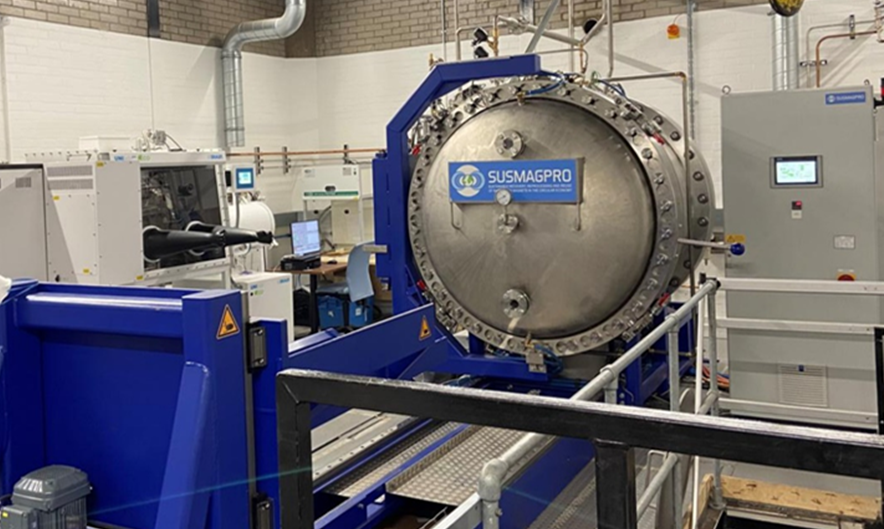
A process employing hydrogen is promising relief to one of the vexing problems in recycling rare earth magnets from electronic and automotive waste streams. The standard process involves shredding the metal parts of computer disk drives, speakers and electric motors. Unfortunately, the contained NdFeB magnets break up into a friable magnetized powder which then sticks to the ferrous scrap and the shredder itself. A production-scale plant in Germany planned to go onstream in 2024 and a pilot plant launched a few months ago in the UK, expected to graduate to production-scale in 2023, are using the hydrogen-enabled process in efforts to commercialize it.
At the center of both efforts is HyProMag Limited, closely tied to the University of Birmingham and an outgrowth of research conducted there. In November, its German subsidiary HyProMag GmbH was awarded a €3.7 million grant to establish a production facility in Baden-Wurttemberg. The first phase is to reach a minimum capacity of 100tpa NdFeB comprising recycled rare earth sintered magnets, alloy pellets and powders. The initial production facility would be a similar size to a £4.3 million project being developed by HyProMag and the University of Birmingham at Tyseley Energy Park in the UK.
The German plant will be the first in that country using the process, with first production targeted for 2024. Total cost of the project is expected to be €6.1 million, about 60% funded by the grant. HyProMag GmbH is 80% owned by HyProMag Ltd and 20% owned by Professor Carlo Burkhardt of Pforzheim University, coordinator of the €14m SusMagPro and €13m REEsilience EU funded recycling projects with approximately 40 partners across the European supply chain.
Hydrogen Processing of Magnet Scrap
Key to the design of the plants is a patented process developed at the University of Birmingham which uses hydrogen to liberate and break down the used magnets into an alloy powder for remanufacture. Called HPMS (Hydrogen Processing of Magnet Scrap), it is based on the hydrogen decrepitation process developed in the Magnetic Materials Group at the university by the late Professor Rex Harris. It was first tested in the laboratory using an old washing machine drum to extract the rare earth alloys from products such as hard disk drives, speakers and electric motors and separate it from other bits of plastic and metal surrounding the magnet.
The HPMS process has been exclusively licensed to HyProMag, which will be one of the facility’s primary industrial users, helping to operate the plant and establish the supply chain. The extracted NdFeB powder is in the form of an alloy which can be re-processed into different forms which can be sold back into the supply chain for rare earth magnets.
HPMS offers an extremely efficient method to extract magnets from end-of-life waste streams as a pure NdFeB alloy powder with a very low environmental footprint. Products for recycling are exposed to hydrogen at atmospheric pressure and room temperature. The NdFeB magnets break apart and, crucially, the powder which is generated is demagnetized which makes it easier to extract. The nickel coating peels away from the surface of the magnets and this can be separated using mechanical means. The extracted NdFeB powder is of a purity whereby it can be reprocessed into new magnetic materials or rare earth alloys.
Pilot plant launched at University of Birmingham
Following initial successes, the technology was recently scaled up to the pilot scale. The pilot facility has received significant funding via the EU Horizon 2020 project SusMagPro, one of the largest magnet projects in Europe. In the pilot facility, a 1,200-litre pressure vessel is able to process up to 100kg of magnets per day.
Crucially, the resulting powder is de-magnetized during this process, so can then be refined further before going through a pressing and sintering process, in which the reclaimed materials are compacted and heated to form new magnets. In doing so, this process uses 88% less energy to create magnets when compared to virgin sources and will offer the only indigenous source of sintered rare earth magnets in the UK. The recycling pilot will process scrap from a wide variety of sources including hard drives, speakers, wind turbines and electric motors.
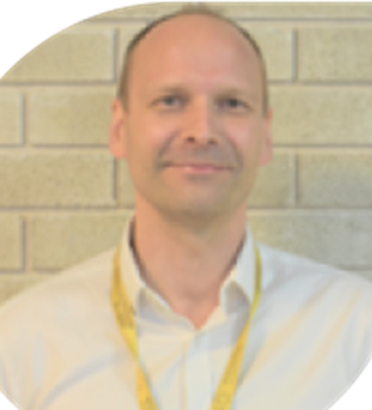
The pilot plant in Birmingham was launched in September. “This pilot plant paves the way for the UK to take a leading role in high performance magnet recycling. Alongside the technologies and equipment, we have developed, is a wealth of industry and research expertise. These partnerships form a solid foundation for this new industry to succeed, said Professor Allan Walton, co-director of the Birmingham Centre for Strategic Elements & Critical Materials at the University of Birmingham. He is also a founding director of HyProMag.
“It is vital to develop processes to ensure a sustainable supply of these materials and reduce dependency on virgin mined metals. As less than five per cent of end-of-life magnets are currently recycled, this is a key process that can begin to address the global shortfall in magnet manufacture.” Automotive companies participating in the project, include Jaguar Land Rover and GKN. One of the efforts is to recycle speaker assemblies from hard disk drive scrap for a subsidiary motor application for a Bentley vehicle.
The plant is an important step towards opening the UK’s first full scale remanufacturing facility at Tyseley Energy Park, to be completed in 2023. The pilot and full-scale facility have received a share of £33m funding from UK Research and Innovation’s Driving the Electric Revolution Industrialisation Centres, established to support the UK in becoming a center of excellence and innovation in power electronics, machines and drives.
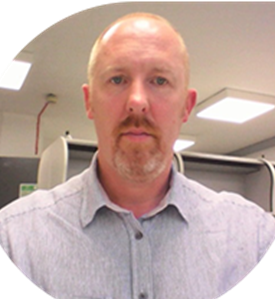
“This pilot plant enables us to demonstrate not only the potential of the HPMS process, but how efficient the end-to-end production line can be. It will also enable us to refine and streamline the production line ahead of launching our full-scale facility at Tyseley. The plant will produce rare earth alloy powders which can be fed into any part of the rare earth value chain,” said Nick Mann, operations general manager of HyProMag.
Another key player is Mkango Resources
HyProMag is commercializing HPMS technology with the support of UK and Canadian listed Mkango Resources, a major shareholder. Mkango’s corporate strategy is to develop new sustainable primary and secondary sources of neodymium, praseodymium, dysprosium and terbium to supply accelerating demand from electric vehicles, wind turbines and other clean technologies in an integrated mine, refine and recycle strategy.
It is developing a rare earths mine in Africa, named Songwe Hill in Malawi. Another effort is a collaboration with Grupa Azoty Pulawy, Poland’s leading chemical company and the second largest manufacturer of nitrogen and compound fertilizers in the European Union. The two companies have agreed to work together towards development of a rare earth separation plant at Pulawy to process the purified mixed rare earth carbonate produced at Songwe Hill. Through its ownership of Maginito, it holds a 42% interest in HyProMag with an option to increase its interest to 49%.
“This is an exciting milestone for Mkango, HyProMag GmbH, HyProMag Limited, which significantly enhances the group’s production pipeline, targeting first production in the UK in 2023 and Germany in 2024, with North America developed in parallel,” said William Dawes, CEO, upon announcement of the German facility. “We envisage that the recycling of rare earth magnets will play a key role in the development of robust supply chains to catalyse and support growth in the electric vehicle sector and in other clean technologies. “This project further cements Mkango’s and HyProMag’s early mover advantage in the rare earth magnet recycling sector, highlighting its competitive position and benefiting from a very strong network of industry and academic partners.” For more info, see www.hypromag.com, www.mkango.ca, www.birmingham.ac.uk and www.susmagpro.eu.