials for lightweight construction.
For more info, see www.barlog.de and www.ruhr-symposium.de.