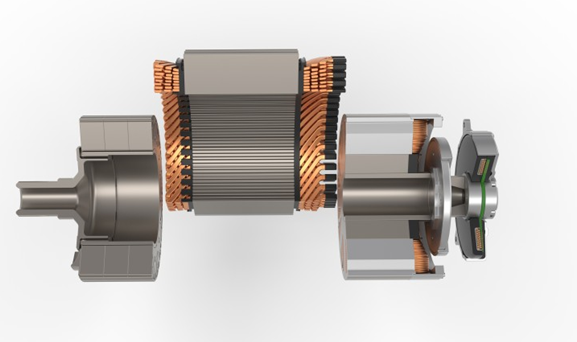
“Electrification is the focus of the future for MAHLE as we continue to position ourselves as a systems-expertise champion in e-mobility,” said Peter Lynch, vice president of Sales & Application Engineering and president, MAHLE Industries, Inc., at this year’s Consumer Electronics Show. The company used the event’s impact as a showcase for breakthrough technology to demonstrate the latest developments in its extensive portfolio for e-mobility. Among them were:
- A new technology kit for electric motors combines the advantages of MAHLE’s benchmark SCT (Superior Continuous Torque) and MCT (Magnet-free Contactless Transmitter) electric motors. The “perfect motor” combines permanently high peak power, contactless and thus wear-free power transmission, the absence of rare earths, and maximum efficiency.
- New battery cooling plates inspired by nature ensure fast charging, long cruising range and long service life for sensitive lithium-ion batteries, making the complete system significantly more efficient with up to 20% battery life.
- A wireless-charging positioning system that allows an electric vehicle to be simply, reliably and precisely aligned above a charging coil in the floor. SAE International, the US-based standards developing organization for engineering professionals, has chosen the system as the global standard solution for wireless charging.
The technology kit for electric motors, shown in image at top, essentially provides a toolbox whereby MAHLE can offer its customers customized electrification solutions for any vehicle class, application or even brand philosophy. The MCT and endurance-champion SCT electric motors are among the latest innovations from the German automotive supplier in the field of electric drives. Dispensing with rare earths in MCT technology not only makes production more environmentally friendly, but also brings advantages in terms of costs and raw- material security. It is particularly efficient at almost all operating points.
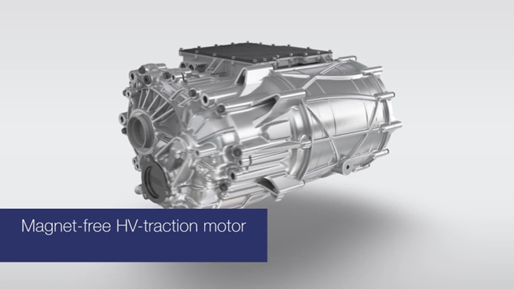
The MCT electric motor shows its efficiency advantages especially in those areas that are frequently used in real road traffic. The MCT electric motor is characterized by high durability because the necessary transmission of electric currents between the rotating and stationary parts inside the motor is contactless and thus wear-free. The motor therefore is maintenance-free and suitable for a wide range of applications.
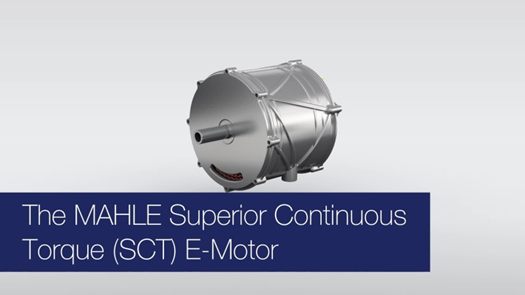
The SCT electric motor is the most enduring electric motor in the MAHLE range. The traction motor can operate at high power for an unlimited period of time. This technological leap was made possible by a new cooling concept. Innovative integrated oil cooling not only makes the e-motor robust, but at the same time also allows the waste heat generated to be used in the vehicle’s overall system. MAHLE engineers emphasize its small size, light weight and efficiency. The extremely compact design also results in a material-cost and weight advantage; a lighter motor requires less material in production and at the same time increases the possible payload in commercial vehicles.
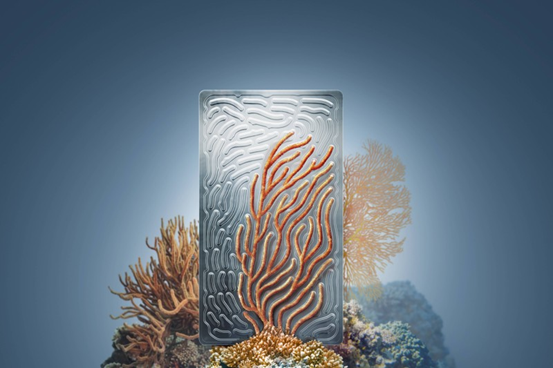
Essential for battery electric vehicles is heating and cooling in the car, the thermal management that automotive design engineers aspire to. Using nature as a model, MAHLE has now achieved a technological leap forward with its new battery cooling plate. The innovative plates help ensure fast charging, long cruising range and long service life for sensitive lithium-ion batteries, making the complete system significantly more efficient with up to 20% battery life.
The group”s engineers have developed a bionic structure that is modeled on nature for the cooling channels that causes the coolant to flow differently. This significantly improves the thermodynamic performance and structural-mechanical properties of the cooling plate. As a result, MAHLE was able to increase cooling performance by 10 percent and reduce pressure loss by 20 percent. As a result, the battery can be reliably and homogeneously kept within the necessary temperature window. It thus becomes more efficient and can be charged more quickly. In addition, its service life is increased. On top of this, MAHLE has reduced the amount of material used for the plate by up to 15 percent, thus saving 15 percent CO2.
“With our new battery cooling plate, we are breaking away from technical geometries and instead using natural structures, such as the coral shape-with outstanding effect for our cooling technology and great advantages in structural stability to boot,” said Dr. Uli Christian Blessing, head of global development thermal management at MAHLE.
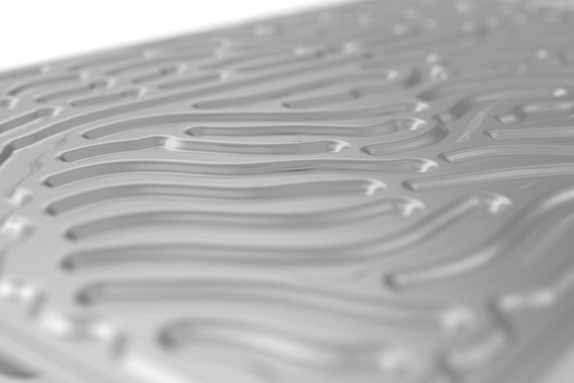
Lithium-ion batteries are very temperature-sensitive. The cell temperature should not exceed 40 degrees Celsius over longer periods – even under extreme conditions such as fast charging. At the same time, the temperature distribution across all cells must be as uniform as possible. The batteries are therefore usually cooled via flow-through plates.
In the latest development from MAHLE, the flow rate of the coolant is controlled according to demand: Especially in the case of small temperature differences between battery cells and coolant, heat transfer is improved by faster flow rates. The bionic battery cooling plate from MAHLE works so efficiently that the temperature range can be reduced by 50 percent and peak temperatures in particular can be significantly lowered. In this way, the Group makes a major contribution to the service life and performance of the expensive battery.
And the bionic structure also offers design advantages. Greater rigidity makes it possible to use the battery cooling plate with lower material thicknesses. This further improves its effectiveness. In addition, there are more degrees of freedom to enable new manufacturing processes with less energy and material input. A contribution to sustainability. For well over a decade, MAHLE has been developing systems for cooling lithium-ion batteries for small cars through to large commercial vehicles, making it one of the pioneers in this field of technology.
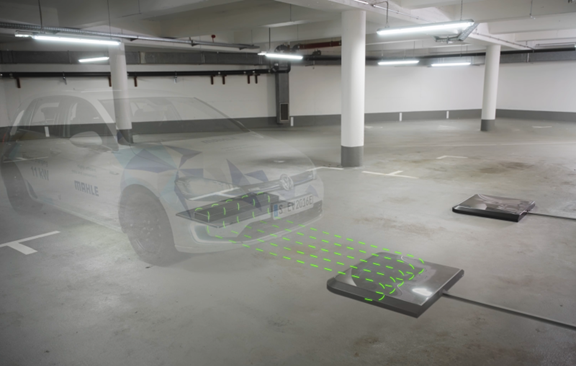
The company’s all-new positioning system for wireless charging was recently chosen as the global standard technology by SAE International. It allows an electric vehicle to be simply, reliably and precisely aligned above an inductive charging coil in the floor. SAE International, the US-based standards developing organization for engineering professionals, has chosen the MAHLE positioning system as the global standard solution for wireless charging.
The cross-manufacturer solution from MAHLE paves the way for the comprehensive and rapid market launch of this attractive alternative to wired charging for batteries and for electric and hybrid vehicles. It is based on a magnetic field and automatically establishes a connection with the controlled charging point as the electric vehicle approaches. A special navigation system in the vehicle display supports the driver, and the car is soon in the ideal position. The charging process begins automatically.
About MAHLE
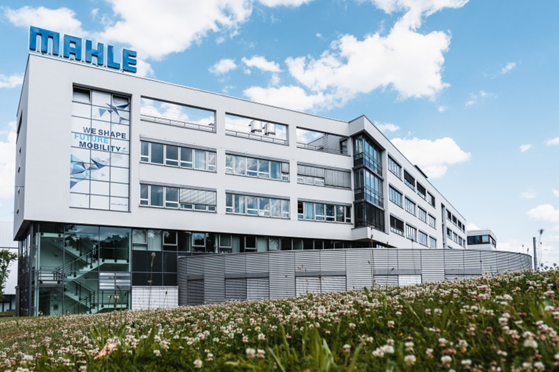
About:
MAHLE is a leading international development partner and supplier to the automotive industry with customers in both passenger car and commercial vehicle sectors. Founded in 1920, the technology group is working on the climate-neutral mobility of tomorrow, with a focus on the strategic areas of electrification and thermal management as well as further technology fields to reduce CO2 emissions, such as fuel cells or highly efficient combustion engines that also run on hydrogen or synthetic fuels. Today, one in every two vehicles globally is equipped with MAHLE components.
MAHLE generated sales of more than EUR 12 billion in 2022. The company is represented with approximately 72,000 employees at 152 production locations and 12 major research and development centers in more than 30 countries (as of 31.12.2022). For more info, see www.mahle.com.