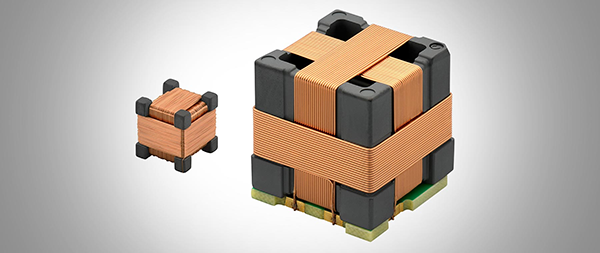
Applying its expertise with highly permeable ferrite material, Neosid has developed innovative new isotropic 3D antennas for electromagnetic tracking systems in devices for various industries such as gaming, logistics, maintenance, and medicine. Using a transmitting antenna, shown on the left, and a receiving antenna, shown on the right, the systems can accomplish six directions of accuracy making them suitable for advanced virtual reality tracking by collecting information on the position of an object in three-dimensional space.
“These antennas result from a combination of our expertise in the development and manufacturing of customized ferrites by injection molding as well as of electronic components,” said Yilmaz Benzer, managing director. “Providing virtual information for technology of the future, they are increasingly being used to collect information on the position of an abject in three-dimensional space. They use the data acquired to add virtual information to processes.”
One of the company’s innovations is its use of a highly permeable ferrite material with a specific resistance of approx. 106 to 107 mΩ. This allows direct winding without an insulating coating. Components made of the material are highly versatile and can be used in RF, antenna and interference suppression technology as well as for proximity switches, transponders and other electronic components.
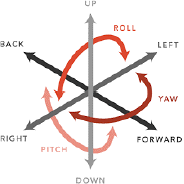
Many positioning systems rely on GPS navigation where two coordinates define the position in a plane. For the description of the object height, an additional piece of information is needed to yield 3D data. If this data is supplemented with information on the orientation of the object, the result is 6 directions which describe the freedom of movement of an object in three-dimensional space, referred to as 6 degrees of freedom (6DoF).
Antenna core
The systems are based upon ferrite core antennas. The three coils on the antenna are oriented at right angles to each other. The cube shape of the antenna offers isotropic properties during transmission and reception in the x-, y-, and z-axes.
“We utilize a special manufacturing process to form modern ferrite materials into any required three-dimensional shape,” explains Benzer. “We use this to create a hollow ferrite core for our 3D cube antennas. Compared to a solid ferrite core, this significantly reduces the weight of the component —while retaining the efficiency of the antenna. Our one-piece antenna cores offer the greatest degree of resistance against mechanical influences because we keep the number of components used low.”—thereby also doing our part for a sustainable environment.
Alternatively, Neosid also designs isotropic antennas without a ferrite core which are made of three air-core coils put together. This design variant is particularly important for applications in which magnetic materials are not to be used, such as in certain medical systems.
“Our proficiency in advanced manufacturing methods allows us to design 3D cube antennas such that they can be manufactured optimally in an automated production process,” notes Benzer. Metallized areas on the ferrite core serve as contact surfaces for the individual windings as well as for contacting the entire component on the circuit board.
The process-optimized ferrite core makes it possible to automatically wind the antenna. The wire thickness, number of windings, and winding position can be individually adapted to the requirements of the application, and the coil wire can be attached reliably to the component.
Vertical integration at Neosid is an important factor. The design, the creation of the production tools and the manufacturing of the ferrite cores for the antennas take place in Germany. Modern, robot-controlled production equipment is used for the winding processes and the company exercises continuous quality control and advanced production methods along the entire manufacturing process.
Advantages of magnetic sensor systems
Magnetic sensor systems have several advantages over corresponding methods such as camera-based optical or mechanical systems using gyroscopes or gyrostats, explains Benzer. For example, they do not require direct visual contact, which means they work amidst surrounding obstacles and can be operated in a wear-free manner. Optical systems are generally based on complicated and time-consuming image processing methods which require fast processors. Furthermore, the data that can be collected is limited to the visible environment which can be captured by the camera system. Mechanical systems have a complicated design and are subject to natural wear and tear, which limits their service life.
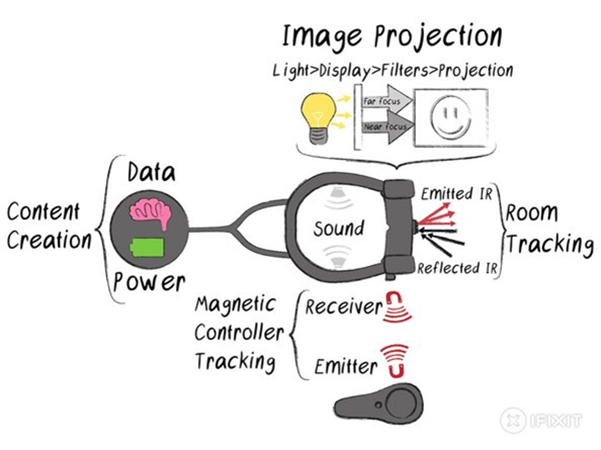
Electromagnetic tracking systems generally require two components. A transmitting and a receiving antenna. The magnetic waves generated in the transmitter induce voltages in the receiving antenna which are forwarded to the microprocessor-aided evaluation unit. The antennas each possess three orthogonally oriented coils for generating, or collecting, information in all three spatial axes. If these coils contain identical electrical and geometric properties, this corresponds to an isotropic antenna design. Such a unit shows advantages in the evaluation of signal information, as the transmitted outgoing and incoming signals can be related directly to each other. When these properties are bundled, the result assumes the shape of what is called a 3D cube antenna.
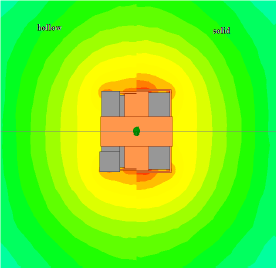
Simulation is an important step in the product development. Technical requirements with regard to inductance, sensitivity, operating frequency, and additional parameters determine the design of 3D cube antennas. Comprehensive simulations are performed as part of the design process.
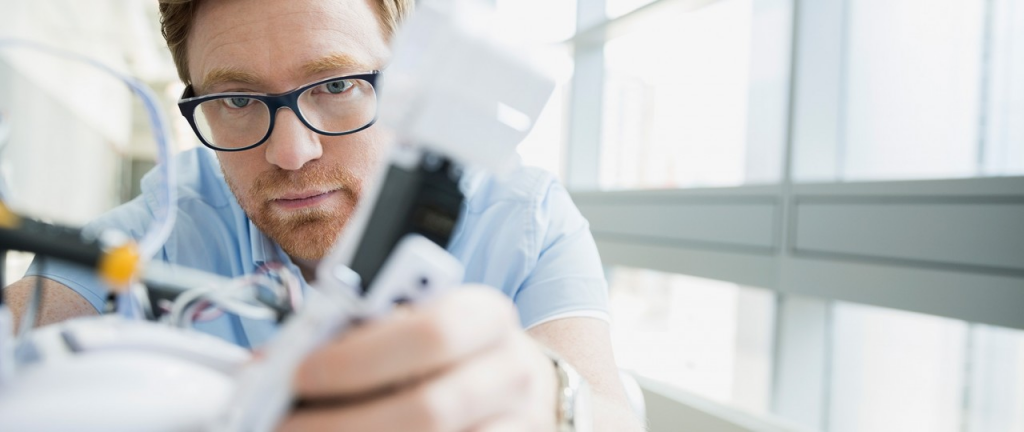
Based in Halser, Germany, located east of Dusseldorf and Cologne, Neosid specializes in the design and manufacture of small custom electronic components, many using its expertise with permeable ferrite and inductance. The company has about 90 staff. For more info, see www.neosid.de.