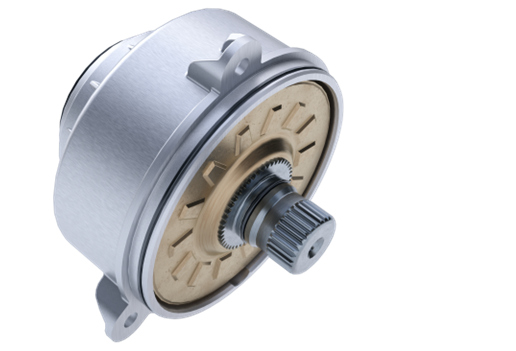
Something special happened in EV innovation when Burgess-Norton and Means Industries joined forces under the umbrella of Amsted Automotive. Now, eliminating complex hydraulic systems by repeated magnetic latching, Means has developed a revolutionary e-axle for electric trucks and SUVs.
The breakthrough came by combining the design, engineering and manufacturing prowess of Burgess-Norton with the electro-mechanical and advanced metal-forming expertise of Means. The Dynamic Controllable Clutch (DCC) technology and accompanying Electro-Mechanical E-axle Disconnect solution allow driveline systems to engage and disengage the rear electric drivetrain from the drive axle efficiently while at the same time conserving energy.
DCC uses electric actuation to create substantial packaging and system efficiencies, eliminating complex hydraulic systems by magnetically latching in each state. The process significantly reduces the energy requirements to keep AWD and 4WD systems engaged, enabling shift times of less than 20 milliseconds and extending EV range for electric trucks and SUVs by up to 20%.
The upshot? Electric AWD and 4WD vehicles now have greater on-demand performance, with enhanced efficiencies during on-road and off-road conditions. The system is already by adopted by vehicle manufacturers. Recently, a cutting-edge electric 4WD producer needed to improve range on its 4-motor application. Amsted added two of their disconnect modules to the units that ultimately improved efficiency by 10% while concurrently adding performance characteristics such as individual controls.
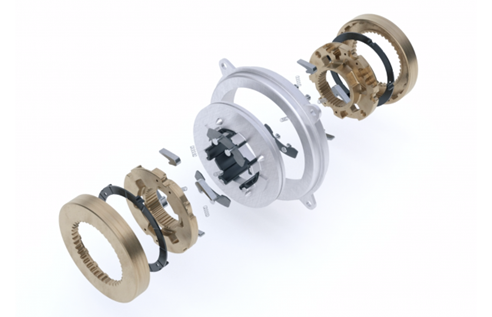
In 2021, Amsted Automotive Group which is based in Chicago brought together Means and Burgess-Norton to form a new and innovative technology team. The combination yielded an expanded global presence with 16 facilities in North America, Asia and Europe to serve the automotive industry with a robust manufacturing footprint, producing over 100 million components and assemblies annually.
The group has aligned the combined design and engineering expertise, and manufacturing capabilities, to build leadership in advanced metal-forming and powder metal manufacturing with electro-mechanical clutch design capabilities for electrified propulsion solutions, building on Amsted Automotive’s role in automatic transmissions.
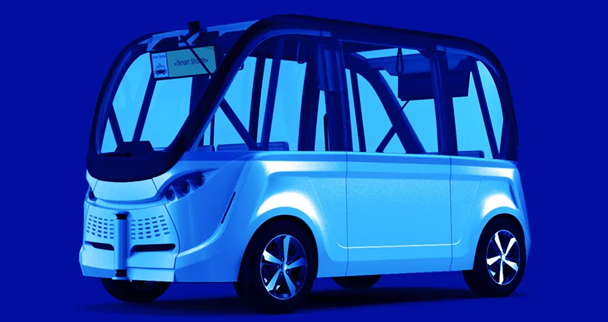
Now, Amsted provides a range of products for e-mobility and electrified propulsion for auto manufacturers. Among the lineup are products such as e-axle and wheel-end disconnects, differential disconnect system, multi-speed shifting, regenerative braking, electric motor components and net-formed components for gear boxes and e=axles. See www.amsted.com.