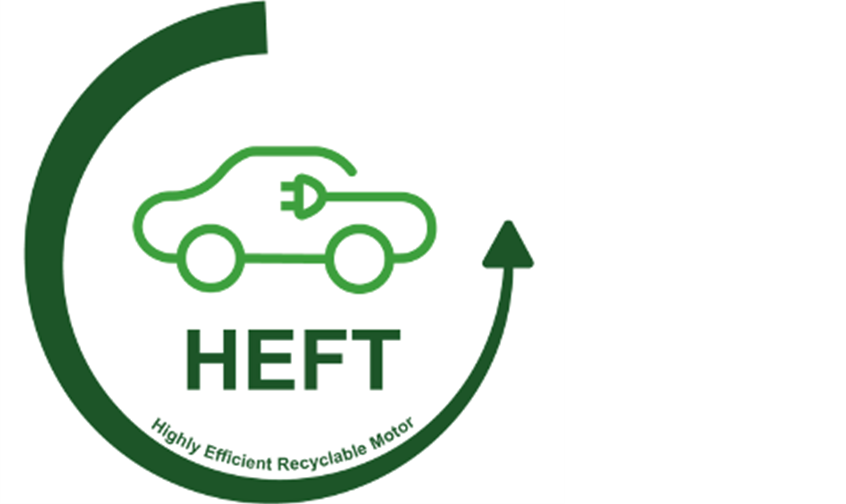
A €4m research and development program to develop a lower cost, more efficient and power dense permanent magnet e-motor for electric vehicles is being funded by the European Community. Inspired by ambitious sustainability objectives, the program is led by Mondragon University in Spain. Among the consortium are leading e-drivetrain manufacturer GKN Automotive and innovative magnetics company Magneti Ljubljana which, separately, recently put on the market a novel magnetic filament that enables three-dimensional printing of bonded magnets.
The consortium of eight European partners are focused on a circular strategy for rare earth critical raw materials in the motor to be implemented through design and material innovation that can be applied to mass production of next-generation electric vehicles. The innovations aim at allowing magnets in the motor to be smaller in size, contain less rare earth material, also be eligible for reuse and recycling.
Welcome to the 2023 Sustainability Fest of Magnetics Magazine!
Stay tuned for more in the November/December issue.
Participate: Submit your sustainability content now.
A long-term circular strategy for rare earth critical raw materials is an important aspect of the effort, targeting a reduction in the use of two key rare earth materials (neodymium and dysprosium) of up to 80% and recycling more than 80% of any rare earth material used. This is intended to conserve resources and create increased resilience in the European supply chain.

Named HEFT (Highly Efficient Recyclable Motor) the project includes a total of eight partners from Belgium, Italy, Slovenia, Spain and the UK. GKN Automotive, a supplier to more than 90% of the world’s automotive OEMs with more than 20 years of e-drive experience, serves as a key industrial partner for manufacturing and assembly, and ensuring the final motor design meets industry needs and requirements. All the work from GKN Automotive will be carried out from its facility in Zumaia, Spain.
Magneti supplies the key magnetic material for the project. Another industry participant is Sumitomo Bakeline Europe’s High Performance Materials (SBHPP) business whose factory in Ghent produces Vyncolit thermoset molding compound. Other partners in the consortium are Ikerlan, the University of Nottingham, the University of Bologna and KU Leuven.
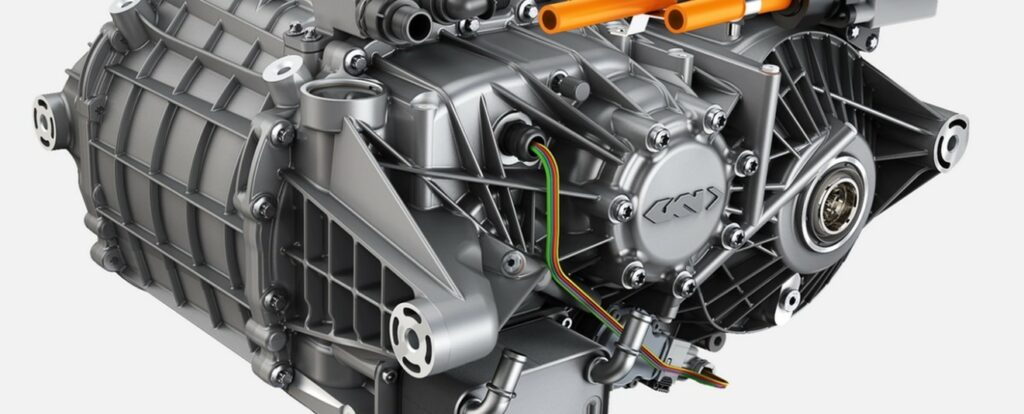
“The HEFT project is an exciting opportunity to develop the next generation of eMotors that will be more sustainable and efficient, while costing less to manufacture,” comments Aitor Tovar, senior global manager of eMotor development at GKN Automotive. “I believe development in these areas is key to the future of electric mobility so I’m delighted that we can contribute our expertise in eDrive innovation as an industrial partner, helping to meet an industry need.”
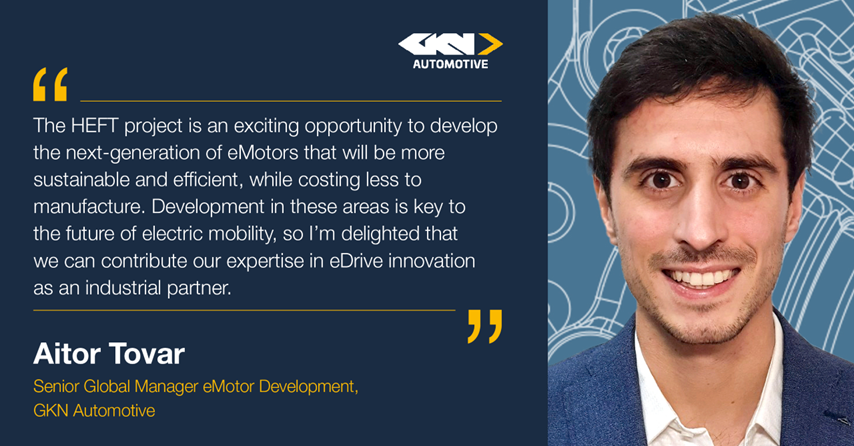
“Minimising the environmental impact of manufacturing, particularly through a reduction in the use of rare earth critical raw materials, is an essential consideration in the development of future products, so the implementation of a circular economy strategy is another key motivation in our participation in this project.”
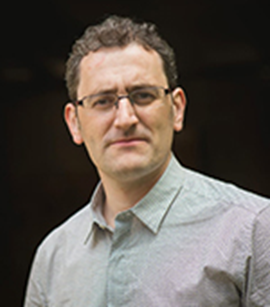
HEFT considers that an energy-efficient rare-earth synchronous motor is the best option for next-generation high-power primary axle traction EVs and proposes a set of innovation challenges on electric synchronous motor configuration based on SiC inverters (direct cooling of rotor and stator, advance insulation for high voltage, multibarrier rotor topology, wave windings) and advanced materials such as grain boundary diffusion (GBD) magnets, epoxy for magnet fixation, composite for motor housing and insulation resin.
The work will be validated against two motor topologies. Compared to two main reference automotive IPM commercial motors in Europe, the VW ID.3 and FIAT500, objectives for the project motor are to achieve >800V, 20% reduction losses, >7 KW/kg and 42kW/l power density, 28% cheaper, 50-66% material savings, including 60% reduction of REE content and >80% REE recyclability rate.
As this solution is still dependent on REE from China, HEFT is aligning with the European Raw Materials Alliance (ERMA) action plan towards a circular economy market of rare earth permanent magnets and suggests one circular economy-based alternative magnet route and two REE recycled routes together with policies promotion towards the foundation of a European rare earths industry, capable of delivering 20% of EU demand by 2030.
Eight work projects are planned to implement the concepts where five research partners are tasked with developing innovative ideas around the design-to-x approach, while the three companies assure the results have a clear market orientation and fulfill the industry needs. HEFT plans to organize OEM workshops to ensure wide adoption of the solutions, also with policymakers to promote regulations towards the EU circular market that would help maintaining the leadership of EU companies, while increasing their competitiveness and job opportunities linked to the new circular business models.
Magnetic filament for 3D printing of bonded magnets
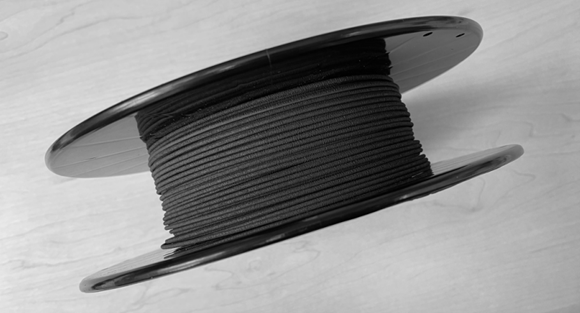
Separate from the HEFT project, Magneti Ljubljana recently announced that it has developed its novel magnetic filament and now has begun selling it. The filament can be used to produce bonded magnets on conventional FDM/FFF 3D printers. It enables 3D printing of bonded magnets of complex shapes with magnetic properties comparable to the properties of injection-molded plastic magnets.
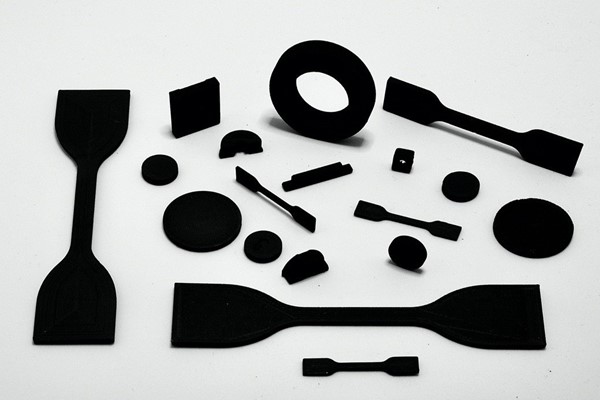
The company displayed its products at the SIA Powertrain Congress for automobile engineers held in June 2023 at Port-Marly, France. A leading venue for the automotive technology community in Europe, this year’s meeting devoted considerable attention to sustainability issues.
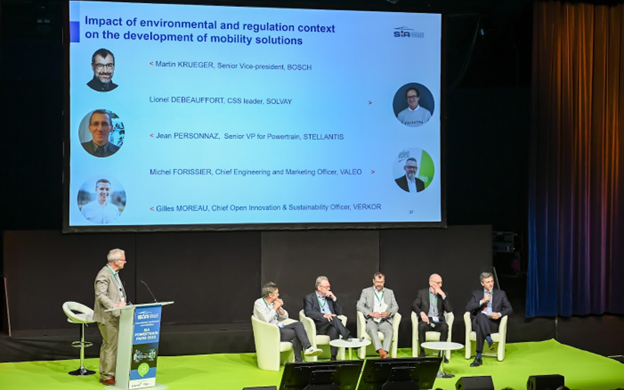
For more info, see www.heftproject.org, www.gknautomotive.com, www.magneti.si, www.sia.fr.