By Dr. Tom Murray, Marc Barmeier, Stephen Tuckwell
Elantas PDG, Inc.
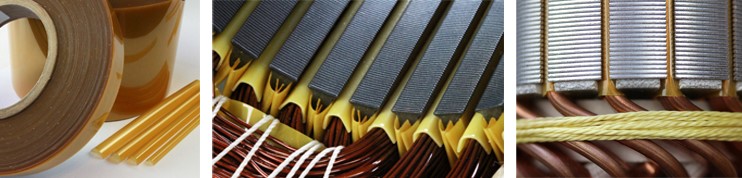
Introduction to Flexible Electrical Insulation
The application conditions for any piece of electrical equipment can be extreme. It is therefore vitally important that insulation systems for motors, generators and transformers are designed around the most critical conditions. The right selection of insulating components including Flexible Electrical Insulation for the various voltages and temperature classes is paramount to the integrity of the electrical equipment.
Flexible Electrical Insulation layers protect insulated wires from coming into contact with steel cores, hold wires in place, and provide a phase-to-phase barrier. To protect the conductor and insulation structure against mechanical, electrical, environmental and thermal stress, the whole winding is then consolidated using a compatible resin system. Typical Flexible Electrical Insulation applications are slot liners, phase insulations, wedges and slot closures.
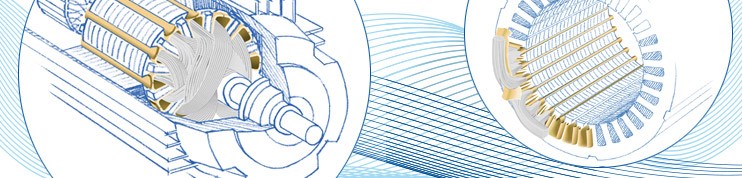
ELAN-Film HT-180
ELAN-Film HT-180 is the debut product solution in a new Elantas product family, which expands the potential of flexible insulation compared with conventional laminate combinations. It is an innovative material ideally matched to the performance required while operating at temperature ranges up to 200 degrees C, ensuring that electrical machines have a long and reliable service life. It is designed for low-voltage motors and generators to protect insulated copper from the steel core (slot liner) and where phase-to-phase insulation is required. It can easily be performed so it is excellent for use as a slot closure or in areas where formed insulation is essential and is fully compatible with a wide range of impregnating and potting resins.
Overview
Flexible materials used as electrical insulation are of three main types: papers, film, and laminate structures. Aramid fiber paper has been the industry standard for the past 50 years and has a thermal class of 200 but suffers from moisture absorption and orientation limitations. Hence, insulation technologies developed laminates with high thermal capability aramid papers on low thermal class PET films. While these products have been on the market for many years, there has been a need for technologically improved products to overcome the deficiencies of laminates, papers, and film.
The technical paper introduces a newly developed product, a composite film substrate with better electrical and mechanical properties to overcome the present limitations in laminates. This paper will cover the product description, its comparative advantages over present laminates, and the benefits for the electrical industry in total.
Flexible materials for electrical insulation
Flexible materials used as electrical insulation are of three main types: papers, film, and laminate structure. Papers are of a variety of thermal classes. Most are of low thermal index (rag, nonwoven polyester, cellulose, cotton fiber). However, aramide fiber paper has been the industry standard for the past 50 years and has a thermal class of 200. Papers have deficiencies such as poor electrical properties and low physical and mechanical properties.
The film materials available in the marketplace are of either low thermal class (polyester, PET) or high thermal class and high expense such as polyimide (PI) films. The disadvantage of the PI films is not only the high cost but also the relatively thin (12-50 micron) thicknesses available at reasonable costs.
Laminate grade flexible insulations were created to bridge the gap between the high dielectrics of the PET film with poor thermal properties and the high thermal stability of the aramide paper with low dielectric properties. The typical construction of laminate insulation is aramide fiber/PET/aramide fiber. Typically, an adhesive is necessary to hold the aramide and the PET together and is the weak link in the overall construction.
Poly (amide-imide) resins (PAI) were first commercially available as electrical insulating magnet wire coatings in the 1960s. Since this time, PAI resins are standard coatings on most magnet wire constructions used in industrial applications. Outstanding characteristics include high thermal performance, chemical and abrasion resistance, and low coefficient of friction. The use of PAI resins outside of wire enamels has been limited due to high temperature of cure and lack of physical properties due to low molecular weight of the resin. The ELAN-Film HT-180 insulation was born out of the desire to combine the PAI resin with a base film to make a flexible insulating composite material to be used in motors, generators, transformers, and other electrical devices.
Material Construction
ELAN-Film HT-180 insulation is a composite material constructed of 13 microns of PAI resin coated on both faces of varying thicknesses of PET base film. The PAI resin is specifically formulated to maintain the high thermal resistance inherent in polyamideimide resins but also to accomplish excellent film forming properties of a high molecular weight material.
The PET layer can vary in thickness from 25 microns to 317 microns. The PAI layer on both the front and the back face is always 13 microns. The 25 microns of PAI film is responsible for the UL listing of 200 as tested by UL 1446. The construction is modeled after and similar to MW35 magnet wire. MW35 has a polyester base coat with poor thermal properties with an overcoat of PAI for thermal performance, chemical resistance, abrasion resistance, and low coefficient of friction.
Electrical Properties
The electrical properties of ELAN-Film HT-180 insulation are outlined and compared to competitive films of similar thicknesses in the accompany tables. Three conditions were applied to each film. The films/papers were first dried at 80 degrees C overnight to remove water. Dielectric breakdown was then measured and normalized on volts per mil. The films were then immersed in water for 24 hours at 25 degrees C. A third sample was placed in a 100% humidity chamber at 40 degrees C. Dielectric breakdown was then measured on each of these samples.
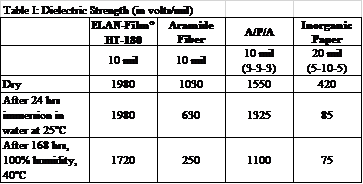
The aramide fiber and inorganic paper materials both started off with much lower dielectric breakdown than the film containing products. The papers are relatively porous due to the fibrous nature of the material leading to the low dielectric breakdown. The ELAN-Film HT-180 insulation as well as the laminate A/P/A start off much higher in average dielectric breakdown.
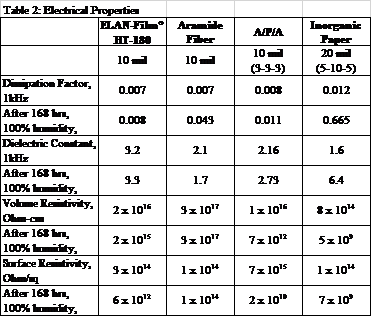
The impact of water on the paper products is evident. The aramide fiber paper loses approximately 40% of its dielectric properties after water immersion and 75% after exposure to the humidity cabinet. The inorganic paper behaved in a similar fashion with around 80% reduction in dielectric breakdown. The ELAN-Film HT-180 insulation is virtually unchanged in dielectric breakdown in both the water immersion and the humidity cabinet at 100% humidity.
The inherent advantages of this new insulation towards moisture resistance against the papers and laminate materials are evident. Dissipation factor is virtually unchanged after exposure to water while the other materials show a significant degradation. Dielectric constant, volume resistivity, and surface resistivity also show similar trends with little change in properties after moisture exposure.
Physical properties
Two key physical properties of the ELAN-Film HT-180 insulation are low moisture absorption and Freon extraction values. As mentioned in the electrical properties section, it does not absorb moisture like the paper materials. The paper products and related materials must be dried before use and stored in a protective way to avoid re-absorption of water before use. The ELAN-Film HT-180 insulation exhibits excellent Freon resistance compared to the laminate materials which use an adhesive that is not compatible.
One of the most important physical properties of ELAN-Film HT-180 insulation is its compatibility with most impregnating materials. Adhesion by cross hatch adhesion tester has been tested with alkyd resin, waterborne polyester, epoxy emulsion, unsaturated polyester with vinyl toluene, unsaturated polyester with diallyl phthalate (DAP), and epoxy resins. Excellent adhesion was observed with each of these chemistries.
Mechanical Properties
Robust mechanical properties are important for handling of electrical insulating films and papers. Mechanical insertion equipment exerts large forces on electrical parts that can give part failure during the insertion process. The ELAN-Film HT-180 insulation has a number of advantages over the competitive materials. Orientation is a big concern for the paper products including aramide fiber paper. Tensile and modulus are roughly half in the cross versus the machine direction. The ELAN-Film HT-180 insulation is roughly equivalent in the two directions and therefore can be used in any orientation.
Tear strength is also an important feature for mechanical properties. Abusive manufacturing techniques must not damage the solid insulating material. The accompanying photo shows a slot liner that was removed after final assembly by automated mechanical insertion equipment. No damage or cracks were observed even with the multiple of bends and strains put into the material. Tear strength is one such feature that dictates the abuse that can be tolerated. The ELAN-Film HT-180 insulation is significantly higher in tear strength than many of its competitors available in the marketplace.
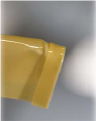
Processing Advantages
ELAN-Film HT-180 insulation is commercially competitive and offers overall cost saving opportunities for the customers due to improved storage, handling, and processing conditions. Due to its low moisture absorption, the need for preheating components and the extra care needed in processing, drying, packaging, and handling is eliminated. It has no restriction on material orientation during slitting and cutting operations, resulting in less waste and improved yields during component fabrication.
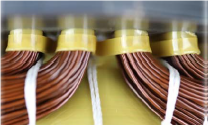
Due to its abrasion resistance, the down-times and cleaning efforts (e.g. no dusting or chalking during die cutting, slitting, creasing, and folding) are significantly reduced. It was also laser cut without char formation like aramide fiber paper and was fabricated with ultrasonic welding. The mechanical properties combined with the excellent dielectric strength allow customers an option to decrease the thickness of the insulation, enhancing apparatus designs while further increasing cost advantages. Further, customers have increased winding speeds due to excellent tear and tensile properties eliminating challenges with tearing and pinholing.
Summary
ELAN-Film HT-180 insulation is a unique, new flexible electrical insulating product that offers significant performance and productivity gains for end users. It is a composite of PET film coated on each side with a 13 micron layer of polyamideimide. The film combines a material from a well-known electrical application (magnet wire) with the ease of processing with PET.
Improvements in electrical, physical, mechanical, and processing properties give ELAN-Film HT-180 insulation significant advantages in the field. The paper products, including aramide fiber-based papers, easily absorb water in the paper voids, which leads to low dielectric strength and other issues. Film based materials are continuous castings without voids. Processing advantages include no restriction on orientation and no chalking or dusting during fabrication leading to less down-time for cleaning.
Acknowledgments
The authors would like to thank Novak Cvijanovic and Tan Nguyen of Elantas PDG for the materials preparation and testing. Parts of this article were adapted from a presentation at the 2018 Electrical Insulation Conference, San Antonio, TX, 17-20 June 2018. For more information, please visit www.altana.com/divisions/elantas.html.
About the authors
Dr Thomas Murray is Director of Research and Development. Stephen Tuckwell is Vice President and Business Line Manager. Marc Barmeier Business Development Manager — Emerging Technologies. All with Elantas PDG Inc. in St. Louis, MO, a division of the Altana Group based in Wesel, Germany.