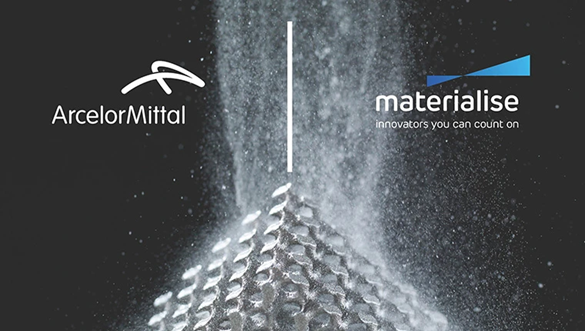
Additive manufacturing using metal powders is getting serious attention from ArcelorMittal, a leading global steel manufacturer with electrical steel and magnetic alloys in its portfolio. In June, it announced a partnering with Materialise to use its 3D print processor in ArcelorMittals’s new metal powder business. The move syncs with the company’s setup of an atomizer operation in Spain that paves the way for building a new business in high-volume production of metal powders for additive manufacturing.
In November 2023, ArcelorMittal declared its entry into the additive manufacturing market as a steel powder supplier. Located in Aviles, the industrial-scale inert gas atomizer can produce steel powders for AM technologies such as laser powder bed fusion, binder jetting and direct energy deposition with production startup early this year. It has a large batch-size capability, from 200 kg to 3 tons, and an initial capacity of 1,000 tons annually.
A new business unit, ArcelorMittal Powders, has been established to commercialize the output of the atomizer. The steel powders will be offered in size ranges suitable for all existing powder-based metal additive technologies in manufacturing industries such as aerospace, defense, automotive, medical and energy.
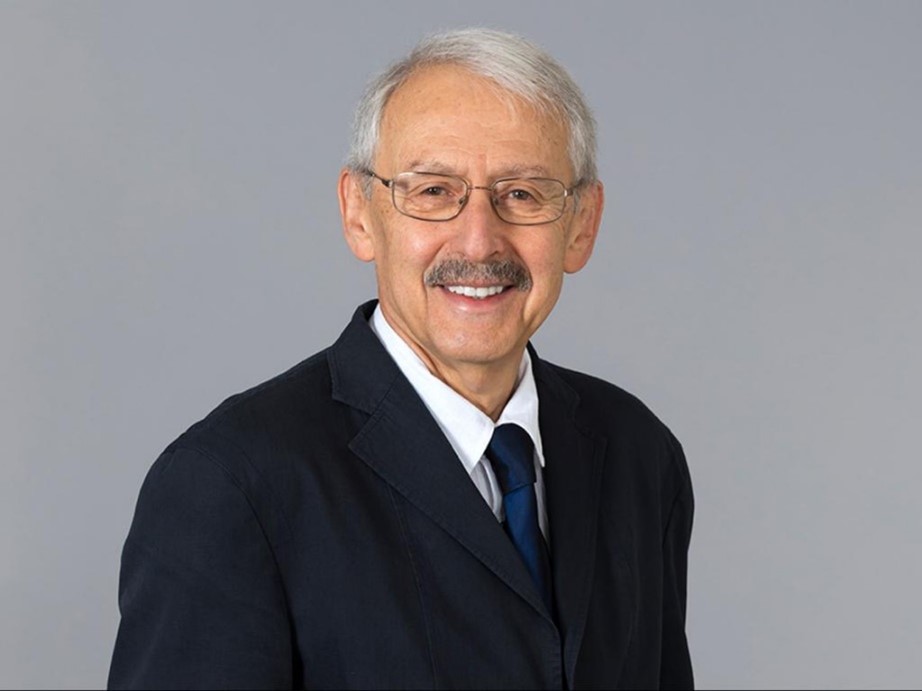
“We are proud to launch ArcelorMittal Powders, a new business unit that reflects our vision to be at the forefront of innovation and sustainability in the steel industry,” said Gregory Ludkovsky, CEO of global research and development of ArcelorMittal. “The additive manufacturing industry has grown phenomenally over the past decade and is expected to continue to grow in double digits over the next 10 years. While the production of steel powders is a new venture for ArcelorMittal, we are confident that our metallurgical expertise and solutions-based approach will provide our customers with the support they need to improve the quality and reliability of their additive manufacturing projects.”
“Additive manufacturing is an area we have been investing in and building our capabilities for several years, and we are now ready to scale up our production and offer our customers and partners a reliable and competitive source of high-quality steel powders,” noted Colin Hautz, CEO of ArcelorMittal Powders.
Marketed under the AdamIQ brand name, the product portfolio will include stainless steels, tool steels and low alloy steels including initially a dual-phase alloy equivalent to its 4140 product. Drawing on its metallurgical expertise, ArcelorMittal’s research and development team dedicated to AM technologies and steel powder production intends to add further steel powder products for customers to test this year.
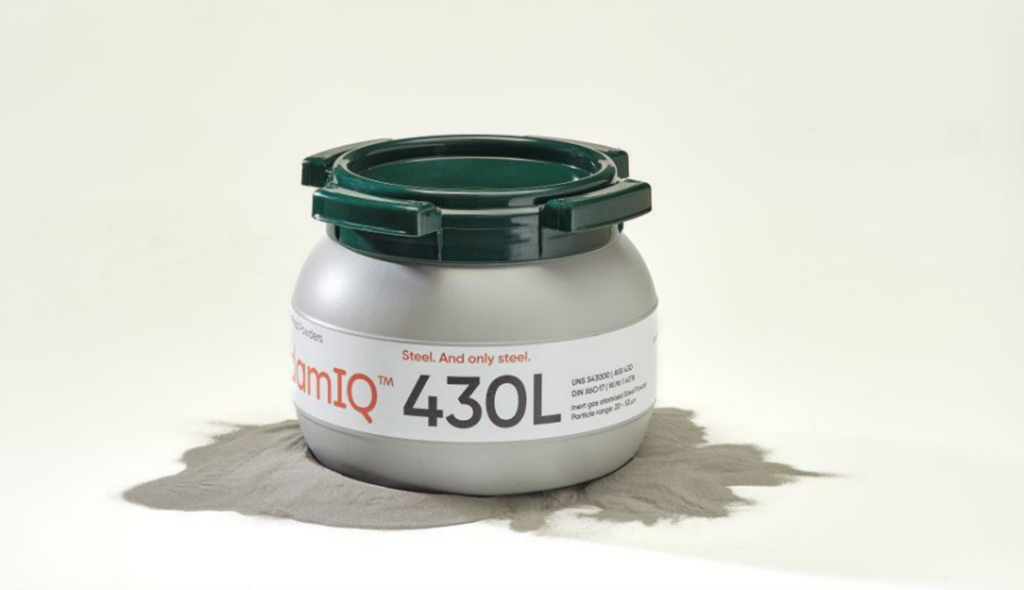
Already showing in the offerings is a ferritic stainless alloy, AdamIQ 430L, that can be used in brake disc coatings being developed to help automotive manufacturers comply with the EU7 regulation on particle emissions. A layer of powder deposited on the brake disc provides wear and corrosion resistance which significantly reduces the particulate emissions of braking.
Though not currently on the list, some design engineers likely will be asking particularly about one of the company’s alloys with significant magnetic properties: XC06 High Purity Ultra Low Carbon Magnet Steel. Standardly available as bulk solid plate up to 825 mm thickness, it is a soft ferromagnetic iron providing high saturation polarization, high permeability and low coercitive force. It is used in numerous high-tech magnet applications requiring highly specific and homogeneous magnetic properties including magnetic resonance imaging, MRI guided proton therapy devices, particle physics accelerators such as cyclotrons and synchrotrons, spectrometers and magnetic components such as cores and yokes. At this writing, however, Magnetics Magazine has not been able to ascertain the extent, if any, that it will become an AdamIQ product.
ArcelorMittal has been producing steel powders in a pilot atomizer at Aviles since 2018. With its dedicated research and development facilities and over 50 full-time researchers, the company’s metallurgists and engineers have developed a detailed understanding of the interactions between steel alloy design, atomization parameters, AM process parameters and the final properties of the printed parts.
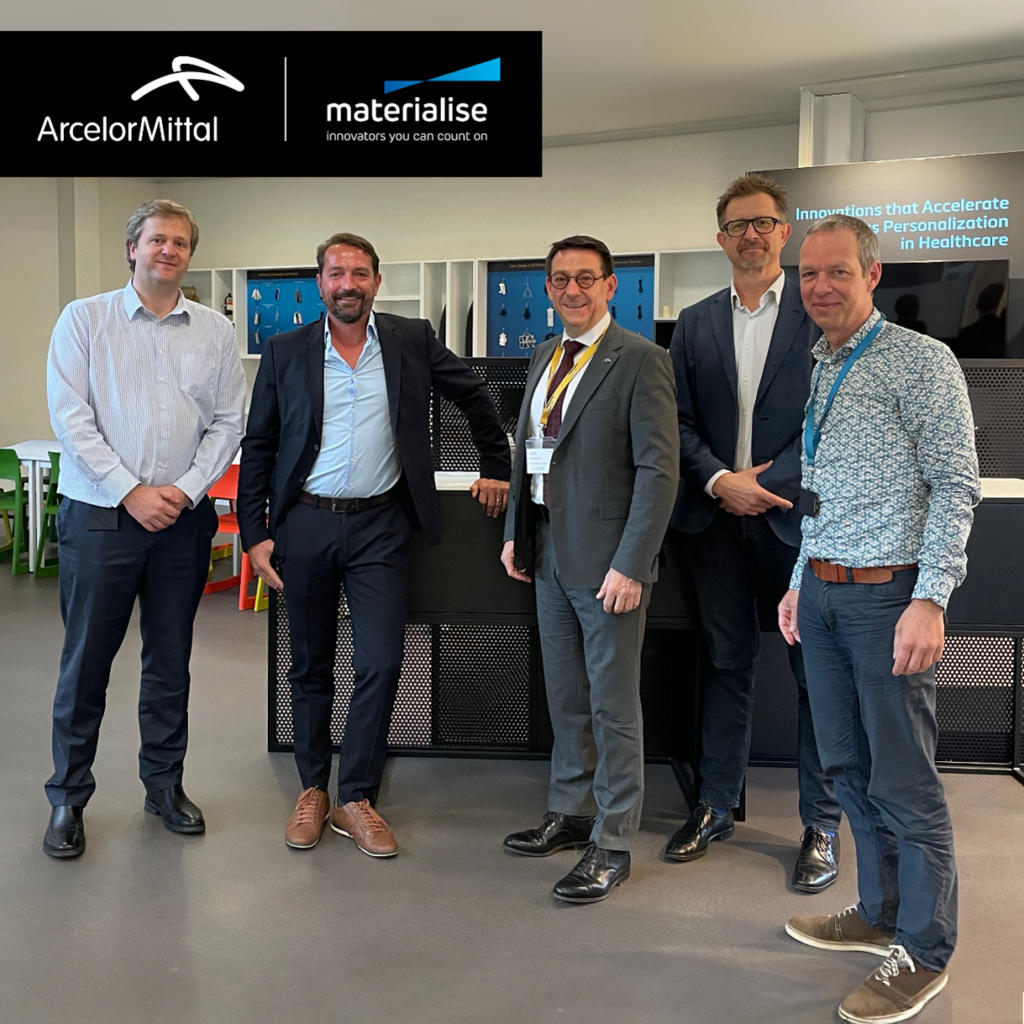
A new step in that direction came recently in an agreement with Materialise, a provider of 3D printing software and services based in Leuven, Belgium. Basically, ArcelorMittal will use Materialise’s build processor for 3D printers. Build processors link 3D printers with data preparation software, streamlining the additive manufacturing process from design to print. Materialise’s processor supports larger build volumes and more complex geometries than traditional processors so users can customize process parameters, streamline workflows and print faster.
“Our collaboration with Materialise supports our vision that the key to success in additive manufacturing is about finding the right blend of digital instructions and steel powders to deliver the best balance of quality and productivity in an application. Whether developing new applications with new alloys or proving the feasibility of new designs for existing applications through steel additive manufacturing, Materialise offers us a formidable channel to bring build instructions straight to the heart of a 3D printer,” said Aubin Defer, Chief Marketing Officer, ArcelorMittal Powders. For more info, see www.arcelormittal.com and www.materialise.com.