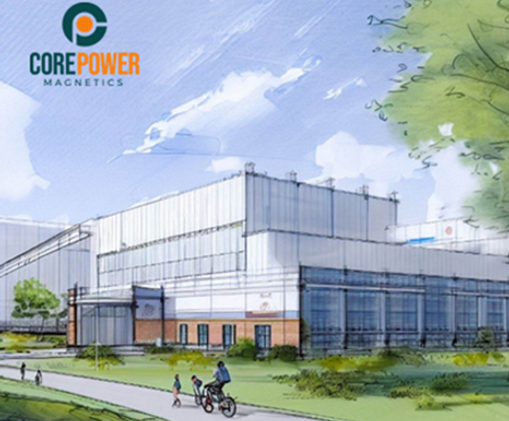
CorePower Magnetics, building upon soft magnetics technologies invented at Carnegie Mellon University and the National Energy Technology Laboratory, is planning to establish a plant in Pittsburgh to manufacture its signature nanocrystalline magnetic cores and power electronic components made from them – and has been awarded key quality certification.
- In November it was selected for $20 million in funding from the U.S. Department of Energy’s Office of Manufacturing and Energy Supply Chains to launch a state-of-the-art domestic manufacturing facility.
- In late January, it received certification to ISO 9001:2015 Quality Management System standard as recognized by Performance Review Institute Registrar. A testament to the company’s commitment to quality and excellence, and dedication to continual improvement of their management system, the certification is an important hallmark for gaining business from top industry players.
By reusing a former industrial site, the new facility aims to onshore production and strengthen supply chain resilience for electric grid infrastructure and electric vehicles. Finished power electronics components including motors, inductors and transformers are planned to be produced at the plant employing the company’s nanocrystalline magnetic cores through a scalable, in-line manufacturing processes.
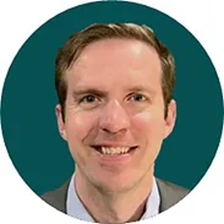
“This facility secures a reliable domestic source of high-performance alloys and components currently dominated by foreign supply chains,” said Dr. Sam Kernion, CEO. “Teaming our innovative solutions with the region’s renowned metals manufacturing legacy and skilled workforce, we will build the manufacturing backbone needed to upgrade critical infrastructure across America’s energy economy,”
The manufacturing facility will contain an advanced metals casting line to mass produce advanced amorphous and nanocrystalline alloys, in addition to component production lines for motors and high frequency transformers and inductors. CorePower’s specialty magnetic grades upgrade legacy systems like distribution transformers while enabling emerging compact and thermally stable components for EV powertrains, EV fast chargers and renewable energy integration, says the company.
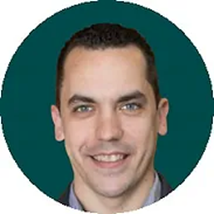
“By repurposing legacy infrastructure in Pittsburgh, we can leverage existing assets to drive innovation and the local economy,” explained Dr. Paul Ohodnicki, CTO. “This support from the DOE will be transformational as we work to meet surging demand for U.S.-made technologies enabling vehicle electrification and modernized power grids.”
With integrated manufacturing scaled to supply 10,000 tons annually, CorePower targets a 20% expansion of current domestic capacity alongside meeting 10% of global demand for the specialized magnetic metals. Its new class of metal amorphous nanocrystalline FeCo and FeNi alloys have material properties that can meet demanding applications while providing flexibility and control in engineering the magnetic core properties in our products, says CorePower. The process transforms amorphous metal ribbon into spatially tuned, high-performance magnetic cores.