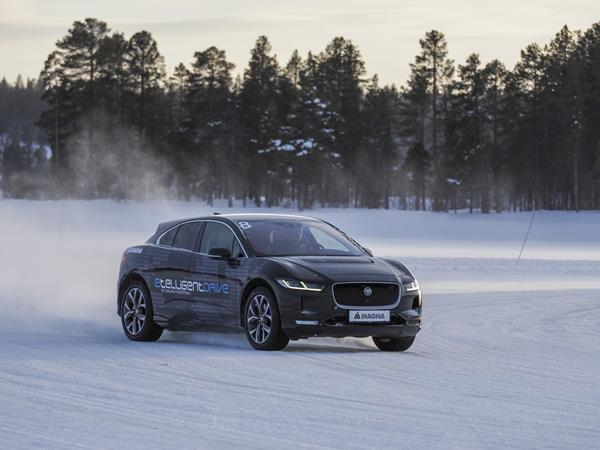
Encompassing different combinations of magnetic technology, Canadian automotive supplier Magna is building a suite of powertrains and components for electric vehicles that reflect its total systems approach to serve the evolving needs of automotive manufacturers. Shown above is, e4, the company’s latest technology demonstrator car during winter test driving in northern Sweden, which showcases the new systems in a pure EV format.
The e4 includes highly integrated permanent magnet synchronous motor (PSM) electric drive systems on the front and rear axle. The unit on the front is equipped with a mechanical differential, while the unit on the rear has a twin-clutch torque vectoring system. Both drives, including the gearbox, electric motors, inverters, inverter software, and vehicle control strategy, are developments from Magna. They deliver peak output of 180 kW each with a high average efficiency of about 90 percent.
Launched this year, the e4 is the latest example of Magna’s modular and scalable powertrain solutions for EVs. Its e2 prototype, introduced a year earlier, allows a comparison of eight different powertrain configurations within a single vehicle architecture. Magna expects that global growth in e-mobility will include mild and micro hybrids, high-voltage hybrids and electric vehicles.
“We are positioned to capitalize on the changing landscape with a strong product portfolio that covers various powertrain types,” said Tom Rucker, president of Magna Powertrain. “From reducing CO2 and supporting sustainability goals to delivering dynamic, fun-to-drive performance, we can lead automakers through the powertrain transition with our modular and scalable powertrain configurations.” Coming soon, said Rucker in April, are all-wheel-drive systems from Magna that replace mechanical components with complete electric-drive powertrain systems (motor-inverter-gearbox) and electric axles.
Magna continues to work on further optimization of e-drives with a second-generation system, optimizing decoupling strategies, winding technologies for the e-machines, and advanced electronic controls.
“The e4 demonstrates how cost, efficiency, and driving dynamics can be optimized without making any trade-offs”, says Harald Naunheimer, vice president future products at Magna Powertrain. The efficiency improvements can benefit hybrid vehicles as well as battery electric vehicles. For example, the rear axle drive of the e4 can also be used in a high-voltage hybrid vehicle, while offering the same efficiency and dynamics advantages.
Magna Powertrain uses a modular system of scalable building blocks, which enables a high share of common parts. This applies to both electric axle drives (e-drives) and transmissions for conventional and hybrid drives. For example, a common, state-of-the-art electric motor platform can be used for e-drives as well as hybrid dual-clutch transmissions. All these applications can also utilize innovations like the decoupling of drives to further increase efficiency.
“The scalability of building blocks and modular design allows tailor-made solutions to meet a wide range of customer requirements,” says Anton Mayer, senior vice president engineering at Magna Powertrain. “This applies both to OEMs, who can reduce the consumption of their fleets, and to consumers, who benefit from lower costs, greater range, and more driving pleasure and safety.”
The company’s high voltage portfolio covers a diverse range of single components to complete systems, from mechanical e-axles up to highly integrated e-drives. Variations are available for plug-in hybrids as well as for pure electric vehicles. Its platform approach provides flexibility using cross-project synergies with scalability from 50 – 250 kW.
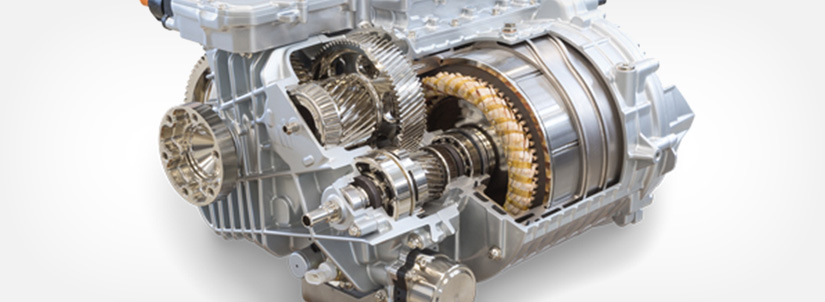
Its Highly Integrated eDrive System Low is a small e-drive system that contains either an asynchronous motor or a PSM e-machine, an integrated single-speed gearbox and a high voltage inverter. The system’s power ranges from 60 to 90 kW. The Mid version includes a gearbox, a PSM e-machine with 90-160 kW power and an inverter. It can be utilized as a primary axle for battery electric vehicles or as a secondary axle for full hybrid and battery electric vehicles. At the top of the range is the High version with 160-250 kW power PSM e-machine, inverter, and a torque-vectoring optional gearbox, designed for high-performance battery electric vehicles.
Other avenues also are being explored by the company, including efforts to reduce dependence on rare earth magnets in EV powertrains. In 2019, it was awarded a grant by the U.S. Department of Energy to develop advanced electric motor technologies for next-generation vehicle propulsion systems. In partnership with the Illinois Institute of Technology and University of Wisconsin-Madison, Magna is applying its powertrain, electronics and full-vehicle expertise to deliver an automotive-grade, high-performance electric motor that aims to achieve increased power density and reduced cost compared to current e-motors.
The objective is to develop an electric motor that is half the cost and eight times the power density, while delivering 125 kW of peak power. The reduction in cost is the result of eliminating the use of rare-earth permanent magnets. To be presented for evaluation in 2021, the project will integrate the electric motor technologies with a transmission and inverter as part of an overall e-drive system. The project scope includes development and use of innovative materials, cooling technologies, winding technologies, simulation models, as well as control and optimization techniques. For more info, see www.magna.com.