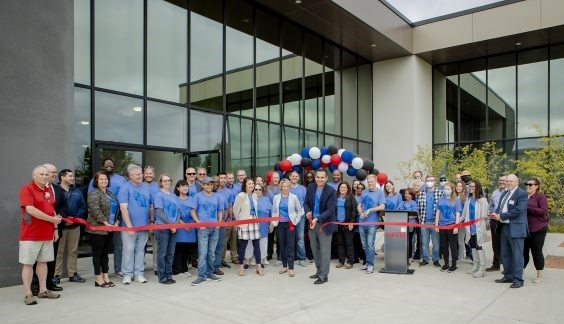
Power quality manufacturer MTE Corporation has opened a new headquarters in Menomonee Falls, Wisconsin and recently introduced new filters for protecting motors. A supplier of products designed to improve the reliability of power electronic systems, MTE designs passive harmonic filters, line and load reactors, link chokes, dV/dt and sinewave motor protection filters, power conditioning and distribution units and custom magnetic products.
“Our new headquarters exemplifies the investments we are making in our business, employees, and community for today and for years to come,” commented Ahsan Javed, president, at the grand opening.
An innovative lab incorporates state-of-the-art technology which allows the company to accelerate new product development. The lab provides new equipment and capabilities, said Todd Shudarek, director of engineering. “Our new power quality lab allows us to rapidly prototype and test products for our customers around the world. We can be more responsive and have more space to support the growing needs of our business.”
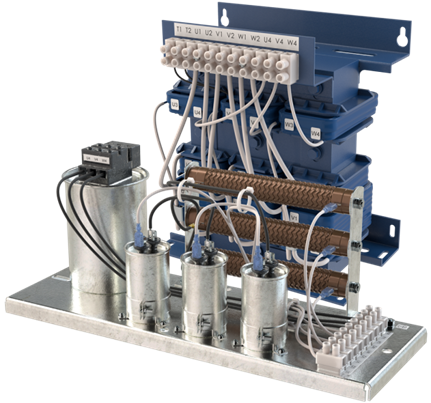
One of the new filters recently introduced is the Matrix Air EC Motor Filter, designed to mitigate harmonics that are produced by electronically commutated motors (ECMs). The new solution is optimized for HVAC-R and data center cooling applications and can also be used anywhere ECMs are installed such as conveyance systems, variable refrigeration flow equipment, and refrigerated displays.
ECMs combine the benefits of DC electric motors with integrated drives and are primarily used to control the speed of fans such as those found in data center fan walls and air handling units. However, because ECMs emulate variable frequency drives, they can produce damaging harmonics that degrade power quality which causes nuisance tripping, equipment to overheat and problems with electrical utilities. The new filter resolves these harmonic issues to provide greater stability across fan speed ranges which allows ECMs to operate at full speed and higher efficiency.
Matrix Air is producing groundbreaking results, says Javed. “EC motors are growing in adoption as applications demand higher efficiency and control. Our proprietary Matrix Air design is ideally suited to help these critical systems run cooler, smoother and without downtime. The benefits are tangible, with a large data center customer now saving thousands on their electrical bills all while enhancing uptime and reliability.” The product is based on MTE’s patented Matrix AP Filter product line. As each application is unique in terms of fans, load and other technical requirements, MTE designs a customized solution to meet customer specifications.
The Matrix Air is 25% smaller in size to competitive options, notes Shudarek. “We developed Matrix Air to fit within already densely packed electronics cabinets. With limited space, it was imperative that we minimize the footprint.”
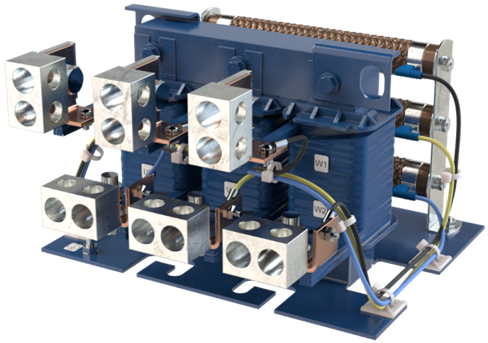
Another recent introduction is the company’s new dV E-Series motor protection filter. Using a dV/dt filter enables uptime and protects AC motors from the destructive effects of the variable frequency drive (VFD) pulse width modulated voltage that can damage cables and motors.
The dV E-Series mitigates reflective waves, reduces rise time, and limits peak voltage resulting in a reduced motor heating, longer cable and motor life, and a significant reduction in downtime and total ownership cost. The dV E-series offers up to 60% lower watts loss versus competitive dV/dt filters, enabling more efficiency and savings, and ensuring longer life and protection for equipment around the filter. See www.mtecorp.com.