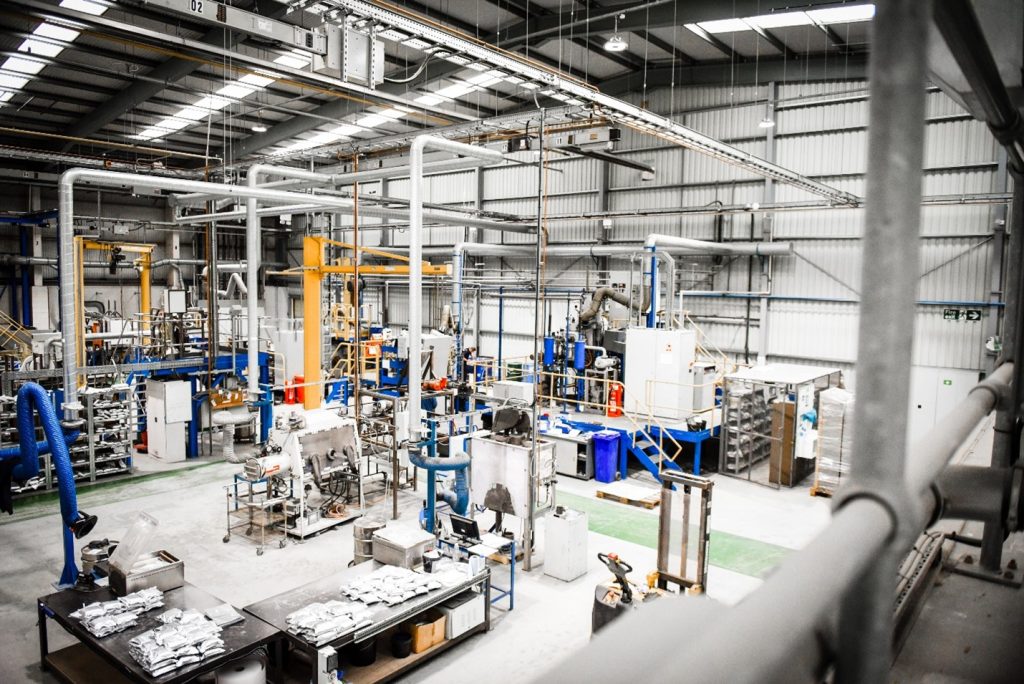
Less Common Metals, a refiner and leading producer of rare earth metals and alloys in the Western world, continues to expand its technical capabilities with the addition of more process equipment at its headquarters in England, with a newly designed molten salt electrolysis cell and through an innovative collaborative effort on magnet recycling. This article highlights some of the recent developments.
“LCM’s global presence has continued to grow, allowing us to work on innovative projects with partners worldwide,” noted Aaron Riley, general manager, in a year-end summary he made in December 2024. “This year marked a leap forward in our expansion plans into the US and EU markets. We’ve also broadened our metal making capabilities to include heavy rare earth elements. The installation of two new furnaces for processing terbium (Tb) and dysprosium (Dy) represents a major step in supporting applications like high-strength permanent magnets used in EV motors, wind turbines, and defense technologies.”
Molten salt electrolysis for rare earth alloys
LCM’s technical team is pushing the boundaries of rare earth molten salt electrolysis, exploring innovative opportunities to enhance an alternative supply chain. In one milestone, a pilot-scale trial for producing rare earth alloys with a newly designed molten salt electrolysis cell achieved an impressive 15-20% increase in energy efficiency compared to existing cells. “These findings will help LCM enhance its capabilities for reliably producing high-quality rare earth metals and alloys in the Western world, solidifying our position in the global market,” noted Riley.
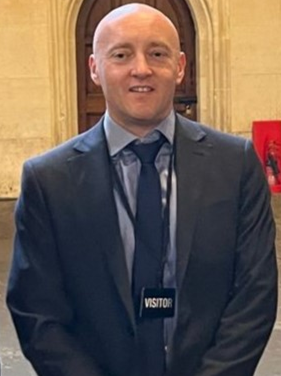
“As the only commercial facility in the west, which is free from far eastern restrictions and linked ownership for the production of heavy rare earths by molten salt electrolysis, LCM has a variety of opportunities. We are currently expanding our Nd/NdPr metal production from a 2-cell operation to a 6-cell operation in the UK. This expansion will increase our capacity from 55 tons per cell per annum to a total capacity of 330 tons per annum to meet rising demand. The innovations in our electrolysis process, driven by LCM’s newly bolstered technical department, will lay a solid foundation for future expansion in the sustainable production of rare earth metals and alloys.”
According to Riley, LCM is the only commercial facility outside of China and not Chinese-owned producing neodymium metal and neodymium praseodymium master alloy by molten salt electrolysis. With its samarium cobalt alloy production side, LCM is the only company worldwide operating the co-reduction process.
The company commercially produces both Nd and NdPr metal via fused salt electrolysis, and all material manufactured since 2017 is processed using alternative supply chain material. Since 2017, LCM has had the capacity to commercially produce over 120 tons per year of high-quality Nd and NdPr metals. Today, it can process and produce over 100 specialty alloys serving diverse industries including even the growing demand for hydrogen storage applications.
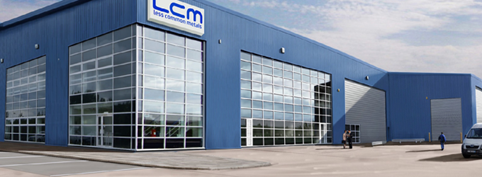
“Despite the significant challenges in progressing molten salt electrolysis for rare earth elements from lab-scale (TRL 4) to deployment and operational stages (TRL 9) outside of China, LCM has successfully demonstrated its capability to overcome these obstacles,” adds Manu Kaimanikal, senior metallurgist. “This achievement is attributed to continuous innovations in the electrolysis process, combined with the expertise of our highly skilled operators. As a result, we have achieved the production of rare earth alloys with enhanced process efficiency.”
Leading magnet recycling collaboration
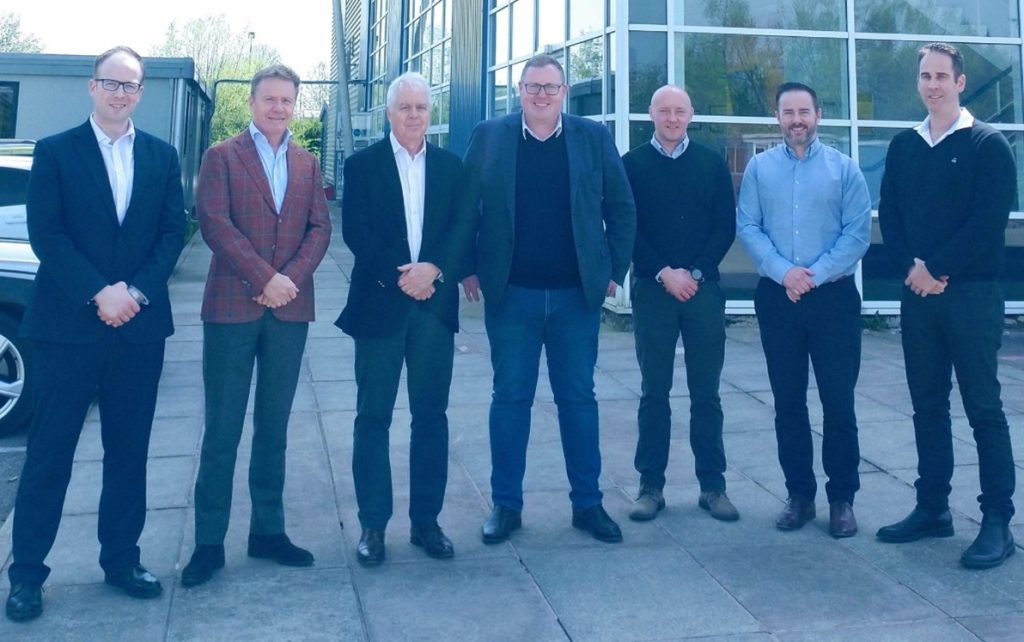
In another effort, LCM is leading an “industrial scrap-to-magnet” government-funded initiative in collaboration with Ionic Technologies and Vacuumschmelze. As earlier reported in Magnetics Magazine, the forward-thinking project aims to produce high-quality NdFeB magnets using 100% recycled heavy and light rare earth elements with full traceability. The REEVALUATE project (Rare Earth Elements recovery from industrial scrap produced during grain boundary diffusion of permanent magnets) focuses on reclaiming valuable rare earth elements from pre-consumer industrial scrap, an underutilized resource that accounts for 36% of valuable rare earth content during magnet manufacturing and material processing stages.
VAC’s role is to provide pre-consumer magnet scrap. Ionic will convert it into high purity rare earth oxides at their newly developed demonstration plant situated in Belfast. The oxides will then be supplied to LCM, who will reduce the oxides back to rare earth metals and alloys, tailoring them to VAC’s specifications for producing new magnets. In a truly circular process, any byproduct scrap generated during LCM’s material processing will be sent back to Ionic Technologies for further refining, ensuring that no valuable material is wasted, establishing a closed-loop system.
“LCM is proud to be leading the project in partnership with Ionic Rare Earths and Vacuumschmelze,” commented Riley. “By advancing a fully traceable, circular supply chain, we are not only addressing the growing demand for rare earths driven by clean energy technologies but also exploring an alternative route for sustainability in the industry.” For more info, see www.lesscommonmetals.com.