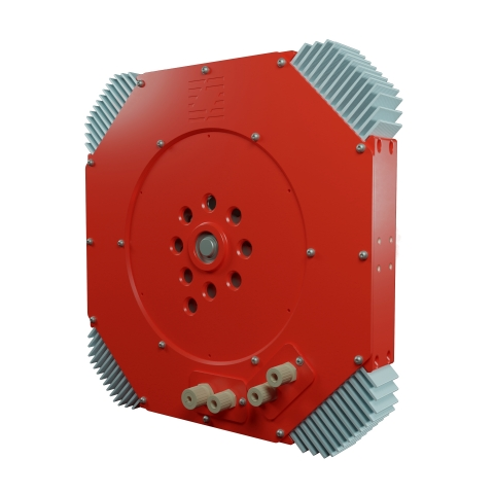
Infinitum Electric, developer of an innovative axial-flux electric motor that relies on printed circuit board electronics instead of traditional wound copper coils, has launched as its first product a 15-hp motor to power HVAC equipment.
Armed with fresh venture funding, an initial roster of impressive OEM customers and a newly hired slate of blue-chip executives, the three-year-old startup aims to eventually move up the horsepower ladder to supply its motors to manufacturers of bigger products including electric vehicles.
Its new IEx Series motor, shown above, is a third of the size and weight of conventional designs while delivering class-leading efficiency and IoT capabilities, the company says. It has reached OEM sales agreements with three leading equipment makers – Twin City Fans, Comefri and ACME fan. The first shipment of motors is scheduled for June. It plans to release 10 hp and 5 hp models by the end of the year, while pursuing research and development efforts in other market segments such as oil and gas, aerospace and electric vehicles.
“With the launch of our IEx Series motor, we are delivering a smaller, smarter, quieter, lighter and higher performing motor into the roughly $150 billion yearly electric motor market,” said Ben Schuler, CEO. “After the electric motor has gone virtually untouched for more than 100 years, our product is generating exciting interest in key industries, and we’re honored to introduce our first product line with three of the industry’s top fan and blower OEMs.”
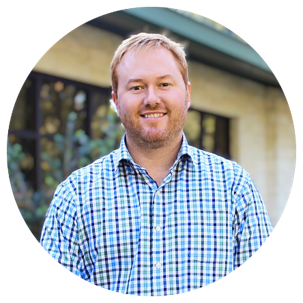
“Infinitum Electric’s fresh approach to ECM motor development is unique in the commercial HVAC industry,” said Sylvie Braun, COO of Comefri. “At the same time, we are certain, as a leader in global fan design, Comefri USA’s close collaboration with Infinitum Electric will provide distinctive leadership in the American commercial HVAC marketplace for years to come”
“Infinitum is bringing the electric motor into the 21st century” said Jeff Robinson, vice president of engineering applications at Twin City Fans, “and we’re thrilled to incorporate Infinitum advantages into our fan designs that will be more compact, lighter weight, more efficient and have easy speed control. This will give our customers the competitive advantage that we’re excited about. We are striving to bring the most efficient solution to our customers, and Infinitum helps us do exactly that.”
“Partnering with Infinitum aligns with our commitment to quality and performance,” said Lee Buddrus, president of ACME Fan. “Not only does Infinitum offer unique performance advantage by being smaller, lighter and more efficient, their motor insulation provides fundamental change in quality and durability.”
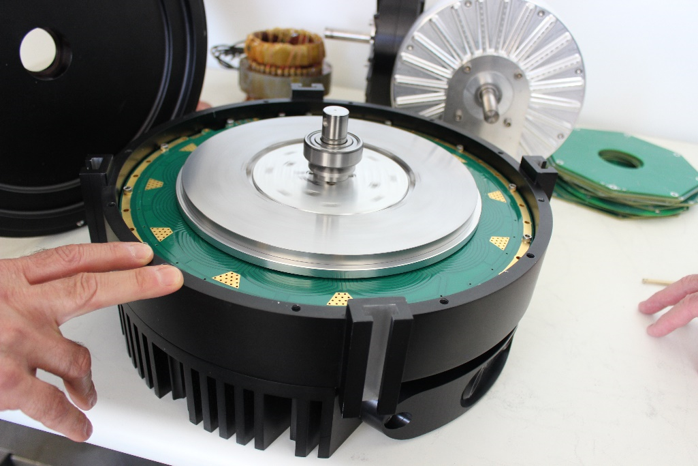
The Technology
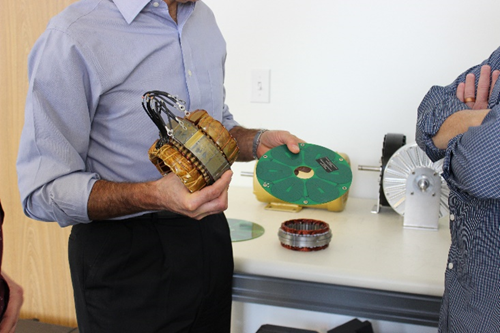
According to Infinitum, the inherent advantages of its machine topology are due to several key aspects. The weight of a PCB stator is less than 10% of the weight of a similarly rated conventional iron core wound stator. The PCB stator can support current densities between 3 to 4 times higher than a conventional stator under the same cooling conditions. Rotor eddy current losses are negligible as the magnetic flux, as seen by the magnets and back iron, is constant, therefore these machines have very high efficiency across a wide range of power and speeds.
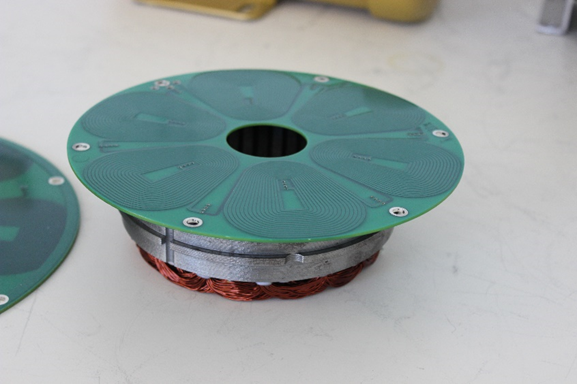
The PCB construction enables a compact and thin stator structure minimizing the effective airgap, and therefore the magnet mass of the machine. PCB stators are consistently built void-free using a mature and repeatable process independently of operator skills or experience, so under the same voltage and temperature conditions, PCB stators last up to ten times longer than equivalent copper windings.
The motor’s PCB-based stators with etched copper wiring eliminate the need for traditional motor stators made with twisted copper wiring. This means that machinery designed to automate the twisting of the copper wires can be eliminated from the motor manufacturing process and replaced by fabless, fully automated PCB manufacturing. This major shift in the process drastically simplifies motor manufacturing and significantly reduces the cost to make each motor, notes Infinitum.
Wire windings and iron laminations are eliminated by etching copper conductors into a printed circuit board. Weight reduction on the component level is as high as 90% and the machine level can be up to 50% lighter weight. Optimized magnetic configurations improve power density even further.
The core-less motor provides high performance at high speeds by eliminating hysteresis loss found in a conventional stator core. Removal of the conventional laminated stator core significantly reduces core losses, decreases cogging and torque ripple and increases efficiency. Identical copper conductors allow electrical losses to be easily controlled and provides high power density by optimizing copper layout.
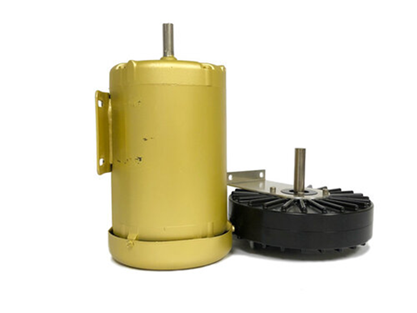
With the iron removed and attractive magnetic forces eliminated from the machine, structural requirements are also reduced significantly. Further, the continuous coil design in the PCB stator optimizes coil geometry, providing maximum power density and efficiency at a fraction of the size and weight. Current density can be more than four times higher than machines with traditional iron laminations and copper windings, says the company, substantially reducing the copper mass for the same current rating. The company’s design algorithm allows it to design and produce stators with virtually any dimension, so motor diameter and length can be increased or decreased as desired.
Another attribute which Infinitum cites is that acoustic noise is low due to the absence of normal magnetic forces acting between the rotor and the stator and negligible torque ripple due to the absence of reluctance torque. The normal magnetic force in an axial flux electric machine is perpendicular to the rotor surface, analogous to a radial magnetic force in a radial flux machine. Iron core electric machines typically have some torque pulsations due to the variations in the reluctance as the rotating magnetic field travels around the motor. In the airgap of an iron core machine, the position of the rotor relative to stator is such that the magnetic flux produces a magnetic force in the same direction of rotation of the machine. The magnetic force acts in such a way as to reduce the reluctance of the magnetic path. As the rotor moves in the direction of rotation, the alignment of the rotor poles changes relative to the stator to a point where the magnetic flux produces a force in the opposite direction of rotation. This alternating magnetic force will produce a torque ripple. The Infinitum motor, however, does not have an iron core or slots, so the distribution of the magnetic flux across the airgaps and stator remains constant and the machine rotates without any pulsating magnetic force acting on the rotor.
The company
Based in Round Rock, TX near Austin, Infinitum was established in 2016. Fresh funding to fuel its growth came in December in the form of a $12.5 million Series B round of financing. This followed a Series A round completed in January, bringing total funding to $15.2 million. The Series B round was led by Cottonwood Technology Fund and includes participation from Chevron Technology Ventures, AJAX Strategies and individual investors.
“Our patented circuit board stator is what sets us apart and positions us well for success, not just in the HVAC space, but for a variety of applications,” said Schuler. “Our motor technology provides superior advantages for companies looking for improved performance. The electric motor market is a $150 billion industry annually, over a century old, and many markets within the industry are trying to consume and create power more efficiently. Some markets, like electric vehicles, are in the process of electrifying completely.” The company holds six patents currently and has a further 15 pending. “Our patented motor technology will completely transform the electric motor market, a market that has changed very little since inception more than 100 years ago.”
“Since participating in the Series A round in December, we’ve seen Infinitum advance tremendously. They’ve added key leaders to the team, signed multiple customer contracts and are prepared to ramp their own manufacturing facility,” said Dave Blivin, managing director for Cottonwood. “We’re proud to have led the Series B round, and we’re excited to see Infinitum attract the support of leading investors who will further enhance their success in the growing electric motor industry — one that is ripe for the type of disruptive innovation Infinitum provides.”
“Infinitum’s mission aligns well with our goals for the Future Energy Fund,” said Barbara Burger, president of Chevron Technology Ventures. “The purpose of the Future Energy Fund is to invest in breakthrough energy technologies that reflect Chevron’s commitment to lower emission energy sources and that are integral to low-carbon and efficient value chains.”
In August, the company announced three senior executive appointments as it opened its new headquarters and manufacturing facility. Michael Gray was named senior vice president of supply chain and manufacturing, alongside Paulo Guedes-Pinto as vice president technology and Tracy Gill, formerly with Raytheon, as director of engineering.
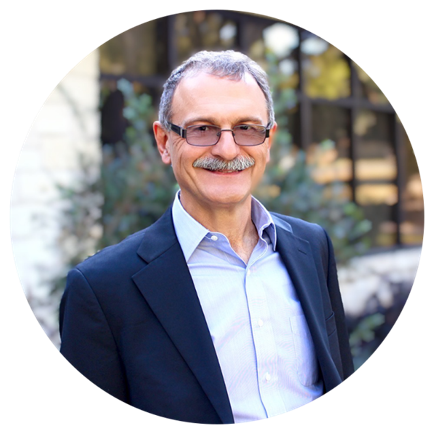
Guedes-Pinto has over 27 years of experience in the design and manufacture of large AC and DC motors, traction motors, axial flux permanent magnet machines, high-speed permanent magnet motors for subsea and land applications, as well as medium voltage drives. Before joining Infinitum Electric, he held engineering and R&D leadership positions at TECO-Westinghouse, Boulder Wind Power, FMC Technologies, GE Canada, JDS Uniphase and Indústrias Villares which is now Gevisa, a GE company. He holds nine patents related to electric machines and drives.
In March, Infinitum hired Mark Preston as chief operating officer. He has served in executive roles at GE, Northern Power Systems, Glacier Bay, MegaWatt Solar, Vestas, Innovus Power and, most recently, Array Technologies, a manufacturer of solar tracking systems, where he as the vice president of engineering.
For more info, see www.infinitumelectric.com. For more news about axial flux motors, go to www.MagneticsMag.com and query “axial flux”.